Welcome to our guide on understanding common laser cutting processes for zinc. In this guide, we will cover the basics of laser cutting and its importance in fabrication, as well as the different methods used to achieve the desired result when cutting zinc. We will also review the advantages and disadvantages of each process from an economic and environmental perspective. Finally, we will conclude by discussing best practices for safely utilizing these procedures and how to avoid common mistakes. By the end of this guide, you should have a better understanding of how to laser cut zinc for successful and effective results.
Identifying Different Laser Cutting Processes
Oxygen Cutting
Oxygen cutting is one of the most common laser cutting processes used to cut zinc and other materials. In this process, a beam of laser energy is focused onto the material, and oxygen is used to blow away the incandescent particles that are heated and removed when the laser is applied. This allows for a clean and precise cut that is uniform and consistent.
Nitrogen Cutting
processes Nitrogen cutting is one of the common laser cutting processes for zinc. This process involves using a laser beam to cut through the zinc as if it were cutting through air. The laser beam is directed at the material and the heat from the laser is generated to create a kerf, or a small incision, in the material.
Once the laser has created the incision in the material, nitrogen gas is then used to blow away the molten material, eliminating the need for a separate cutting tool to do the work.
Flame Cutting
Flame cutting is a cost-effective and common laser cutting process for zinc. This process is most often used for thick metal sheets and creates a high quality, smooth cut. This cutting method uses a laser to heat the metal until it reaches its melting point.
When the metal has reached its melting point, a heated gas, such as oxygen, is used to blow away the molten metal, leaving a clean cut edge. The amount of heat generated is controlled by the power of the laser, gas purity and the arrangement of nozzle used for cutting.
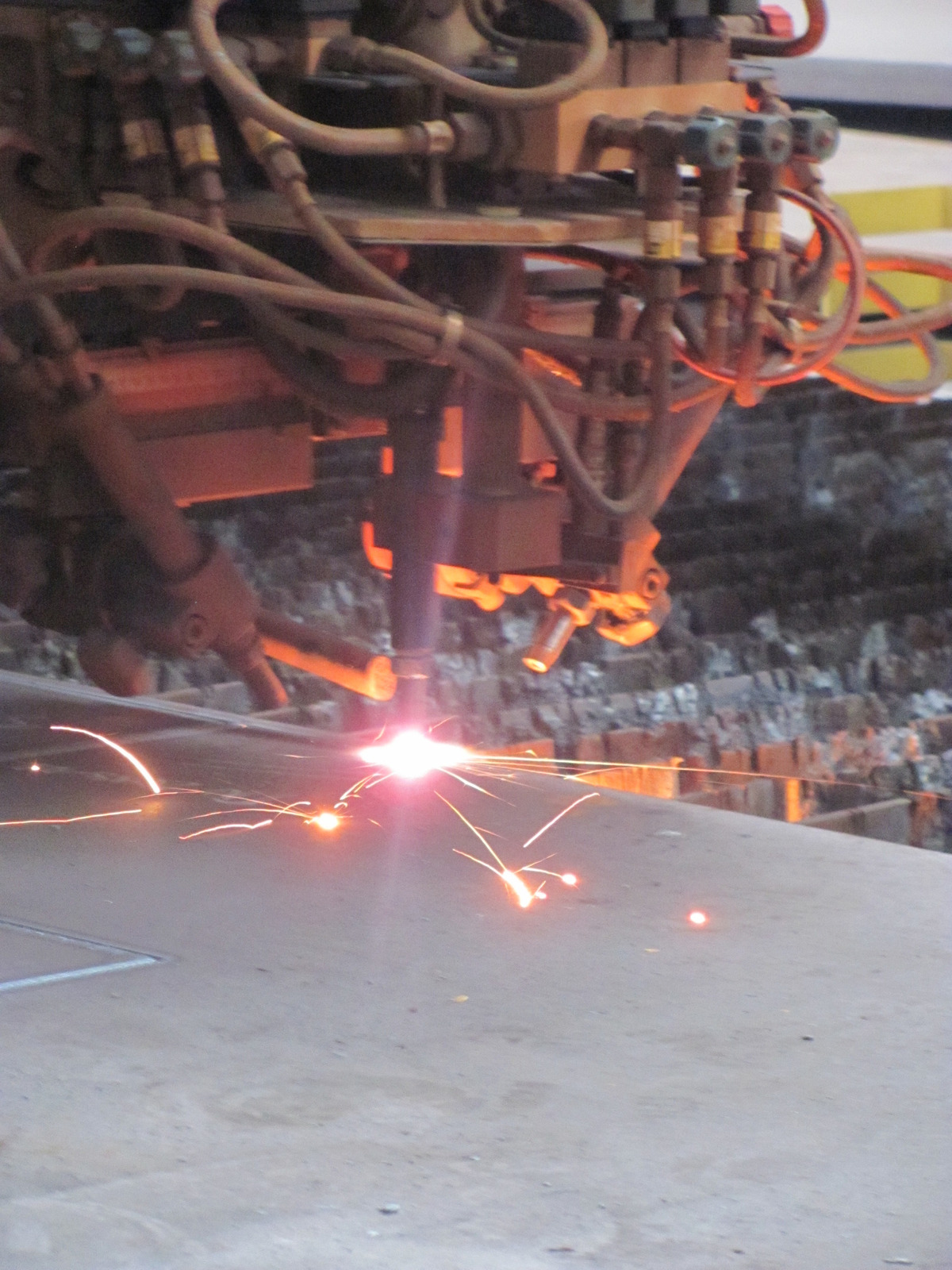
Comparing Different Laser Cutting Processes
Oxygen Cutting
Oxygen Cutting, one of the common laser cutting processes employed to work with zinc, is a process in which an oxygen jet is used to cut or engrave the material. The process is powered using laser-generated energy, and the oxygen jet is used to create a controlled flow of oxygen. This flow is directed precisely at the surface of the material, allowing for accurate cutting or marking of the material’s surface.
The process involves heating the material using the laser beam, causing a reaction that has the oxygen jet further heat and vaporize the material. This vaporization of the material is what allows for the cutting or engraving of the material.
Advantages
