The use of precision laser cutting for metal has revolutionized the way in which metal is cut and shaped. This technology allows for the precise cutting of even the most intricate designs, while also minimizing waste. By eliminating the need for grinding and other more laborious and time-consuming processes, laser cutting offers the production of parts that are accurate, cost-effective and ecologically friendly. This article will explore how precision laser cutting can help you optimize your production to reduce waste and maximize efficiency.
Benefits of Minimizing Waste with Precision Laser Cutting for Metal
Cost savings
Using a precision laser cutter to cut metal offers substantial cost savings due to the reduction in material waste. Because laser cutting is so precise, it is able to accurately cut out even the most intricate detailing without any instance of material waste. This advantage is especially important when you consider the cost of the material that is being cut.
Even the slightest of errors or deviations caused by other cutting tools can result in excess material waste. Laser cutting avoids this by allowing you to precisely control the vector and width of every cut.
Efficiency
At its core, efficiency is about making the most of available resources. Precision laser cutting for metal is an incredibly efficient method of cutting and shaping metal–helping to reduce waste significantly. The computer-controlled laser cutters use CNC (Computer Numerical Control) programming, which allows the machine to precisely follow a given path with remarkable accuracy.
The precision of laser cutting leads to fewer opportunity for human error. With traditional methods, human inaccuracies will often lead to uneven cuts and wasted materials. By contrast, laser cutters cut with pinpoint accuracy and amazing repeatability.
Quality of the cut
Using precision laser cutting for metal is a great way to reduce waste during the manufacturing process. The laser cutters used in this process are extremely precise, allowing manufacturers to achieve extremely fine tolerances and create high-quality products with tight precision. The laser cutter produces a smooth, non-jagged cut, resulting in minimal waste and higher quality end product.
Additionally, the laser cutting process reduces the amount of labor involved in creating components, allowing the manufacturer to create parts with fewer workers and materials.
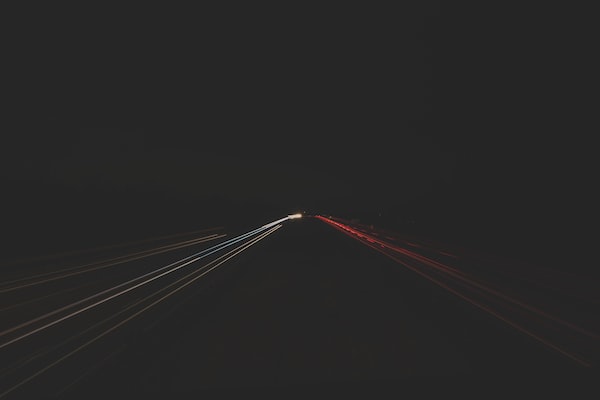
Different Types of Precision Laser Cutting for Metal
Oxygen-assisted laser cutting
Oxygen-assisted laser cutting is a type of precision laser cutting process that allows for a high-quality, clean-cut with minimal waste. It uses a focused laser beam to cut or melt metal surface and an oxygen jet to blow away melted material and debris that results from cutting process. The oxygen jet helps keep the cut surface as clean and smooth as possible and also offers protection against heat generated by the cutting process of the laser.
CO2 laser cutting
When it comes to reducing waste and maximizing precision and accuracy, CO2 laser cutting is the way to go. CO2 lasers are very precise in their cutting, meaning they can create intricate designs with higher levels of accuracy than traditional cutting methods. This results in less wasted material due to precise cuts that fit together perfectly.
The CO2 laser cutter also heats up the metal to be cut, allowing for thinner, more accurate cuts. While it is more expensive than traditional cutting, its accuracy and ability to reduce waste can save money in the long run.
