Are you looking for ways to cut costs without sacrificing quality when laser cutting sheet metal? This guide provides a few helpful tips on how to save money when laser cutting sheet metal. With these tips, you will be able to reduce expenses and still produce high-quality results.
Identifying Opportunities to Save Money
Choosing the Right Laser Cutting Machine
process When it comes to saving money when laser cutting sheet metal, choosing the right laser cutting machine is essential. The type of machine you choose should depend on the size of the material, the type of material you’re cutting, the thickness of the material, your budget, and the type of laser cutting process you intend to use. Knowing all these factors will help you make the right choice when shopping for a laser cutter that can produce the best results.
Understanding the Cost of Cutting Sheet Metal
When it comes to laser cutting sheet metal, one of the most important things to understand is the cost of cutting. Knowing the various costs associated with laser cutting sheet metal can help you identify opportunities to save money when getting the job done. The cost of laser cutting sheet metal depends on a variety of factors, such as the type of sheet metal being cut, the complexity of the pattern, and the size of the project.
The thickness of the sheet metal also plays a role in the cost of laser cutting. The cost of laser cutting sheet metal also depends on the type of laser cutter being used. Different laser cutters have different capabilities, so it’s important to choose the right one for the job.
Estimating the Full Cost of a Laser Cutting Job
Estimating the Full Cost of a Laser Cutting Job Laser cutting of sheet metal is a popular way to produce precision parts with minimal time and effort. Laser cutters use a focused beam of light to precisely cut and engrave intricate patterns into metal and other materials.
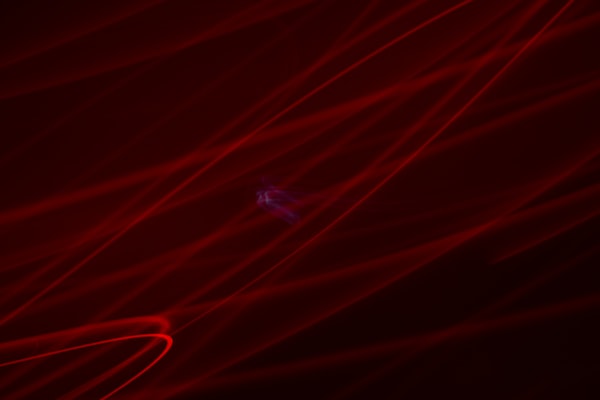
Adjusting Laser Cuts for Maximum Cost Efficiency
Adjusting Kerf Widths and Pass Depths
When laser cutting sheet metal, adjusting the kerf widths and pass depths can be an effective way to save money. Kerf widths and pass depths refer to how deep a laser beam engraves or cuts into the material and how much of the material is being lost in the process. The two main options for these settings are narrow kerf widths and shallow pass depths, or wider kerf widths and deeper pass depths.
Choosing the Right Focusing Optics for the Project
Choosing the right focusing optics for a laser cutting project can be a crucial step in saving money. Focusing optics are the lenses through which the laser beam in a laser cutter is focused. If the wrong focusing optics are used, it can lead to either a poor quality cut or increased costs due to extended job times or wasted material.
When choosing the right optics for a sheet metal laser cutting project, there are several key factors to consider.
Utilizing Tabbing to Minimize Cut Length and Scrap
When it comes to laser cutting sheet metal, one of the most important ways to save money is to use tabbing. By adding small “tabs” to pieces in the shape of a star or a triangle, the laser cutter will have less material to cut through and thus, will cut down on wasted material, or scrap. The tabbing method allows for the laser cutter to cut through the material with maximum accuracy, and also for less energy to be used as the laser cutter does not have to expend extra power to battle against thicker material.
Optimizing Component Design for Laser Cutting
Understanding Laser Cutting Tolerances and Capabilities
Laser cutting is a process that uses a highly focused beam of light to cut or engrave a material. Laser cutters are often used to cut sheet metal because they offer precise and repeatable cuts that produce clean edges. Many industrial processes rely on laser-cut sheet metal, from aircraft manufacturing and automotive components to medical devices and kitchen appliances.
When it comes to customizing sheet metal parts through laser cutting, it is important to understand the different tolerances and capabilities of the laser cutter you will be using. Different types of laser cutters have different precision levels and can handle different thicknesses of materials.
Designing Components to Minimize Material Usage
Designing components with laser cutting in mind can help you save money when laser cutting sheet metal. Laser cutting is a precise and efficient way to create components from sheet metal. By optimizing your component designs for laser cutting, you can help minimize material usage and overall cost of the finished product.
The most important thing to consider when designing components for laser cutting is the layout of the piece. If you’re laser cutting a flat sheet, always arrange your components in the most efficient layout that’s possible. This might involve nesting or grouping components together to minimize the amount of wasted material.
Leveraging Nesting Software to Optimize Material Placement
Nesting software plays an important role in optimizing the placement of material for laser cutting sheet metal. This software is extremely helpful when it comes to cutting materials quickly and efficiently in the least amount of time. This is especially true when dealing with sheet metal, as there are often limited shapes and sizes that can be efficiently cut.
