Automated quality control is an essential component of the manufacturing process. Laser cutting is one of the most cutting-edge production methods and automated quality control can be a great way to ensure that products are created efficiently and to the highest standards. This article will examine the benefits of automated quality control for laser cutting, from improved quality assurance processes to reduced labor costs.
Reduced Operator Error
Reduced Eye Fatigue
When it comes to laser cutting, human error can be a big issue. Even the most attentive operator can accidentally make mistakes, leading to costly production issues and delays. Fortunately, automated quality control can help reduce these errors.
One specific benefit of automated quality control is reduced eye fatigue. Operating a laser cutting machine involves staring at a computer monitor for long periods of time, which can lead to eye fatigue. Over time, the operator may begin to miss small details, leading to problems such as inaccurate cuts or incorrect measurements.
With automated inspection, the machine can quickly detect any errors that may be present, alleviating the need for long periods of intense concentration.
Faster Re-Focus Time
quality control One of the primary benefits of automated quality control for laser cutting is a decreased re-focus time. Instead of having an operator manually inspect laser cut parts for defects or accuracy, automated quality control systems can quickly and accurately detect the slightest errors. Automated quality control systems can also detect changes in the cutting process that an operator may not pick up.
For example, if the laser cutter loses power, or if there has been a shift in the cutting process, the automated quality control system can quickly detect and adjust the focus accordingly.
Improved Product Quality