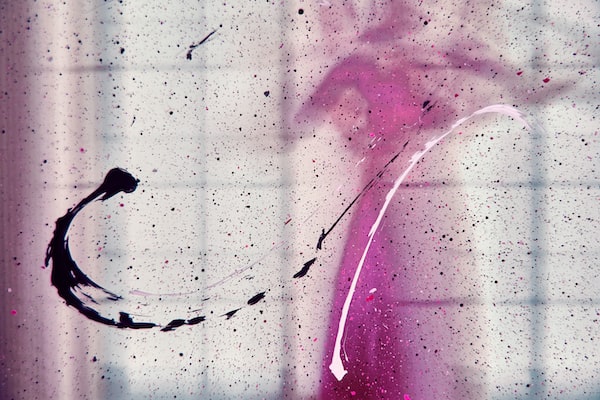
How Precision Laser Cutting for Metal impacts Minimizing Waste
Less scrap material
Precision laser cutting for metal is an effective way of minimizing waste during production and fabricating processes. Laser cutters are used to cut metal with a high degree of accuracy and precision, resulting in reduced waste compared to other cutting methods. The laser cutter operates in a similar way to a computer printer, but instead of printing ink the laser cutter prints a beam of laser light that is focused onto the metal and which is powerful enough to melt and vaporize the metal, leaving a smooth, consistent cut.
This means that far less scrap material is left due to wasted cutting passes as is the case with other cutting methods like plasma or oxy-fuel.
Smoother production process
When it comes to creating precise pieces out of metal, laser cutting can have a major impact on reducing waste. Laser cutting is an incredibly precise process that involves focusing a beam of high-powered laser light onto a target material, making highly precise cuts without having to physically touch the material. This precise cutting process allows manufacturers to create pieces out of thin sheets of metal quickly and accurately, with minimal waste.
Laser cutters can also be used to etch intricate designs onto metal, allowing for even more precise cutting. With laser cutting, manufacturers can create pieces with a much higher level of precision than was possible in the past.
Improved accuracy
When it comes to minimizing waste, precision laser cutting for metal has the potential to make a huge impact. Laser cutting is a process in which a laser beam is used to cut a material into a desired shape or pattern. A key advantage of laser cutting technology is the ability to cut material with improved accuracy and accuracy down to the micron level.
With this improved accuracy, laser cutting can help reduce waste and save materials for projects. Using a laser cutter, accurate cuts can be made in thinner and harder material than traditional methods.
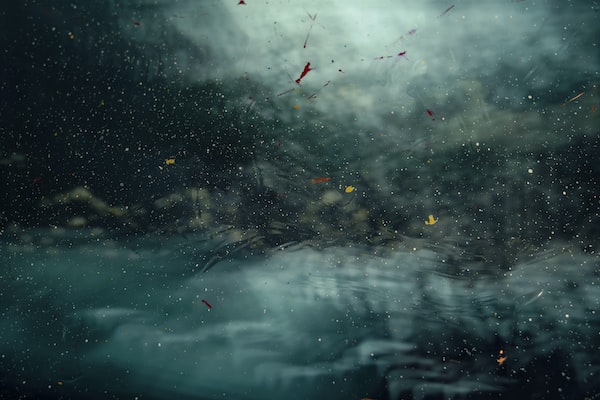
Precautions for Minimizing Waste with Precision Laser Cutting for Metal
Protective equipment for workers
When it comes to precision laser cutting for metal, it is essential to use protective equipment in order to minimize waste. The laser cutting process involves firing high-powered beams of light that can cause harmful exposure to workers and bystanders, as well as kicking up particles and debris, which can be harmful to breathe in. To reduce risk of injury or waste, workers should always wear protective eyewear, face masks, gloves, and protective clothing when operating machinery.
Additionally, a workplace should also be well ventilated, as high concentration levels of residual chemicals from the cutting process, such as powdered metal and other particulates, can be easily inhaled.
Adherence to safety standards
Adherence to safety standards is essential when it comes to minimizing waste with precision laser cutting for metal. Properly trained operators, who understand the hazards associated with high-powered laser cutters, should be handling the machines. The laser cutter must be properly monitored to ensure that the settings are programmed correctly to get the optimal cut for the material being cut.
Protective gear, such as safety glasses, should be worn when operating the laser cutter. When it comes to the setup of the laser cutter, the material being cut should be carefully positioned on the cutting bed. Optimal settings for each material should be established to ensure that the material is cut efficiently.
Consuming resources responsibly
Consuming resources responsibly is an important part of any production process. When it comes to precision laser cutting for metal, one key way to reduce waste is to properly utilize precision laser cutting machines. Laser cutting machines can help to ensure the precise and accurate cutting of materials.