By nesting the sheet metal pieces together and optimizing their placement, it is possible to reduce both the number of cuts required and the amount of time it takes to finish the project.
Tracking Laser Cutting Costs
Using Subcontractors to Streamline the Production Process
One of the most effective tips to save money when laser cutting sheet metal is to outsource the production process. Many companies benefit from using subcontractors for laser cutting, especially for more complex projects. Subcontractors specialize in certain types of laser cutting and can often work faster than an internal team, reducing production time and costs.
This allows you to focus on other aspects of the project and segment out the laser cutting process. Additionally, subcontractors have access to more specialized equipment, such as higher-power lasers, that often greatly increases the efficiency of the laser-cutting job.
Tracking Materials and Labor Costs Over Time
cost When using a laser cutter for sheet metal cutting, one of the best ways to save money is to track your materials and labor costs over time. Depending on the complexity of the job and the configuration of your laser cutter, you may need to track different aspects of the fabrication process, such as material choice, speed, and power settings. Tracking these cost elements over time can help you better understand how they all factor into the cost of the laser cutting job.
Utilizing Estimating Software to Budget for Projects
Having a hard time keeping track of your laser cutting costs? There are plenty of ways to save money when laser cutting sheet metal. One such method is by utilizing estimating software to budget for projects.
Estimating software is like a digital inventory system that records your costs and track activity from your laser cutter. This information can then be used to create a budget for each project. The software can help you make smarter decisions about material choices and the amount of time needed for each project.
You can better calculate the cost of cutting each piece of sheet metal, the cost of energy and other items such as consumables and machines required.
How can I reduce the cost of sheet metal parts?
There are many ways to save money when laser cutting sheet metal parts. First, it is important to identify the right laser cutter for the job. Different laser cutters are designed for different types of sheet metal, and levels of detail and accuracy. Carefully evaluating the job requirements can help ensure that the right machine is chosen for the job.
- Choose Thick Sheet Metal – One of the easiest ways to save money on sheet metal parts is to choose a thicker gauge. Thicker sheets are more durable and offer more stability and strength for complex designs.
- Choose an Economically Crafted Option – Look for laser cutting processes that are designed to reduce the overall cost of the materials and the labor involved. Specialty processes such as precision coining, welding and notching can help minimize cost and maximize appearance and performance.
- Minimize Material Waste – Choose laser cutting processes that minimize material waste. For example, laser interlock nesting allows parts to nest in a laser cut sheet of material, minimizing material waste and cost.
- Use the Right Accessory Parts – Using the right accessory parts can make all the difference in cost savings when it comes to sheet metal cutting. Accessory parts such as jigs and fixtures can help you with cost saving design ideas and material layout to achieve the most cost-effective outcome.
- Look for In-House Solutions – Many laser cutting shops offer in-house services that can help you save money on sheet metal parts. Cutting, pressing and forming of sheet metal can all be done in-house, saving you time and money.
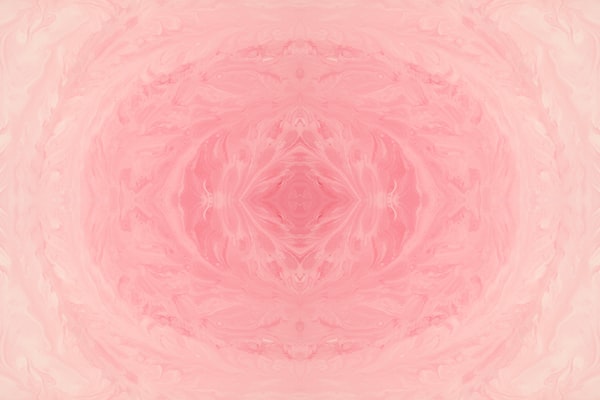
Conclusion
Summary of Main Points for Saving Money on Laser Cutting Sheet Metal
In conclusion, these are some tips to help save money when laser cutting sheet metal. First, understanding the different types of lasers and materials available for cutting can help to reduce the cost of laser cutting and engraving. Second, research the vendor to find the most cost-effective supplier for the project.
Third, batching orders together can help to increase quantity discounts. Finally, avoiding excessive machining and mitigation steps can reduce labor costs.
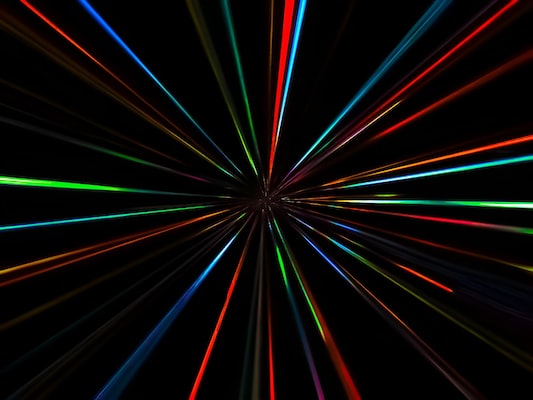