operators One of the main benefits of automated quality control for laser cutting is improved product quality. By using automated inspection, laser cutting operators are able to quickly identify any errors and make corrections early in the process. This can reduce material wastage, as well as increasing the accuracy of the final product to meet customer specifications.
With automated quality control, laser cutters can quickly and accurately cut intricate shapes and patterns.
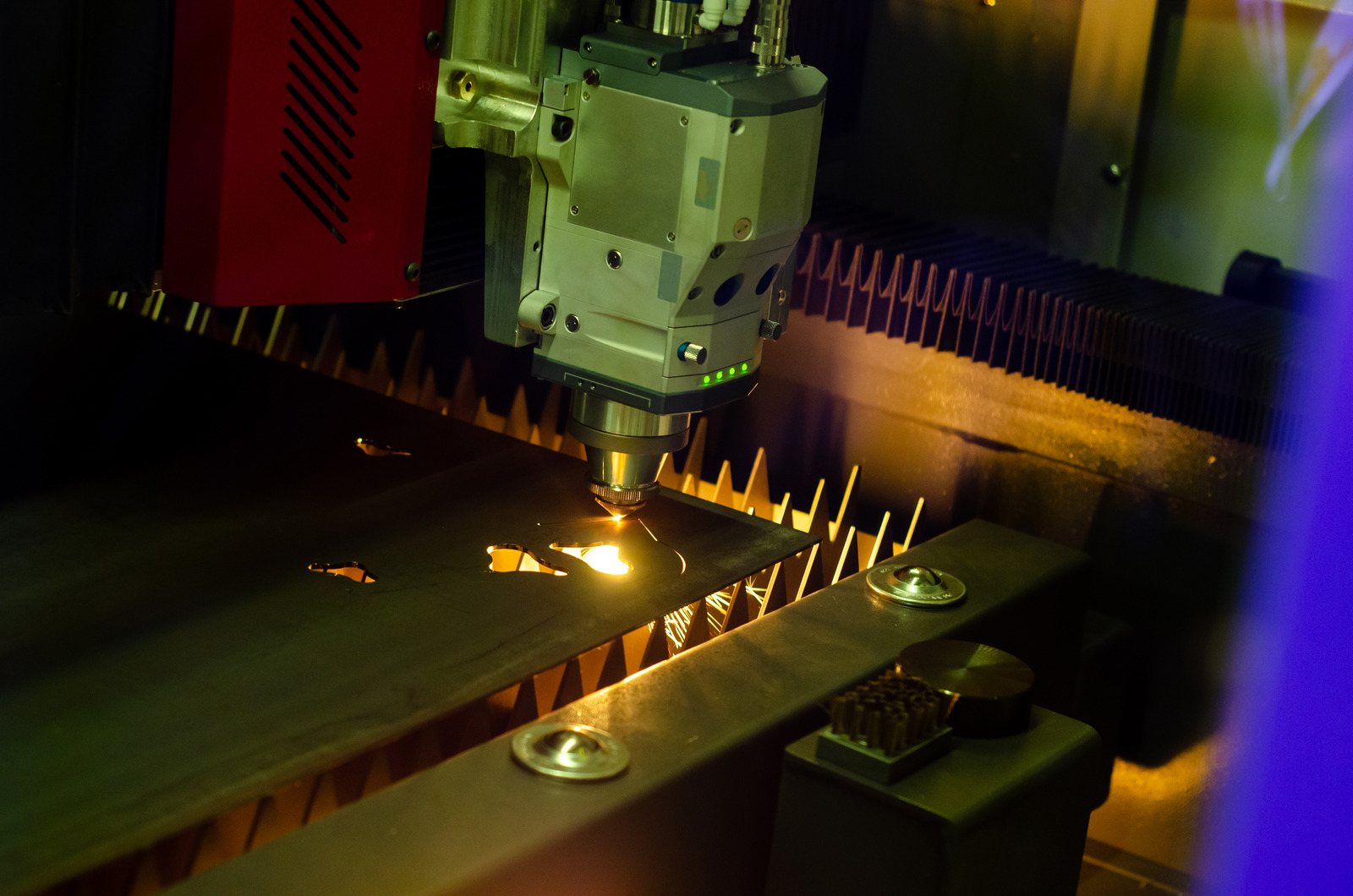
Greater Efficiency
Increased Productivity
When it comes to manufacturing, laser cutting is a key process for creating the parts that go into the final product. The process requires a high level of precision and accuracy, but it doesn’t have to be slow and tedious. To help speed up the process and increase productivity, automated quality control is a must.
Automating the quality control process means the laser cutter doesn’t have to be monitored by an operator or other personnel. Instead, the laser cutter can be left to do its job and will report any issues to the automation system.
Increased Throughput
automation One of the key benefits of automated quality control for laser cutting is increased throughput. Throughput is a measure of the amount of parts being cut compared to the amount of time it takes to complete the job. By using automated quality control processes, businesses can greatly increase the throughput of their laser cutting jobs.
The automated quality control process begins with the insertion of a part into the laser cutter.
Automatically Notified of Defects
One of the primary benefits of automated quality control for laser cutting is the ability to easily and quickly be notified of any defects that might occur. Automated inspection ensures that any problems can be spotted and addressed before the parts are released for further work. This saves time and resources, as workers don’t have to manually inspect each piece and will immediately be alerted to any issues.
The laser cutting process has a high degree of complexity and precision which makes it difficult to manually track quality problems.
