Laser cutting technology has become an essential tool for manufacturers across many industries. It offers a more precise and efficient way of cutting materials compared to mechanical methods. This article provides an introduction to the basics of laser cutting technology, including the different types of lasers and their applications, the benefits and limitations of laser cutting, and the safety precautions associated with it. Whether you’re a business owner looking to increase your efficiency or a hobbyist who wants to try something new, understanding laser cutting technology can help give you the edge you need.
Types of Laser Cutting
CO2 Laser Cutting
CO2 laser cutting is a type of CNC (Computer Numerical Controlled) machine that is used for fabricating custom designs with a thin, focused laser beam. This technology uses a laser to vaporize materials, resulting in a clean, cut edge. CO2 laser cutting is a type of thermal separation process, where a type of CNC machine uses an intensely focused, coherent stream of light to cut through metals, paper, wood, and acrylics.
Fiber Laser Cutting
Fiber laser cutting is a type of CNC (Computer Numerical Controlled) machine that uses an intensely focused, coherent stream of light to cut through metals, paper, wood, and acrylics. This fabrication process utilizes a thin, focused laser beam to carve out intricate designs from materials like metal, paper, wood and acrylics. Fiber laser cutting is a type of thermal separation process, where the laser causes the material to vaporize, resulting in a clean, cut edge.
This technology is extremely effective and accurate, as well as being fast and efficient.
YAG Laser Cutting
YAG laser cutting is a type of CNC (Computer Numerical Controlled) machine and fabrication process that uses a thin, focused laser beam to cut and etch materials into custom designs. This technology utilizes a laser to vaporize materials, resulting in a cut edge. It is a type of thermal separation process and uses an intensely focused, coherent stream of light to cut through metals, paper, wood, and acrylics.
In comparison to other types of cutting and etching technologies, such as plasma, waterjet, and flame cutting, YAG laser cutting has a greatly increased accuracy and repeatability.
Applications of Laser Cutting
Laser Cutting in the Automotive Industry
Laser cutting technology is an invaluable tool when it comes to automotive manufacturing. It’s a type of CNC (Computer Numerical Controlled) machine that helps in performing multiple operations and applications with precision and accuracy. It is a fabrication process that uses a thin, focused laser beam to cut and etch materials into custom designs.
The technology is highly versatile since it uses a laser to vaporize materials. This results in a cut edge with very detailed precision and accuracy. Laser cutting is a type of thermal separation process.
It is a type of CNC machine where an intensely focused, coherent stream of light is directed into the material and used to cut through metals, paper, wood, and acrylics.
Laser Cutting in Aerospace Manufacturing
Laser cutting is a type of CNC (Computer Numerical Controlled) machine which uses an intensely focused, coherent stream of light to cut through materials such as metals, paper, wood, and acrylics. It is a type of thermal separation process and a fabrication process that uses a thin, focused laser beam to cut and etch materials into custom designs. In aerospace manufacturing, this technology is often used to perform multiple operations and applications.
Laser Cutting in Medical Manufacturing
Laser cutting is a type of CNC (Computer Numerical Controlled) machine that uses an intensely focused, coherent stream of light to cut through metals, paper, wood, and acrylics. This type of technology uses a laser to vaporize materials, resulting in a cut edge. It is a fabrication process that uses a thin, focused laser beam to cut and etch materials into custom designs.
It has many applications, one of which is its use in medical manufacturing.
