Optimizing laser cut elevation designs can be a challenge. It requires careful planning, consideration and skill to ensure that the designs are created with efficiency in mind. In this article, we will explore how to achieve maximum efficiency when optimizing laser cut elevation design products. We’ll explore how to properly plan the design process and use the right tools and materials to achieve the desired results. Additionally, we will provide insights on how to identify any potential problems that may arise and offer helpful solutions. By the end of the article, you should have a better understanding of how to maximize efficiency while creating laser cut elevation designs.
Factors to Consider When Optimizing Laser Cut Elevation Designs
Materials
When it comes to optimizing laser cut elevation designs, materials are an important factor to consider. The type of material used plays a major role in how the laser cutter will perform and the results you can expect. Each type of material and thickness will require different levels of laser power and cutting speed, as well as a different cutting head lift.
Using the wrong settings can result in a poor cut quality or a damaged material. Different materials also react differently to the laser heat and pressure used to cut through them. In order to get the best results, it is important to select the right material for the job.
For instance, laser cutters typically require more power when cutting through metals than when cutting through wood.
Design Considerations
When it comes to optimizing laser cut elevation designs, the design considerations are paramount. Most laser cutting machines have several settings to consider in order to achieve the desired cut quality and maximum output with minimal resource consumption. The most common design consideration when it comes to laser cutting is the power capacity of the laser cutter.
If a machine has a higher power capacity, it will be able to cut through thicker materials in order to minimize cutting head lift and decrease the overall cutting time required.
Time & Cost
When it comes to optimizing laser cut elevation designs, two of the main factors to consider are time and cost. Time and cost optimization can be achieved at the same time or separately, depending on your needs. It all comes down to understanding how laser cutting works and using the analysis to make informed decisions.
Time optimization is often the primary factor when it comes to laser cutting. This is especially true when dealing with large-scale production or rapid prototyping.
Strategies for Optimizing Laser Cut Elevation Designs
Appropriately Sizing the Elevation
When it comes to optimizing laser cut elevation designs, one of the key elements for achieving maximum efficiency is appropriately sizing the elevation. By taking the time to decide on the ideal size, you can not only reduce cutting head lift and thus achieve maximum output, but you can also optimize the laser cutter’s linear investment model by using a premium board cutting pattern.
Identifying Appropriate Materials
When it comes to optimizing laser cut elevation designs for maximum efficiency, identifying the best and most appropriate materials to use is one of the most important considerations. The right choice of materials can make all the difference in achieving the desired output with the cutting head, reducing its lifting time, improving its performance, and allowing for a consistently high level of output. To help with the decision-making process, there are a variety of tools at our disposal that can simplify the process.
Utilizing Finishing Techniques
Optimizing Laser Cut Elevation Designs for Maximum Efficiency, Strategies for Optimizing Laser Cut Elevation Designs When it comes to finishing techniques, lasers are the preferred tool. Laser cutting can provide maximum output with an optimized laser path and reduced cutting head lift. The way laser cutting is designed and completed has an impact on the overall efficiency and cost of the project.
Utilizing finishing techniques can help ensure a successful laser cut elevation design. One of the most important parts of a successful laser cutting project is the linear investment model. This is a process used to ensure cutting occurs at the most efficient rate, minimizing the amount of time required to complete the project.
Incorporating Support Structures
When using a laser cutter to create elevation designs, incorporating support structures into the cut is an essential part of optimizing for maximum efficiency. Support structures provide an essential layer of support between the main components of an elevation, allowing for more intricate and delicate designs that are quicker, easier and more cost-efficient to create. By using support structures, designers can reduce the need for the laser cutting head to lift, or be raised and lowered, throughout the cutting process.
This reduces the amount of time spent cutting, and significantly boosts maximum output.