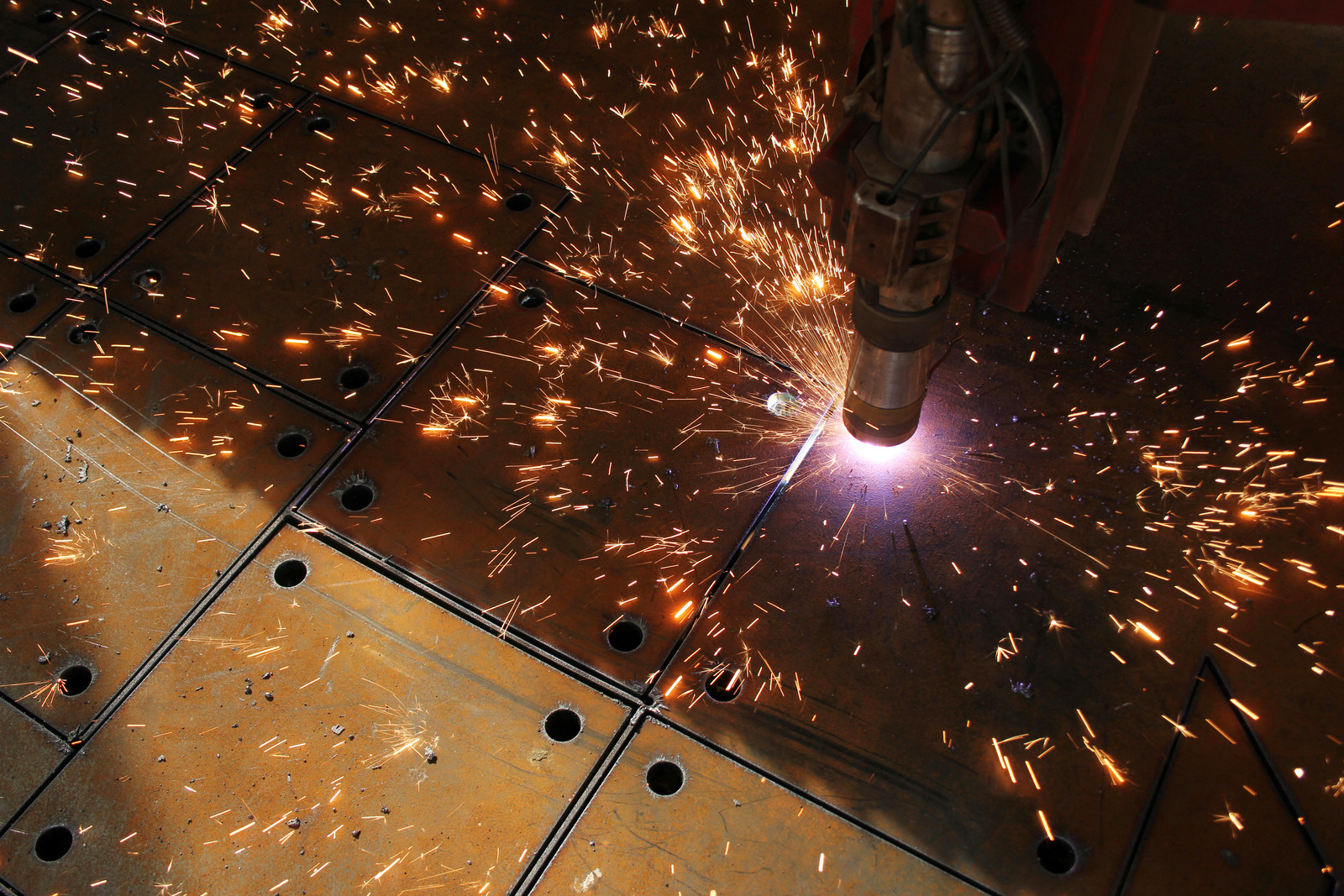
Increased Reliability
Improved Consistency
automation Improved Consistency is one of the biggest benefits of automated quality control for laser cutting. By leveraging automation, quality control processes can be consistently applied in a matter of seconds, providing reliable and consistent cut parts. Automated inspection systems are able to interpret and recognize the contours of parts of interest, detect and report any defects, and provide feedback on the production process to ensure quality and accuracy.
Greater Retention of Quality Standards
quality control Manufacturing and production industries rely heavily on high-quality products and components, and this often requires significant efforts throughout the whole process. In the case of laser cutting, extremely precise measurements and standards must be maintained for an impeccable product. Ensuring this accuracy often requires the manual inspection of each product after it is cut with a laser cutter.
Automated quality control of laser cutting has been a breakthrough in the industry. With this process, improvements in precision and accuracy can now be expected to a much greater degree than before.
Reduced Variance between Layers
quality control One of the major advantages of using automated quality control for laser cutting is the reduction of variance between layers. Automated inspection eliminates the need for manual measurement and visual inspection by utilizing lasers and cameras. This allows for precise measurements and accuracy in the production process, helping guarantee consistent production results.
The laser measuring devices are able to measure the material thickness, surface finish, nooks and crannies, checking that the cut is precise. This helps deliver parts with accuracy and exactness while reducing variability between layers. Using automated quality control technology can also reduce scrappage and wastage, as inspection can be done faster and more cost-effectively than manually.
