Laser cutting is a cost-effective and efficient process to cut sheet metal. It’s no wonder why laser cutting is gaining popularity in the fabrication and manufacturing industries. With the right equipment and materials, laser cutting can provide accurate and precise cuts while maintaining a high level of quality. Before laser cutting, there are a few important things to consider in order to ensure the best results. In this article, we will discuss what to consider before laser cutting sheet metal.
Safety Considerations
Eye protection
Safety When it comes to laser cutting sheet metal, eye protection is an absolute must. It is essential that you wear proper safety glasses that have been designed specifically to protect your eyes from the bright heat produced by the laser. Additionally, you should also make sure to keep other people in the vicinity out of direct view of the laser beam.
The high-intensity laser beam can cause serious damage to your eyes if it is not properly shielded and kept away from any bystanders. Depending on the type of laser being used, you may also need to wear a face shield to provide additional protection.
Ventilation systems
When it comes to laser cutting sheet metal, the importance of having proper ventilation systems in place cannot be overstated. It is essential to have an effective way to handle smoke and fumes created from the laser cutting process. This can be achieved by using an integrated ventilation system that takes in the hot air from the laser cutter, filters it and returns it to the environment at an acceptable emission level.
Fumes and smoke can be dangerous to both the operator and the surrounding environment and can be harmful to health. Furthermore, it is also important to consider dust and particles that get generated during the laser cutting process.
Regulations and codes
Safety When it comes to laser cutting sheet metal, there are a number of regulations and codes that must be adhered to in order to ensure safety and quality. First, the laser cutter must adhere to the set health and safety standards, such as laser safety requirements, to ensure the safety of operators and those in the area affected. Second, the laser cutter must meet industry codes for operation, such as the American Welding Society (AWS) and the American Society of Mechanical Engineers (ASME), in order to ensure the highest quality of the materials being cut.
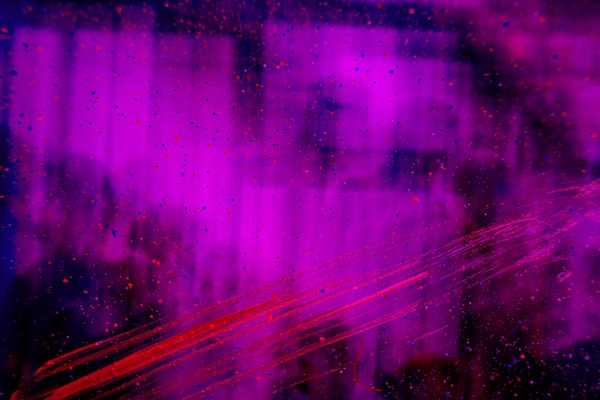
Cost Considerations of Laser Cutting Sheet Metal
Initial start up cost
sheet Metals When it comes to laser cutting sheet metal, the initial start-up cost is an important factor to consider. This cost generally consists of the purchase of the laser cutting equipment, materials and staff resources. There are various different types of laser cutting equipment available, and the costs will vary based on the precise specifications of the machine required.
For example, a machine that is able to accommodate larger pieces of sheet metal will naturally cost more than one that is designed for smaller pieces.
Maintenance and labor costs
Before you decide to go ahead with laser cutting sheet metal, it’s important to consider a few important factors. Cost is a big part of that decision. Laser cutting sheet metal can require a large upfront investment, depending on the volume you’re cutting.
- Do your research regarding laser cutter models and sheet metal types that are most suitable for your project. Different types of sheet metal will require different settings and make sure to read up about the different models available.
- Estimate the total cost of upkeep for the laser cutter. This should include not just the cost of the laser cutter itself, but also the maintenance and energy costs associated with running it.
- Consider if operating a laser cutter yourself is right for your budget. It is typically easier to outsource the job to an experienced professional to keep costs down.
- Check the capabilities of the laser cutter before starting a project. Each laser cutter should have different settings and features that will be necessary for different sheet metal tasks.
- Keep in mind that laser cutting can be a long process and might have associated labor costs. Make sure to factor in the time and cost it takes to finish the job.
Bulk purchasing costs
When it comes to laser cutting sheet metal, bulk purchasing costs can be an important factor in determining the overall cost of the process. bulk purchasing of sheet metal refers to the purchase of larger sheets of metal, generally in excess of 30,000 lbs, which can then be laser cut. Bulk purchasing sheet metal allows for economies of scale, as the larger sheet offers a significant cost savings over buying smaller, individual sheets.
Bulk purchasing also allows for more efficient use of the laser cutting machine itself, as the large sheet can be cut more quickly than if cutting individual sheets.

Types of Materials
Carbon steel
Carbon steel is one of the most common types of sheet metal used in laser cutting. It’s quite strong yet highly malleable, and its low melting point allows it to be cut with ease. Carbon steel also has high thermal and electrical conductivity, meaning you can make a perfect cut with a laser at a fraction of the cost.
When considering a laser cutter for cutting sheet metal, carbon steel is a great option. It’s also a versatile material, which can be used for jewelry, signs, and other artwork.
Stainless steel
When it comes to metal laser cutting, one of the most popular materials used is stainless steel. Stainless steel is strong and long-lasting, making it one of the best materials to work with. This is due to its corrosion-resistant properties, meaning it won’t easily rust over time.
Aluminum
When it comes to laser cutting sheet metal, aluminum is a very popular choice. The material’s high strength-to-weight ratio makes it very cost-efficient and the heat treatment possibilities make it ideal for a variety of applications, from aerospace parts and electronic enclosures to automotive components and consumer products. Additionally, its ductile nature causes it to bend and deform rather than crack or break, making it easier to form and shape.