When it comes to working with metals, laser cutting is one of the most common and efficient options for those who want to achieve precise and accurate results. It is the ideal option for complicated cutting and engraving projects, and it can be used to work with a variety of materials, such as zinc. Laser cutting processes for zinc offer several advantages, including speed and accuracy.
Unlike other cutting methods, laser cutting is incredibly precise and quick. That accuracy ensures that tight tolerances can be met with ease, and that waste is eliminated in the process.
Disadvantages
When it comes to cutting zinc – many people think of laser cutting as the way to go. And it’s true that laser cutting can produce great results for many types of applications with this metal. But as with any machining process, there are advantages and disadvantages to consider.
When it comes to disadvantages of laser cutting zinc, the most notable are related to the complexity of the process. Laser cutting requires a high degree of precision and can often be difficult to produce intricate shapes and clean cuts.
Nitrogen Cutting
Nitrogen cutting is one of the most common laser cutting processes for zinc. This process works by providing a nitrogen assist gas, which helps cool the material as it is being cut. This process is usually done with a high-powered carbon dioxide laser, which is capable of creating intricate shapes and detailed parts with a high level of accuracy.
The nitrogen assist gas also helps to decrease the oxidation of the material during the cutting process, which prevents any smearing or warping in the finished product.
Advantages
When it comes to laser cutting zinc, there are several processes to choose from, each with its own advantages and disadvantages. Understanding each of these common laser cutting processes is essential when it comes to making the best choice for the intended application. Comparing features such as edge finish, speed, and capabilities in material thickness, can help determine the most suitable process.
- Heat Distortion Resistance: Laser cutting can improve the heat resistance of zinc, providing better resistance to warping and deforming due to hotter temperatures.
- High Precision: Laser cutting can precisely cut components with extremely precise shapes.
- Durability: Zinc components that are cut with lasers are known to have better longevity due to the reduced stress levels in the material.
- Tighter Control: Lasers can be easily controlled to allow for precise and accurate cutting with faster results.
- Cost Savings: With fewer raw materials required, laser cutting costs can be reduced without sacrificing quality.
Disadvantages
When it comes to cutting processes for zinc, there are some significant disadvantages to using laser cutting. The most significant of these is the cost. Laser cutting zinc takes considerably more power than cutting other materials and as a result, it is usually much more expensive.
Additionally, laser cutting zinc produces more heat that can potentially cause warping and melting of the material. It is more difficult to achieve the desired effect with a laser cutting process than with traditional hand tools, as well.