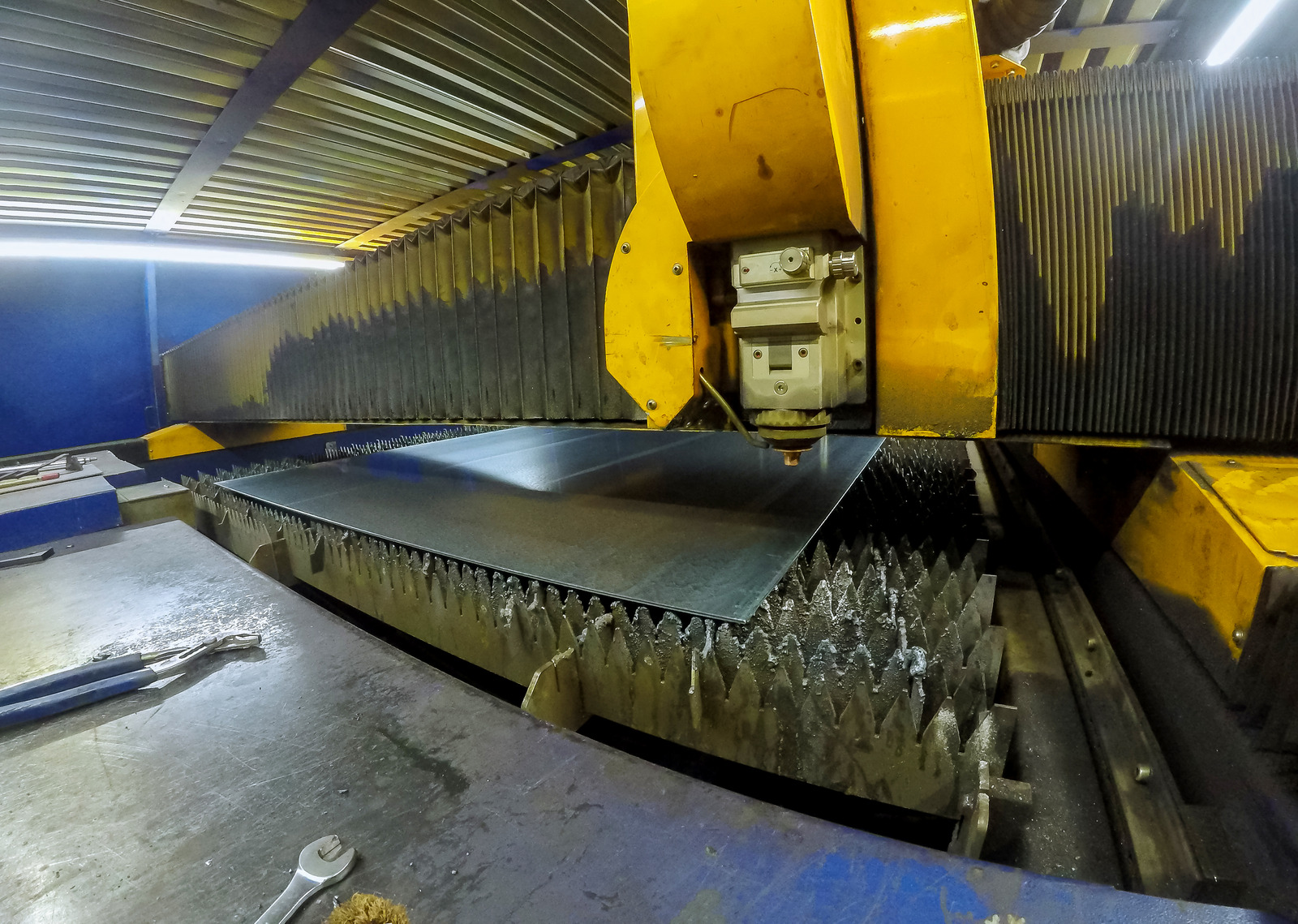
Process of Laser Cutting
Computer-Aided Design
Computer-Aided Design (CAD) is an essential component of laser cutting technology. CAD software is a type of Computer Numerical Control (CNC) machine which enables the user to design a template of the desired object and submit it to the laser cutter for fabrication. This type of CNC machine uses a thin and focused laser beam to precisely cut and etch materials into custom designs.
Laser cutting technology uses a laser to vaporize the materials, resulting in a smooth cut edge with a minimal amount of dust, sparks, or heat distortion.
Planning the Cut
When it comes to planning a laser cut, the process starts with gathering the necessary materials and preparing them for the cutting process. Every piece of material which is going to be cut by the laser machine should be of good quality and conditioned correctly. During the planning stage, it is important to consider the tolerances, material thickness, and the type of laser used.
One needs to be aware of the types of material that can be processed as well as the speed and accuracy of the cutting process.
Setting the Cut Parameters
When it comes to laser cutting technology, setting the cut parameters is a crucial part of the process. A type of CNC (Computer Numerical Controlled) machine, laser cutting is a fabrication process that uses a thin, focused laser beam to cut and etch materials into custom designs. It is a technology that uses a laser to vaporize materials, resulting in a cut edge.
Starting the Laser Cutter
Starting a laser cutter is the beginning of an often complex and sophisticated fabrication process. A laser cutting machine is a type of Computer Numerical Controlled (CNC) machine that is used to cut and etch materials into custom designs. It is a thermal separation process, meaning that it uses a thin and focused laser beam to vaporize the material resulting in a cut edge.
The laser cutter uses an intensely focused, coherent stream of light to cut through materials like metals, paper, wood, and acrylics.