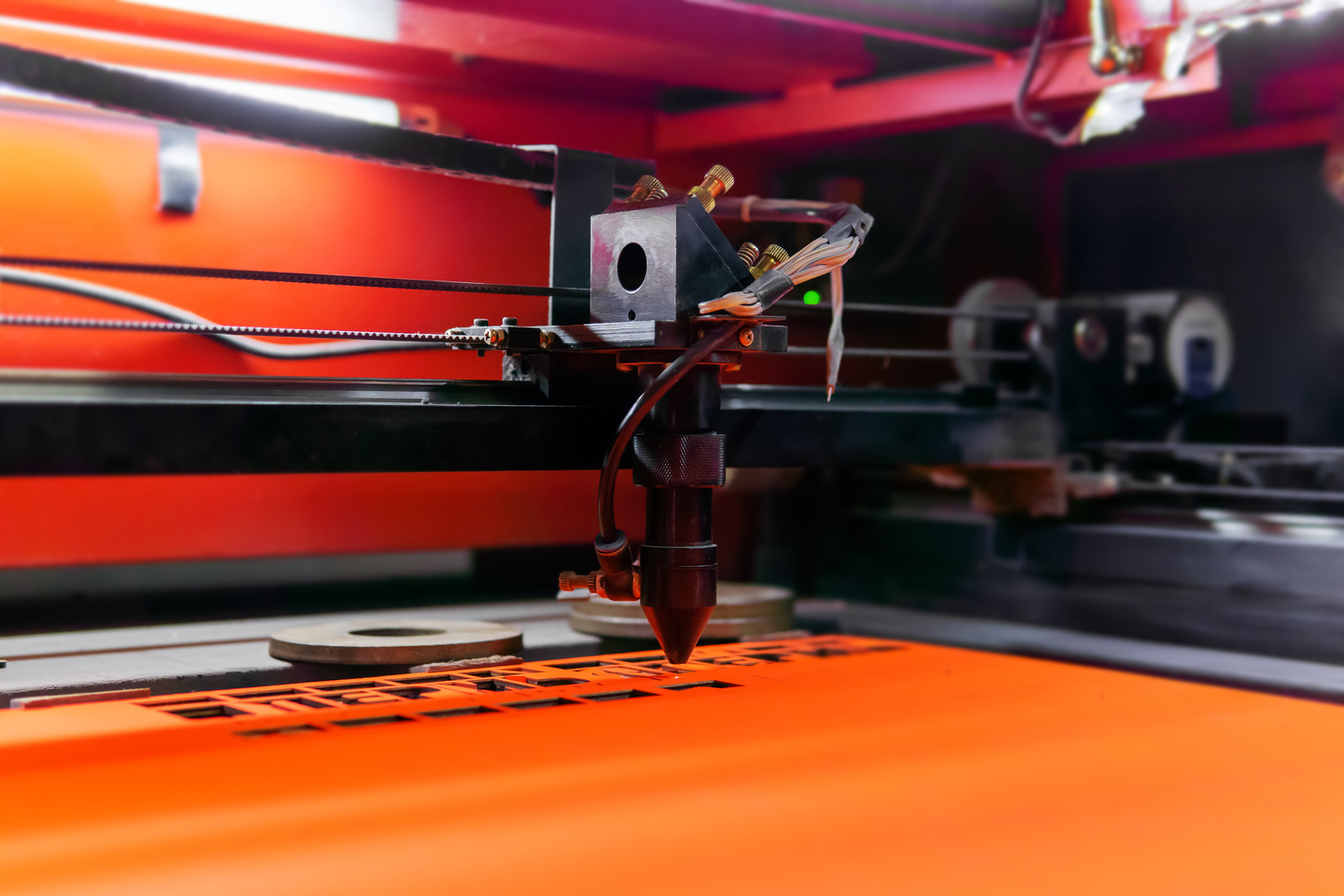
Challenges & Possible Solutions
Limited Production Time
One of the biggest challenges in optimizing laser cut elevation designs for maximum efficiency is limited production time. Laser cutting technology reduces production time by allowing cuts to be completed in a fraction of the time required by traditional methods. As a result, laser cutters can produce large, intricate projects quickly and accurately.
However, in order to maximize output, the laser cutter must be used properly. One way to optimize the laser cutter’s production time is to reduce the amount of time that the cutting head lifts from the board or material.
Increased Material Use
One challenge often faced when optimizing laser cut elevation designs is increased material use. This occurs when a cutting head must lift while switching from one cutting board to the next. Even brief breaks in cutting create the need for additional material, which increases overall costs.
Fortunately, there are a few ways to reduce the amount of material used in laser cutting operations. First and foremost, a laser cut optimization strategy should include optimized laser head paths. This ensures that the laser head will not have to lift from the current board until the project is finished.
Balancing Durability & Cost
When designing elevation designs for a laser cut, it can be a balancing act between durability and cost. Durability often carries a higher price, but that doesn’t mean you can’t maximize efficiency and optimize the laser cutting process to reduce costs. To do this, you need to consider how to reduce the lifting of the laser cutting head and achieve maximum laser cutting output.
One way to optimize laser cutting is to use a linear investment model.
