Ensuring that products meet the desired specifications is a top priority in manufacturing. Quality assurance is essential in laser cutting processes to guarantee that parts are produced to predetermined standards. This article will explain how to ensure that parts meet the required specifications through quality assurance and laser cutting.
Benefits and Disadvantages of Quality Assurance and Laser Cutting
Benefits
QA One of the biggest benefits of quality assurance and laser cutting is the ability to meet specifications. Quality control is essential in both manufacturing and engineering process, and laser cutting allows for improved accuracy and precision when it comes to machining components. Quality control processes also ensure that all parts meet the specified design requirements, making it an ideal choice for when high levels of accuracy are required.
Quality control is also important when it comes to QA specifications, as it helps reduce the risks of waste and scrap, as well as helping reduce lead times and improve the overall quality of the product.
Disadvantages
We all know that Quality Assurance (QA) and laser cutting are two of the most important elements to producing a quality product. Quality control processes and laser cutting can both help ensure that products meet the manufacturer’s specifications. However, whenever two processes are combined, there can be disadvantages.
When QA and laser cutting are used in tandem, there is an increased risk of components not meeting the QA specifications.
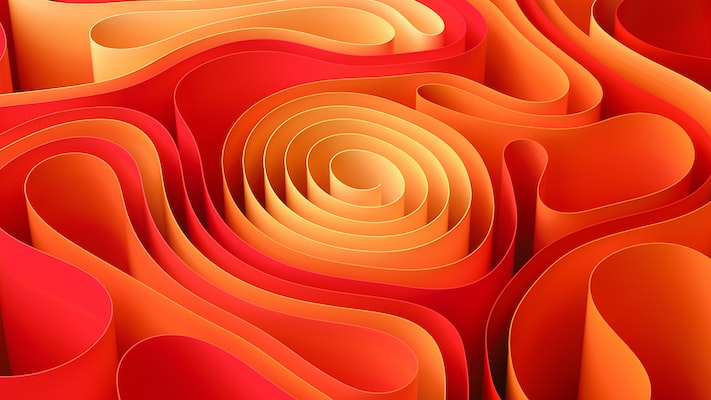
Essential Steps for Quality Assurance and Laser Cutting
Designing the Cut
Designing the Cut is an essential step for Quality Assurance and Laser Cutting. Quality Control and Laser Cutting aim to produce a product to meet specifications and expectations. When it comes to designing the cut, it is important to consider the material being cut and the measurements of the product in order to ensure the desired outcome can be achieved.
Setting Safety Parameters
It is essential to consider safety when conducting quality assurance and laser cutting operations. Setting safety parameters ultimately includes ensuring that products meet required specifications. To meet specifications, quality control is necessary for both the laser cutting machinery and the operators.
Quality Control for Laser Cutting includes checking that the machinery is properly calibrated, making sure the right settings have been inputted into the machine, and confirming the overall operational efficiency of the machinery. For operators, safety parameters include staying up to date with safety protocols, following instructions, and properly wearing appropriate safety gear.
Setting Laser Power
When it comes to quality control, it is essential to meet specifications when utilizing laser cutting. Setting the laser power accurately is a make-or-break factor when it comes to maintaining quality assurance during a laser cutting process. Before the cutting process, the laser parameters need to be set in order to make the right cut.
To do this, the technician must dial in the optimal laser power and speed on the CNC machine. The amount of power should be determined by the material thickness and type. %Materials with higher melting points, for instance, will require more power to be cut.
By taking into careful consideration the material type, thickness and size, the technician should be able to select the appropriate settings.
Maintenance and Quality Inspection
When it comes to Quality Assurance (QA) and Laser Cutting, the importance of maintenance and quality inspection cannot be overstated. Quality control and inspection are essential steps in ensuring that the resulting product meets all the necessary specifications. Quality assurance is a systematic process of monitoring and evaluating the quality of products and services, so it is important to make sure that the laser cutting equipment is in optimal condition and that it is being used properly and in accordance with specific standards.
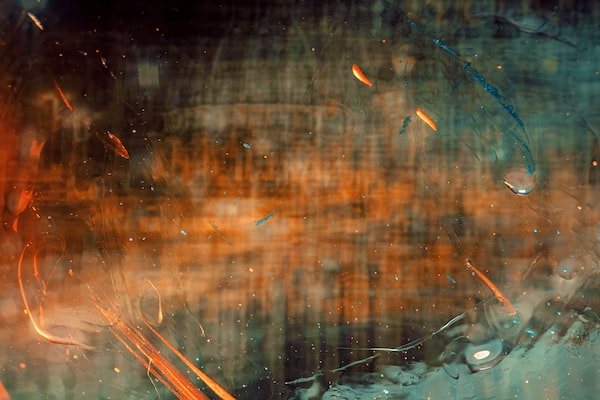
Is the process of insuring that products meet quality specifications?
laser Quality assurance and Laser Cutting: How to Meet Specifications The process of ensuring that products meet quality specifications is known as quality assurance or QA. This means that a product must meet specific requirements for specifications. Quality assurance is important for all manufacturing processes, especially for laser cutting.
Quality control in laser cutting involves ensuring that the material being cut is of good quality, that the laser cutting parameters are correct, and that the cutting result meets the desired specifications.
How do you perform a quality control inspection in manufacturing?
inspection Quality control is paramount when it comes to manufacturing, and laser cutting is no exception. To ensure that the highest possible quality of product is achieved, a thorough quality control inspection must be performed and meet specifications. Quality assurance is an important step in developing a quality product and involves testing the products to determine if they meet the required specifications.