Flame Cutting
Laser cutting of zinc metal is becoming a more common process for many applications. One of the most popular cutting processes for zinc metal is flame cutting. Flame cutting uses a laser to heat the zinc metal to a very high temperature and then cut the metal using a jet of compressed air or oxygen.
The laser is used to heat the metal up to a very high temperature, which causes the metal to flatten and split into small pieces. The jet of compressed air or oxygen then takes the pieces and disperses them. Flame cutting is often the preferred process for cutting thick or hard metals because it is the most cost effective and fastest way to achieve the desired outcome.
Advantages
Advantages of Using Laser Cutting Processes for Zinc: Laser cutting processes for zinc provide numerous advantages for users. For example, laser cutting is fast and efficient, meaning that it can quickly cut through any material at an incredibly precise rate. This makes it an excellent choice for cutting intricate and sophisticated designs into metal.
Disadvantages
When it comes to laser cutting of zinc and other metals, there are several distinct processes that are available. While any cutting process comes with advantages and disadvantages, understanding the additional drawbacks associated with laser cutting processes for zinc is important for successful and cost-effective outcomes. One of the primary disadvantages of laser cutting zinc is the additional cost.
Laser cutting processes for zinc require more energy and precision, meaning that the cost of consumables, equipment, and maintenance is likely to be higher than other, more standard cutting processes.
Prepping Zinc for Laser Cutting
Cleaning Zinc Surface
Cleaning the surface of zinc before laser cutting is an important part of the process. Proper cleaning ensures that the laser cutter will be able to cut accurately and that the parts created from the cutting are clean, with no debris left behind on the surface. When cleaning zinc for laser cutting, it is important to start with a clean surface.
Any dirt, oil, or debris left on the surface can significantly reduce the precision and accuracy of the laser cutting process.
Marking Zinc Surface
cutting process Marking the surface of zinc before laser cutting is an important step to ensure that your project turns out just right. This is because the markings act as a guide for the laser, indicating where the cuts should be made. It also allows you to easily check the accuracy of the cuts and make adjustments if needed, as well as give you an idea of how the finished product will look.
Applying Gap Powder
processes Applying Gap Powder When it comes to laser cutting zinc, applying gap powder is an important part of the prepping process. Gap powder acts as a barrier between the metal and the laser beam, preventing it from reflecting off of the metal. This protective layer also serves to prevent warping or discoloration.
Gap powder is usually a carbon-filled powder that is applied to the zinc with a electrostatic gun prior to cutting.
Safety Considerations
Eye Protection
One of the safety considerations when undertaking laser cutting processes for zinc is the importance of protecting your eyes. This is because the intense light from the laser can cause permanent eye damage if it is directed towards your eyes. The intensity of the laser beam also depends on the type and wattage of laser used for the cutting process.
Ideally, if you are using a laser with a high wattage, it is recommended that you wear additional protection, such as protective goggles or a face shield.
Protective Clothing
When it comes to laser cutting of zinc, protective clothing is an essential and necessary step to follow. One should always wear specialized protective clothing while operating the laser cutter. This is because the laser process emits a strong light and can be damaging to unprotected skin.
It can also produce hazardous splinters that could easily penetrate the skin. Protective clothing can consist of heavy-duty goggles, face shields, safety masks and safety gloves that provide the highest level of protection.
Respiratory Protection
When it comes to laser cutting and engraving processes involving zinc, safety must always be a priority. Taking the proper safety precautions is essential for any laser cutting project involving zinc. One of the most important safety considerations involves respiratory protection.
When laser cutting zinc, certain fumes and particles can be produced and can be harmful if inhaled. To protect yourself from these fumes and particles, the use of a protective respirator, such as the ones available for purchase at welding supply stores, is essential. These respirators have dual layers of filters.
Conclusion
laser cutting processes In conclusion, laser cutting is an efficient and precise process that is often used to cut and engrave materials, including zinc. Laser cutting can be used to create complex parts, but it takes a skilled operator to ensure the quality of the cuts. In general, all laser cutting processes involve a beam of energy that is directed at the material in order to cut or engrave.