With precise measurements, an efficient cutting process and minimal wastage of resources, precision laser cutting can be a great way to reduce waste and maximize efficiency.
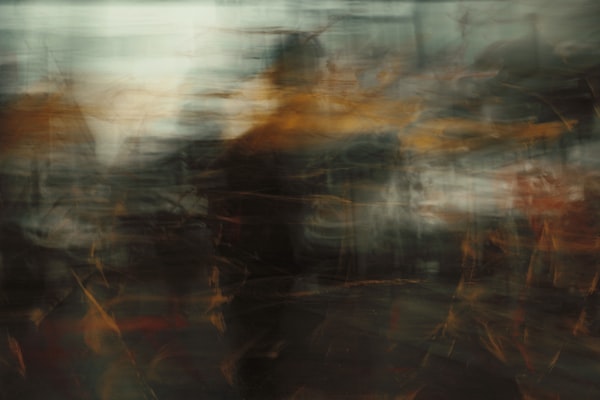
Is laser cutting metal accurate?
Laser cutting is increasingly becoming the go-to technique for processing metal, as it offers superior accuracy and reduced waste compared to traditional cutting methods. Precision laser cutters can cut metals with accuracy down to the thousandths of an inch, reducing waste and minimizing the need for additional processing. That’s why laser cutting is quickly becoming the preferred method for cutting metal, as it provides the highest level of accuracy and precision cutting.
Using a combination of high-pressure lasers, these laser cutters can process metal in a matter of seconds, cutting it with extreme precision.
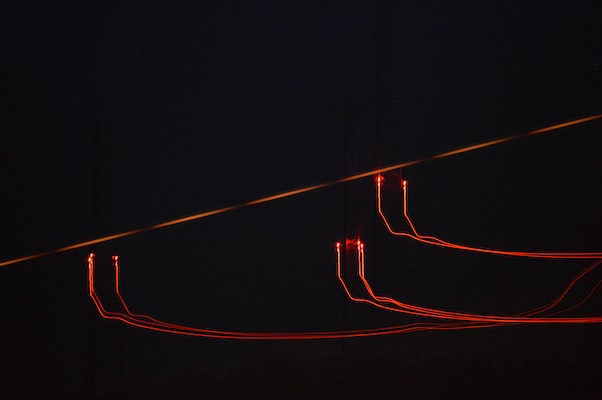
How many watt laser do you need to cut metal?
Whether it’s a small, localized project or a large production batch, reducing waste with precision laser cutting for metal is a priority. But knowing the power of the laser necessary to effectively cut metal can be a challenge. The power of the laser needed to cut metal depends largely on the material being cut.
For materials that are over 2mm thick, such as plate steel, a laser cutter with a wattage of at least 1,000-4,000 is generally necessary to get the job done. On the other hand, for thinner materials, a laser cutter in the range of 500-1,000 watts will typically do the trick.
Conclusion
Summary of the benefits of precision laser cutting
When it comes to minimizing waste in industrial operations, precision laser cutting for metal can be an incredibly beneficial solution. Laser cutting technology is incredibly precise, allowing a wide range of intricate form and shapes to be cut accurately in minimal time. It also offers a wide range of customization options, ensuring that customers get exactly what they need from their products.
Plus, laser cutting reduces the amount of waste left over from the cutting process, reducing overall material costs for industrial operations.
Outline of the precautions to be taken
The conclusion of the topic of minimizing waste with precision laser cutting for metal is that such technology is a great resource that can be utilized. When used in a safe manner, it can greatly reduce waste by reducing the amount of material needed to complete a job.
- Ensure that the laser cutting process uses quality materials, such as high-grade stainless steel and aluminum alloys, to reduce the risk of uneven edges and distortion.
- Always use a bevel edge to reduce the risk of sharp edges and potential injuries.
- Follow a strict maintenance schedule and use the appropriate safety equipment while operating the laser cutting machine.
- Utilize fume extraction systems to reduce any potential health risks and hazardous materials created during the laser cutting process.
- Measure accurately before cutting to reduce the risk of over wasting materials and to maximize the productivity of the laser cutting process.