In order to meet the quality control specifications for laser cutting, precise measurements must be taken during each step in the manufacturing process. This includes measuring the size, shape, and angles of parts and checking for any defects that could affect the performance of the product.
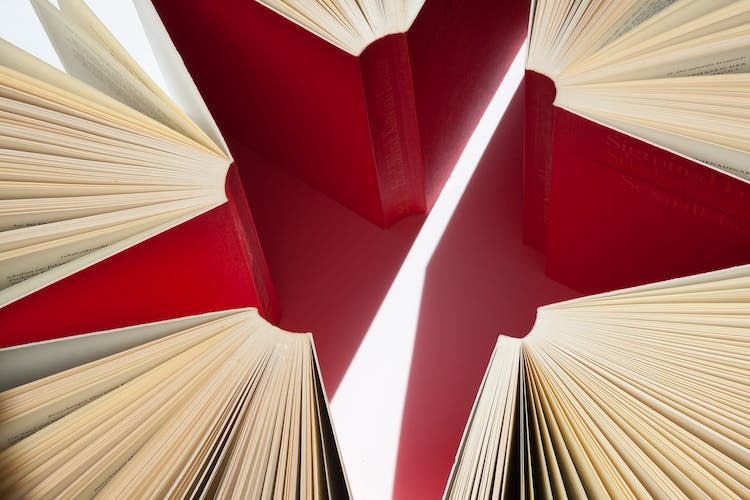
What are the 4 types of quality assurance?
Quality Assurance is essential in the laser cutting process in order to meet specific customer requests or specifications. The four types of quality assurance available for laser cutting include visual examination, process control, detail analysis, and end-use performance testing. Visual examination involves inspecting the product for incisions and surface quality as compared to the drawing used.
- Create a quality assurance checklist: Develop a checklist of the specifications and requirements that must be met to ensure the highest quality parts are produced.
- Check delivered parts: Inspect designed parts right away to ensure that they meet all of the desired specifications and quality requirements.
- Review customer drawings: Carefully review all customer drawings to ensure that the laser cutting process is correctly optimized to meet the customer’s requirements.
- Monitor cutting parameters: Monitor the cutting parameters while the laser is in operation to ensure that they remain consistent with the customer’s specified requirements.
- Verify cut parts: Analyze the cut parts, compare them to the customer’s specified requirements and make any necessary adjustments. Ensure the accuracy of the customer’s drawings and that the parts meet all of the desired specifications.
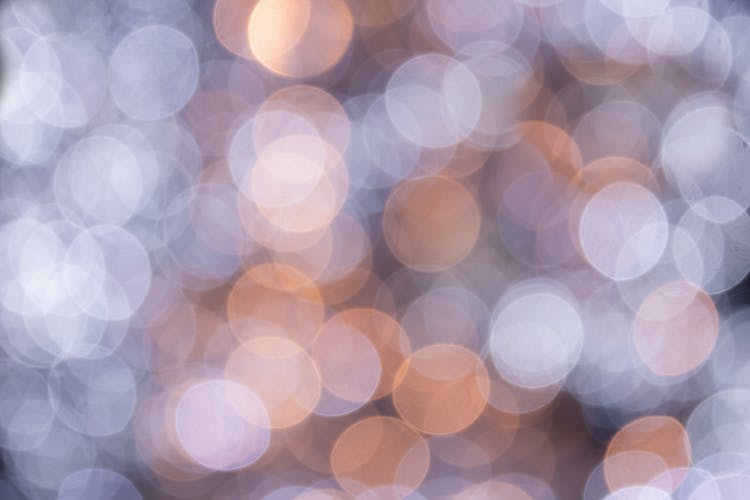
Conclusion
Summary of Quality Assurance and Laser Cutting
Quality assurance and Laser Cutting are two important aspects of any manufacturing process. Quality Assurance (QA) involves setting specifications to ensure that products meet customer standards, while Laser Cutting ensures that parts are machined with precision and accuracy. QA and Laser Cutting are both important to meet customer requirements and specifications, and should be done with quality control measures in place.
Quality Control (QC) is the systematic inspection of each step of a product’s life cycle to ensure that it meets QA standards and specifications for laser cutting.
Final Recommendations
In conclusion, there are several steps that can be taken to ensure that your laser cutting operation meets your quality assurance (QA) specifications. Following quality control best practices, including training, preventive maintenance, and monitoring, will help ensure that you are meeting your standards and will take your operation to the next level. Additionally, implementing a routine inspection system helps to ensure that any issues with your laser cutting process are identified and solved quickly.
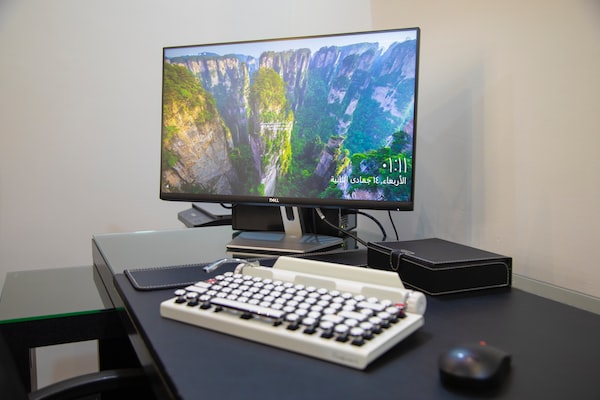