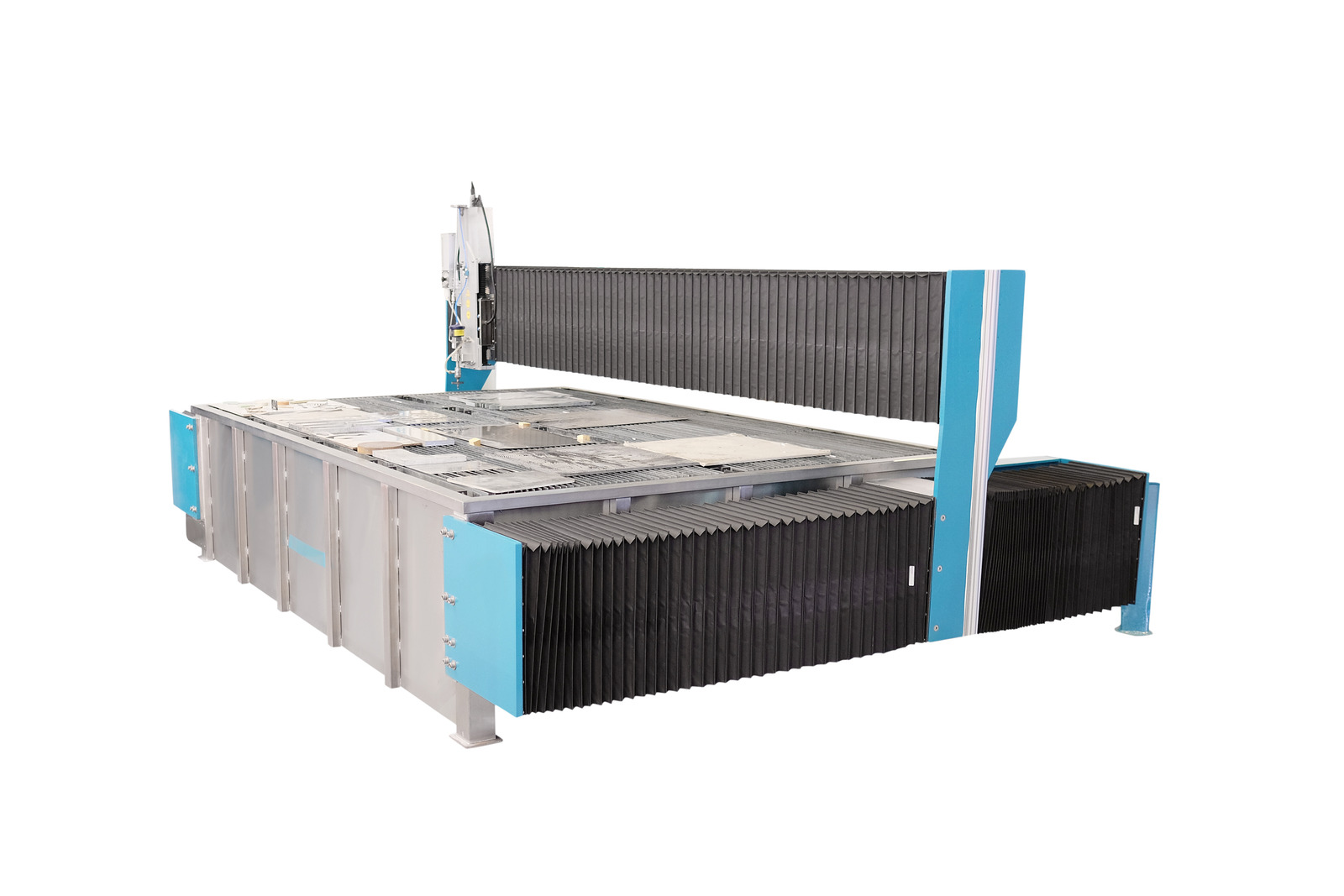
Improved Health and Safety
Reduced Risk of Injury
is One of the most notable benefits of automated quality control for laser cutting is its ability to reduce the risk of injury and safety hazards on the job. Automated inspection and quality control systems provide a much more secure and accurate cutting process. Laser cutters typically require manual handling and positioning, which increases the risk of operator injury.
Less Human Exposure to Laser Beam’s Heat
The use of automated quality control (AQC) for laser cutting offers a number of advantages over manual inspection and quality assurance. One of the most important of these benefits is the reduction in human exposure to the lasers heat. Laser cutters emit a powerful beam of energy which can cause severe burns, damage to clothing and even blindness if safety precautions are not followed.
By utilizing automated quality control systems, manufacturers can reduce the risk of injury to employees. This is done by using sensors to detect the heat emitted from the laser cutter, and alerting workers when the beam reaches a certain level of power.
Improved Workplace Ergonomics
Laser cutting is a process used to shape materials using hot laser beams. It is a technique used in the manufacturing industry to cut shapes and precisions in materials like wood, metal and plastic. As laser cutting has evolved, the introduction of automated quality control systems has enabled manufacturers to create more accurate products with improved safety, health and ergonomic benefits.
One of the major improvements to workplace ergonomics due to automated quality control in laser cutting is the elimination of manual inspection. This means operators can now maintain a good posture while they are operating the laser cutter, as they do not have to twist and turn their bodies to inspect the pre-cut pieces.