When laser cutting sheet metal, one of the most important things to consider is the type of aluminum you are using. There are a variety of different alloys, each with their own properties.
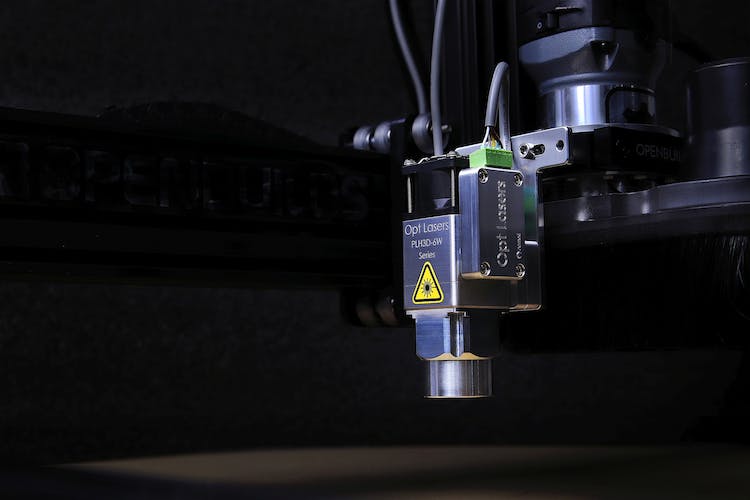
Design Considerations
Vector cutting versus raster cutting
When it comes to laser cutting sheet metal, there are two distinct techniques available: vector cutting and raster cutting. Vector cutting is the most commonly used method for laser cutting sheet metal and is typically used for complex shapes and patterns. Vector cutting works by moving the laser beam along a designated cutting path in the shape of the desired pattern.
This method is the most accurate and precise choice for laser cutting sheet metal as it ensures exact replication of the desired pattern. Raster cutting is a less precise laser cutting technique and is typically used for simpler shapes and curves.
Edge features
Don’ts When using laser cutting to cut sheet metal, edge features need to be considered. Edge features are the cross sections of the sheet metal that are produced through the laser cutting process. These features make up the overall shape of the sheet metal and can have a significant effect on the finished product.
When designing parts made from sheet metal, it is important to understand the different types of edge features that can be produced by laser cutting.
Overlapping shapes
Process When working with sheet metal and laser cutting, overlapping shapes are one of the most important design considerations to take into account. Overlapping shapes are essential for efficient, error-free metal laser cutting. This is because lasers will quickly and accurately cut through the spaces between the shapes, allowing for more intricate pieces that can be cut with uniform accuracy.
When designing metal pieces for laser cutting, overlapping shapes should be planned carefully in order to eliminate any potential gaps or inconsistencies between pieces.
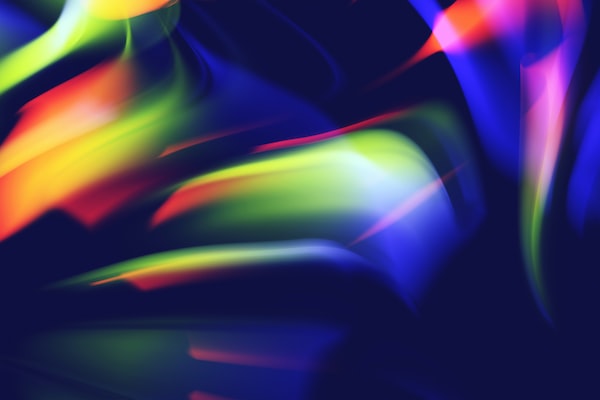
Conclusion
Benefits of laser cutting sheet metal
don’ts The main benefit of laser cutting sheet metal is its precision. Not only is the machinery highly accurate but it also allows for very intricate shapes and designs to be cut with ease. With a laser cutter, you can achieve complex geometries and accurate details which can be difficult to achieve with conventional tools.
Another benefit is the speed of cutting. Lasers can cut extremely quickly, meaning that larger projects can be completed in a relatively short amount of time.
What to consider before laser cutting sheet metal
Before you decide to use laser cutting to cut sheet metal, there are several factors to consider. Firstly, understand what type of laser cutting would best suit your metal project. There are various types of lasers that have different metal cutting capabilities.
The most common type of laser cutting is CO2 laser cutting, which is suitable for cutting a wide range of metals and alloys like stainless steel, aluminum, titanium, brass and so on. Other types of laser cutting include carbon dioxide, nitrogen and oxygen-based lasers. Each type has its own advantages and disadvantages with regard to power, cutting speed, surface finish, and cost.
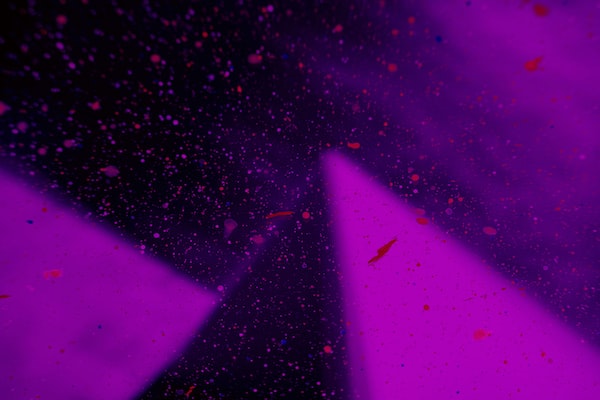