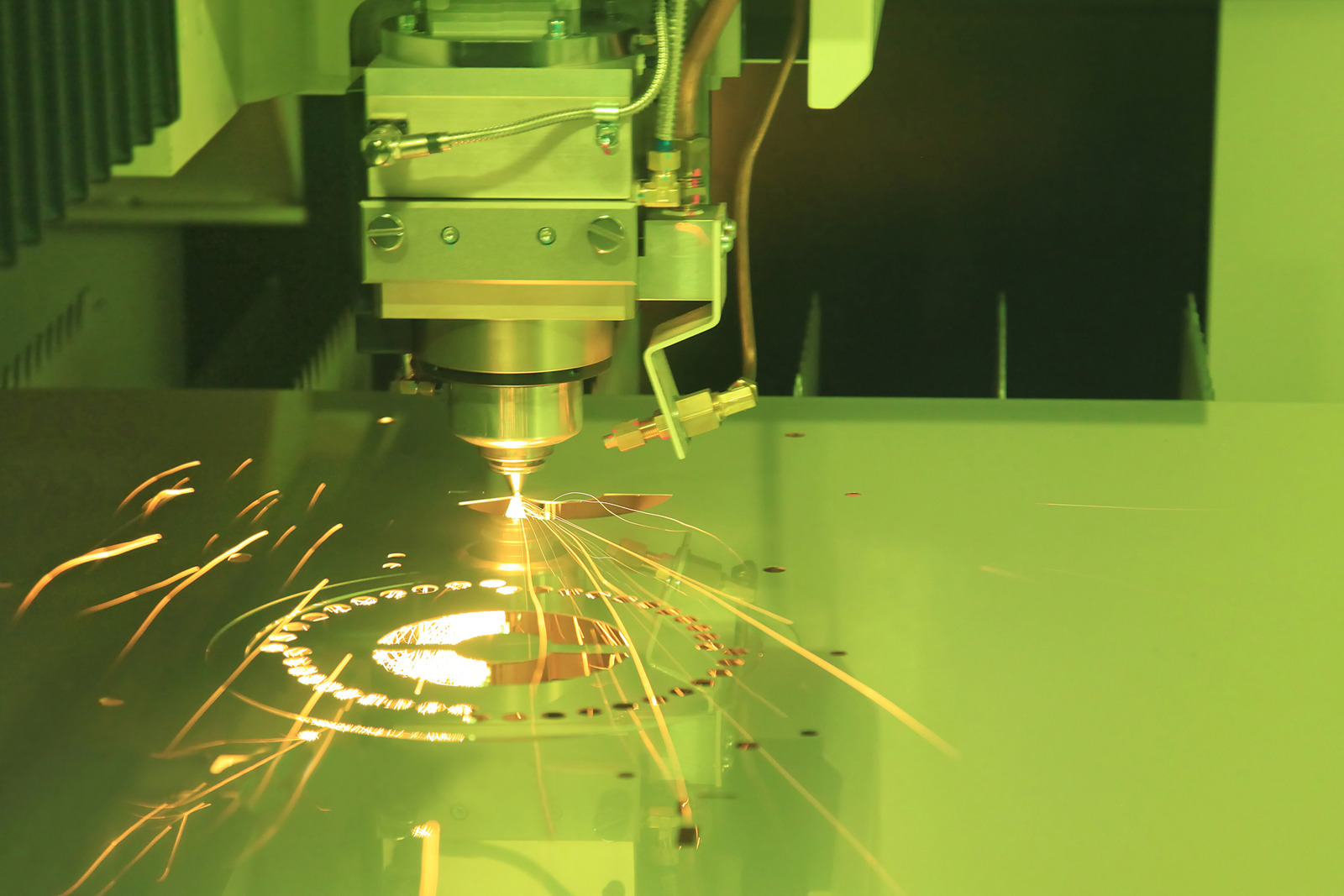
Conclusion
Conclusion: Laser cutting and laser engraving processes are extremely useful for creating intricate designs and components out of common zinc materials. The laser cutting process is incredibly versatile and can be used for creating things from simple, two-dimensional shapes to more intricate, three-dimensional structures, which makes it an ideal solution for a variety of applications and industries. Laser cutting machines also offer a more precise cutting process, meaning that the quality and detail of the final product is much higher than if using other methods.
When using this method you must take into account the laser power and scan speed to ensure the best possible results, especially when dealing with components made of delicate or thicker materials.