Quality Control in Laser Cutting is an important aspect of a machine operator’s job. It ensures that the material is cut in a consistent and accurate manner, producing top quality results. This is done by checking and controlling the laser cutter’s settings throughout the entire cutting process. In this article, we will provide an overview of the different capabilities of quality control available in laser cutting and show how they can be used to ensure the highest quality of cutting outcomes.
Different Quality Control Technologies
Visual Quality Assurance
Visual quality assurance is an essential part of understanding the capabilities of quality control in laser cutting. Quality control involves controlling and checking the cutting capacity and cut quality of the laser cutting materials, which means visual assessment is often needed. This can be done either manually, or through the use of high-tech monitoring equipment.
Manual assessment involves having experts use their eyes and experience to check for defects in the cut material. They usually look for cracks, uneven cuts, and general incorrect cutting dimensions.
Automated & Robotic Laser Cutting Quality Checking
When it comes to understanding the capabilities of quality control in laser cutting, there are a variety of different technologies available. Automated and robotic laser cutting quality checking is one such technology that helps with ensuring the accuracy and quality of laser cuts. Automated and robotic laser cutting quality checking is a process that employs robots and other automated equipment to inspect laser cuts for any flaws or imperfections.
The benefit of automated and robotic quality checking is that it eliminates the need for manual inspection which can be both time consuming and labour intensive.
Intelligent Monitoring Systems
The capabilities of quality control in laser cutting are incredibly important for ensuring that parts and products created by the process meet the required specifications. Different quality control technologies can be used to increase efficiencies, reduce waste, and overall produce higher standards for the products that are created. One of the most popular technologies is intelligent monitoring systems.
An intelligent monitoring system is a sophisticated way of ensuring that the laser cutting process is controlled and monitored while a part is being produced by the laser. This intelligent monitoring system uses a variety of sensors to detect any irregularities within the cutting parameters, such as any out of range cutting speeds or power settings. By detecting any changes quickly, the machine can adjust itself accordingly to ensure that the cutting quality is maintained.
How to Implement Quality Control Measures
Establishing Quality Control Standards
Establishing quality control standards is a critical step when it comes to laser cutting. Unlike other cutting machines, precise laser cutting requires precise guidelines and control measures to ensure a high degree of accuracy and quality. When it comes to laser cutting, the cutting capacity and the cut quality are two of the most important elements to consider in establishing quality control standards.
When it comes to the cutting capacity, it refers to the issues that arise due to the size and shape of the piece being cut. For example, larger pieces will require a larger working area that is able to cut the piece with precision.
Setting Up Visual Quality Assurance
Setting up visual quality assurance is one of the key aspects of implementing quality control measures for laser cutting. In this section, we’ll discuss the importance of quality control, explain how to set up a quality control process and outline the steps you can take to ensure the best quality end product. Laser cutting involves the use of a powerful laser beam to cut a variety of materials such as steel, aluminum, plastics and other non-metallic materials.
The accuracy of the cutting pattern created depends on the type of the laser used, the cutting capacity of the material, and the skills of the operator. Quality control measures must be taken to ensure that the final product conforms to the specifications of the customer.
Implementing Automated Quality Control Programs
Quality control is essential when it comes to laser cutting. It is important to understand the capabilities of the lasers and how to implement quality control measures. Implementing automated quality control programs can be a great way to ensure the cut quality is consistent and meets the required standards.
When it comes to laser cutting, there are typically two measures that need to be taken into account: the laser’s cutting capacity and the laser’s understanding of the material being cut.
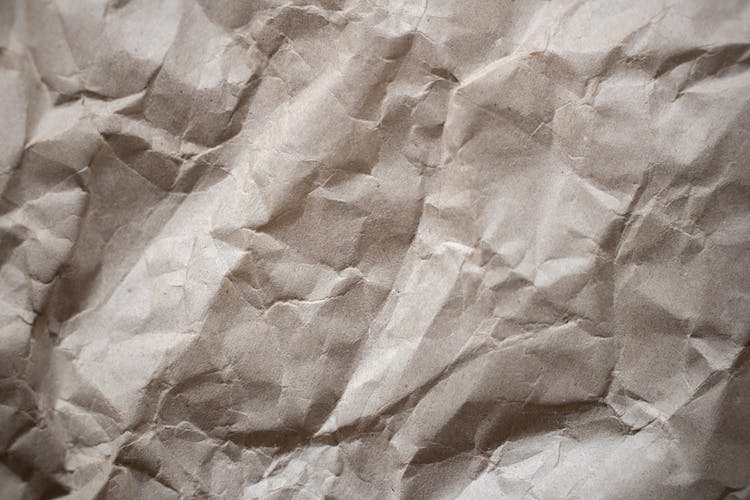
The Future of Quality Control in Laser Cutting
Adopting Advanced Technologies
Adopting Advanced Technologies for Quality Control in Laser Cutting As technology progresses and advances, so too does the process of quality control in the laser cutting industry. In recent years, we’ve seen a rapid increase in the capabilities and accuracy of laser cutter operators. Cutting tools have been improved, allowing for more precise cuts to be made in a shorter time frame.
Additionally, new cutting materials can also be used to create intricate details with greater precision. As well, the technology has changed dramatically over the years, giving us the capability of seeing better cut quality in ways that weren’t possible before.