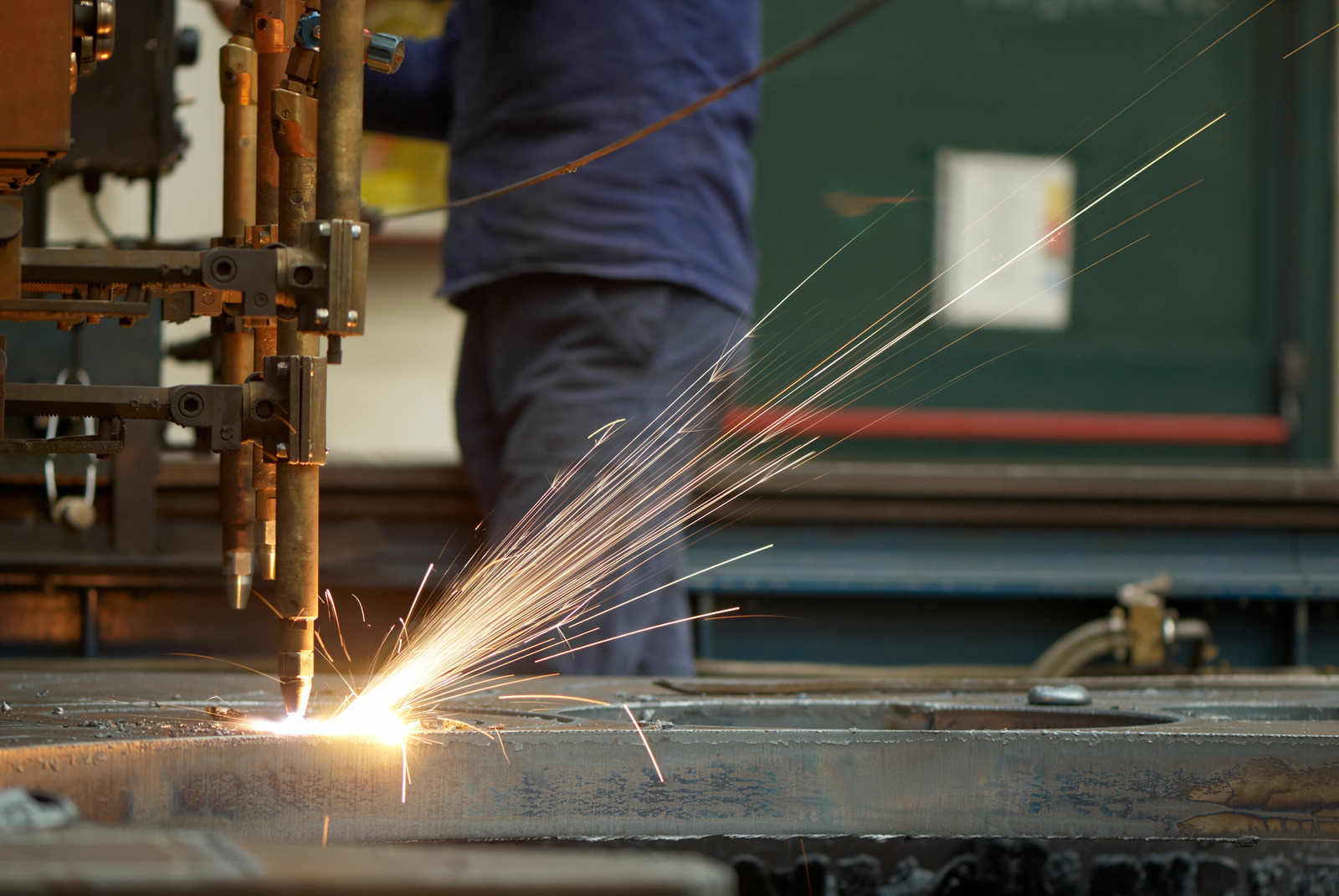
Safety Considerations for Laser Cutting
Protective Gear
When it comes to laser cutting technology, safety should always be a top priority. Protective equipment is an essential component of an effective laser cutting workflow. Wearing protective gear such as goggles, aprons, and respirators can help shield workers from the risks associated with laser cutting, such as laser radiation exposure, fire hazards, and particles from the materials being cut.
Ventilation Requirements
Ventilation Requirements When it comes to laser cutting technology, safety considerations must include proper ventilation. Laser cutting technology is a type of CNC (Computer Numerical Controlled) machine that uses a thin, focused laser beam to cut and etch materials into custom designs. It is a type of thermal separation process and technology that uses a laser to vaporize materials, resulting in a cut edge.
The machine, specifically a CO2 laser, also uses an intensely focused, coherent stream of light to cut through metals, paper, wood, and acrylics.
Conclusion
Benefits of Laser Cutting Technology
The benefits of laser cutting technology can’t be understated. It’s a type of CNC (Computer Numerical Controlled) machine that utilizes a fabrication process uses a thin, focused laser beam to cut and etch materials into custom designs with amazing accuracy and precision. It’s a technology that uses a laser to vaporize materials, resulting in a cut edge that is smooth, uniform, and exact.
Common Applications of Laser Cutting
Conclusion: The application of laser cutting technology is increasingly widespread, thanks to its ability to perform multiple operations and applications and its thermal separation process. As a type of CNC machine, it uses an intensely focused, coherent stream of light to cut through metals, paper, wood, and acrylics. As a result, this technology has revolutionized the manufacturing industry, as it allows for intricate and precise designs to be cut with relative ease and accuracy.