Laser cutting has long been a revolutionary technology in the manufacturing sector. It offers many advantages over traditional cutting processes, including speed, accuracy, greater flexibility, and lower costs. Increasingly, rubber sheet manufacturers are starting to incorporate laser cutting into their operations as a way to maximize efficiency and lower costs. This article will provide an overview of how laser cutting can be used to improve the rubber sheet manufacturing process.
Advantages of Laser Cutting
Accuracy
Incorporating laser cutting into your rubber sheet manufacturing process brings a number of advantages, one of them being accuracy. Laser cutting enables precise and intricate designs, with high levels of accuracy. The laser beams emitted by the machine has the ability to create precise and detailed patterns, with a precision of up to 0.08mm.
This level of accuracy helps in making production faster and increases the efficiency of the cutting process in the long run. Moreover, the laser cut also eliminates the need for extra equipment, such as knives and blades, which can be time-consuming and tedious to use.
Speed
One of the biggest advantages of incorporating laser cutting into your rubber sheet manufacturing process is speed. Using laser cutting, the rubber is cut quickly and efficiently, making the production process much faster and more efficient than other cutting methods. Laser cutters are capable of working at speeds of up to one hundred thousand cuts per second, enabling operators to produce large quantities of rubber in a shorter period of time.
The speed also means that the cutting process is faster and more accurate, resulting in a high-quality product that is cut with precision. In addition, laser cutting helps reduce heat build-up and allows for faster stock removal, making it ideal for high-volume rubber sheet production.
Cost efficiency
Using laser cutting in the rubber sheet manufacturing process can provide a number of benefits. One of the biggest advantages is cost efficiency. Laser cutting offers the highest level of accuracy and offers speed of the highest standards.
This means that less material is wasted in the cutting process, which in turn leads to a lower cost of production. In addition, the speed of the cutting process means that it can be completed in a lot less time compared to traditional methods. This makes it easier and quicker to make a production run and reduces the costs associated with labour and energy.
Furthermore, laser cutting is highly accurate, which means that designers and engineers are able to get the best possible precision when designing their parts.
Laser Cutting vs Alternative Cutting Methods
Water Jet Cutting
Water jet cutting is a great alternative for those wanting to incorporate laser cutting into their rubber sheet manufacturing process. This cutting method utilizes pressurized water to cut through tough materials, like rubber. The high-pressure water stream slices through the material, allowing for precision cutting and intricate shapes.
This makes it ideal for producing rubber sheets with intricate designs or for cutting large pieces of rubber for manufacturing purposes.
Thermal Cutting
Thermal cutting is a method used to cut rubber sheets. It is a type of cutting process that uses heat to cut through the rubber, making it possible to achieve airtight and precise cuts. Laser cutting is one of the most popular thermal cutting methods used in rubber sheet manufacturing.
It has been used for decades as an effective method of cutting rubber sheets due to its accuracy and efficiency. By using laser cutting to shape rubber sheets, manufacturers are able to create intricate designs with greater precision than alternative methods. Laser cutting produces minimal waste, reducing the amount of materials needed during production.
It is also a much faster process than manual cutting, resulting in faster production times.
Traditional Cutting
Traditional cutting of rubber sheet is generally used in the manufacturing process as a time-tested method to cut the rubber into various shapes, sizes, and configurations. This method typically requires multiple stages with a die set to accurately cut the rubber sheet. A die set consists of multiple parts that shape the rubber sheet into the desired shape.
A series of cutting boards are used to guide the die set as it shapes the rubber sheet, creating a precision cutting process.