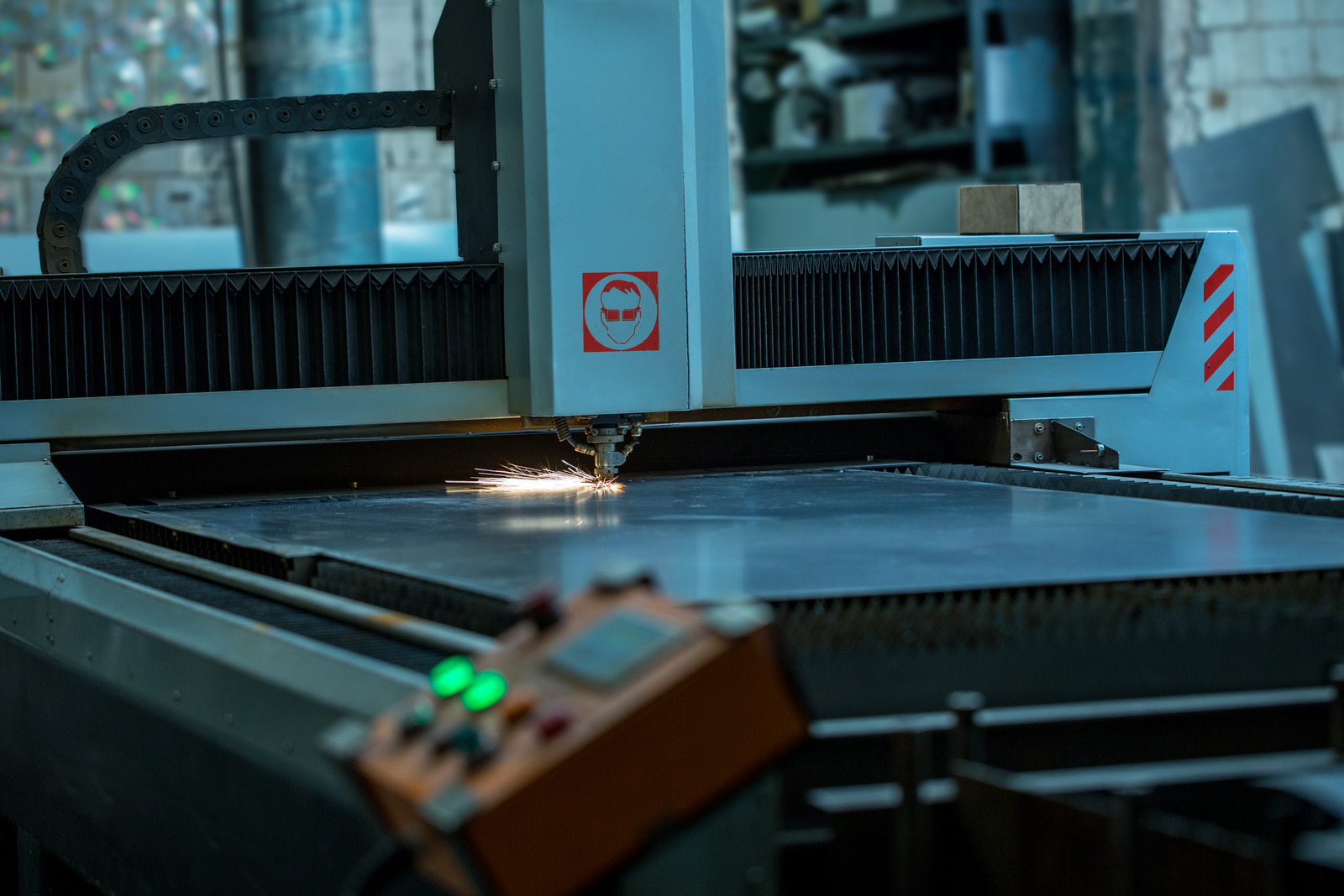
Does laser cutting have higher sheet utilization?
When it comes to optimizing elevation designs for maximum efficiency with a laser cutter, the question of whether laser cutting has higher sheet utilization is an important one. Certainly, laser cutting can bring a wide range of benefits including reduced cutting head lift and maximum output for laser cutting systems. But, does laser cutting have higher sheet utilization?
The answer is yes, particularly when compared to other cutting processes such as milling, riveting and punching machines. This is because laser cutting machines employ optimized laser linear investment models to quickly and accurately cut components from sheet metal.
What are tolerances for laser cutting?
When it comes to laser cutting, accuracy and efficiency are key. And the main factor that affects the quality of laser cutting jobs is tolerance. Tolerance refers to the amount of variations between parts that need to be cut.
The closer the tolerance, the better the quality of the cut will be. Essentially, in order to maximize the output of a laser cutting machine and reduce the cutting head lift, certain tolerances must be adhered to in order for the laser to generate the best results.
Conclusion
Summary of Key Points
In this blog we discussed optimizing laser cut elevation designs for maximum efficiency and discussed a variety of elements to consider in order to ensure that your laser cutting projects are successful. With a few small tweaks in your designs, you can drastically improve the efficiency and output of your laser cutter. Firstly, we examined the way that the cutting head can be lowered or “drooped” to reduce cutting head lift.
Final Thoughts
In our final thoughts about optimizing laser cut elevation designs for maximum efficiency, it’s crucial to understand the different tools and programs that can be used to increase your output and reduce your cutting head lift. Laser cutters are incredible tools and can cut through a variety of materials if used correctly and with the right settings. However, the key to gaining high-quality cutouts with maximum output and minimal waste is optimizing your design and approach.
One way to do this is to use a linear investment model.