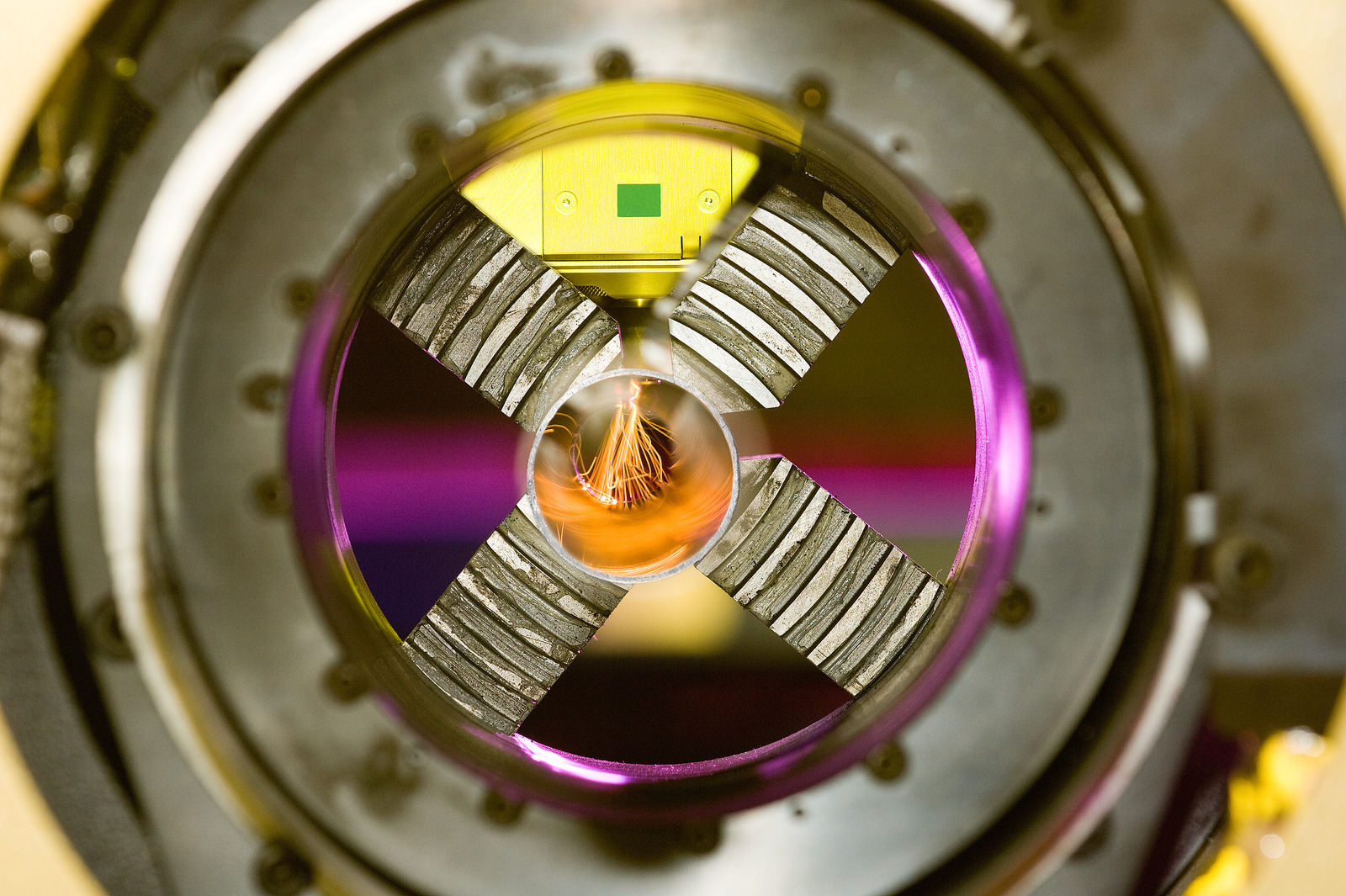
Conclusion
Summary of Benefits
machines The bottom line when it comes to automated quality control for laser cutting is that it’s a no-brainer. Automated quality control for laser cutting saves money, boosts efficiency, and ensures consistent quality for your laser cut products. With automated inspection, you can detect and correct small errors in a fraction of the time it would normally take.
Additionally, the consistent high-quality end product that results will help you stand out from your competitors. Automated quality control for laser cutters also ensures that your laser cutting machines are running optimally, preserving their longevity so you can keep them running for years to come.
Final Thoughts
Our final thoughts on the benefits of automated quality control for laser cutting are that it ensures a higher level of production quality while also saving time and money. Automated inspection systems can identify potential issues quickly and easily, allowing organizations to adjust and adjust their operations accordingly. Automated quality control systems provide organizations with the ability to quickly adjust, repair, and replace defective parts, reducing cost and time associated with manual inspection and repair processes.