Automating Quality Control
When it comes to ensuring the highest quality of Laser Cutting, automation is increasingly playing a key role. Automation is helping manufacturers reduce costs, increase product quality, and streamline their processes. In this blog, we’ll explore the capabilities of quality control in laser cutting and look at the future of quality control in this area.
Quality control is an essential tool for manufacturers who want to ensure the highest quality output from their laser cutting machines. Quality control ensures that the cutting process meets customer specifications and industry standards. Quality control is used in a number of ways, from simple visual inspections to automated tests and inspections.
Leveraging AI & Machine Learning
Leveraging Artificial Intelligence (AI) and Machine Learning (ML) for quality control in laser cutting is a rapidly growing field set to revolutionize the laser cutting industry. It brings a world of possibilities to ensure cut quality, optimize cutting capacity, and predict possible issues that may lead to downtime or scrap materials. AI and ML can be used to develop algorithms which can identify subtle defects in the cutting process.
These algorithms can be used to determine the optimal parameters for each part and even make adjustments on the fly.
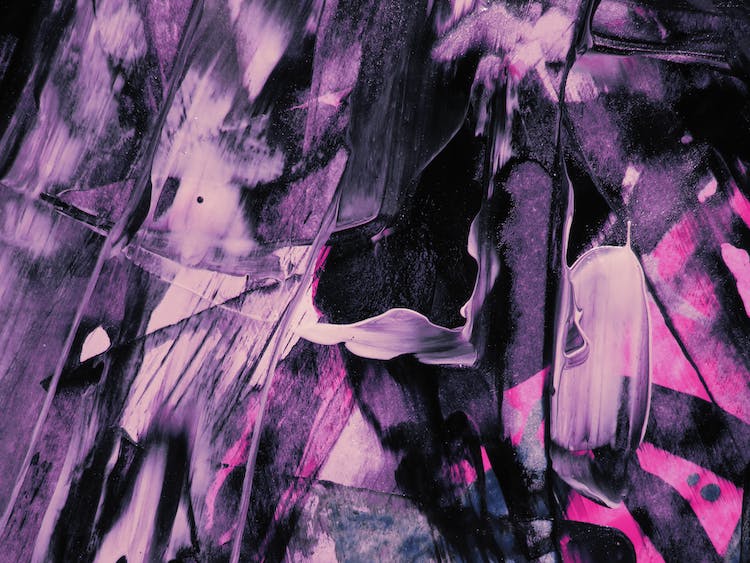
Conclusion
Recap of the Benefits of Quality Control in Laser Cutting
Quality control in laser cutting is an important, often overlooked factor in a successful laser cutting process. It entails understanding the capabilities of your laser cutting machine and the dynamics of different materials in order to ensure the desired results are achieved. Quality control involves the following steps: measuring cutting capacity, understanding the parameters that influence material cutting performance, inspecting the surface quality of the cut pieces for any abnormalities, testing the structural characteristics of cut pieces, and monitoring the cutting process to identify potential issues.
Summary of the Different Quality Control Technologies Used
In conclusion, understanding the capabilities of quality control in laser cutting is an essential part of achieving success in this production process. Quality control technologies such as intrusion detection, surface detection, and channeling detection are used to accurately identify and assess the cut quality of materials that are cut using laser technology. These technologies help to ensure that the cutting capacity, tolerance, and accuracy of the laser cutting systems are in compliance with the required production standards.
How Quality Control Can Improve Business Performance
When it comes to improving business performance with quality control, the capabilities of laser cutting have proven to be invaluable. With lasers, the cutting capacities are seemingly endless in comparison to manual cutting techniques with the added bonus of improved precision and accuracy. By having a better understanding of how the laser technology works, businesses can eliminate wasted time and energy while simultaneously improving the quality of their cuts.
One way that businesses can ensure they are getting the most out of their laser cutting capabilities is by investing in quality control measures.
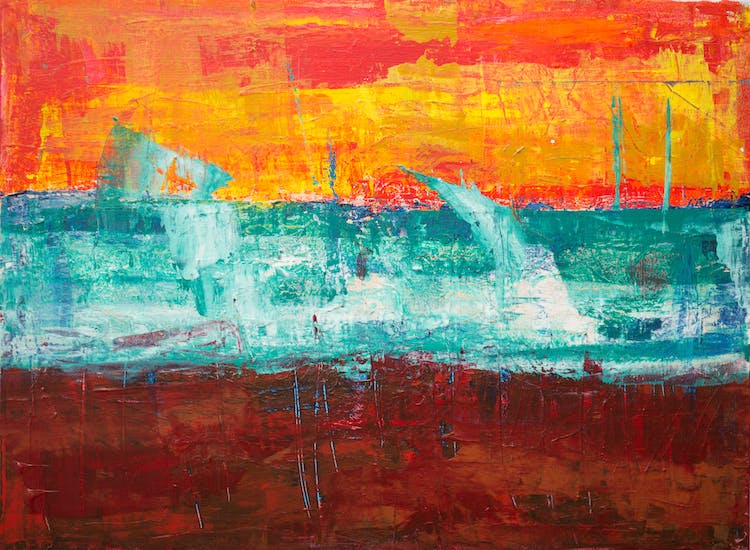