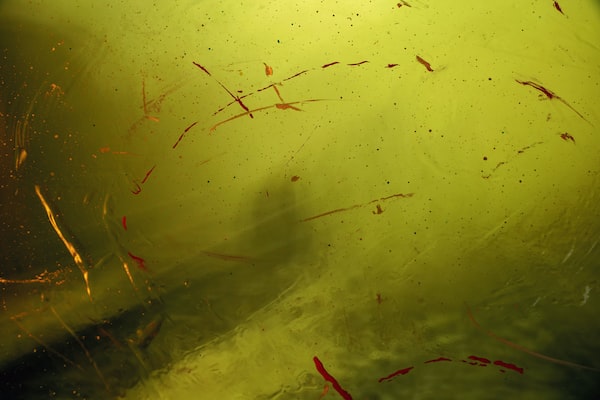
Preparing for Laser Cutting in Rubber Sheet Manufacturing
Choosing the right machine
materials When it comes to incorporating laser cutting into rubber sheet manufacturing, it is important to choose the right machine and understand the method. Laser cutting is a precise and efficient way to cut rubber sheet and other materials, making it an ideal choice for production. For this reason, it is essential to consider the quality of the machine, the type of cutting process, the associated laser cutting parameters and the material to be cut.
Selecting materials
When it comes to incorporating laser cutting into your rubber sheet manufacturing process, the selection of material is one of the most important steps. The method of cut rubber sheets can vary, but the most common choice used in industry today is laser cutting. When laser cutting is chosen as the preferred method, the rubber sheet must be selected to be suitable for the cutting process.
The material must be able to withstand the intense heat created by a laser beam and also be thin enough to fit within the laser cutting machine’s beam path.
Layout planning
When it comes to incorporating laser cutting into rubber sheet manufacturing, layout planning is a critical step in the process. Layout planning is the process of determining the best way to cut the rubber sheet so that the desired dimensions are achieved. The layout should also include the location of any holes or slots required for the production process.
It is important to consider the material thickness and physical constraints in order to ensure the power output and speed of the laser to achieve the desired cutting result. Layouts should also consider the various cutting qualities that the laser is capable of producing. Generally, the laser will either cut or etch through the rubber depending on the power setting and speed of the laser.
Creating optimal cutting settings
When incorporating laser cutting into your rubber sheet manufacturing process, it is important to consider how to create optimal cutting settings. Laser cutting is a precise and efficient way to process a wide range of materials, including rubber sheets. The technology is used for various rubber sheet manufacturing applications and requires careful and methodical planning to ensure maximum efficiency and accuracy during production.
When it comes to cutting rubber, there are several factors that come into play.
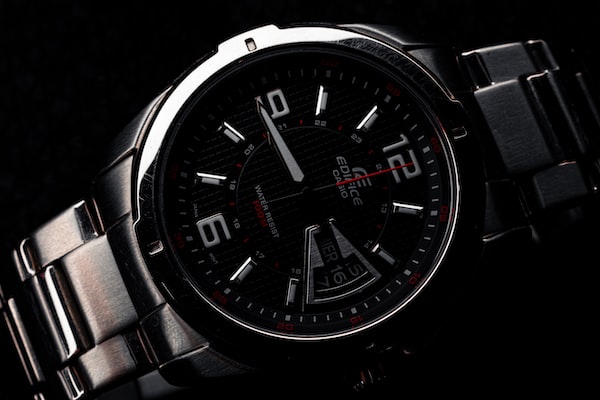
How to Implement Laser Cutting in Rubber Sheet Manufacturing
Integration with existing technology
Integrating laser cutting into your rubber sheet manufacturing process doesn’t have to be complicated. The first step to properly implementing this method is to make sure you have the right technology. Laser cutting is a computer numerically controlled (CNC) process that uses high-power lasers to cut rubber sheets.
For this purpose, you will need a laser with the proper power output and a CNC machine that can be programmed to work according to your needs. Once you’ve got the right technology, you’ll need to determine the cutting process in order to get the most out of your laser cutting procedure. Properly planning the cutting process will ensure that your rubber sheets are cut with accuracy and precision.
Creating effective process controls
Creating effective process controls for incorporating laser cutting into your rubber sheet manufacturing process is essential for the success of the product. A key component in developing these processes starts with identifying the method of cutting the rubber sheet, whether it be a die cutting process or a laser cutting process. Once the cutting process has been determined, the next step is to ensure that it can be effectively implemented with the right type and size of laser cutting machine.
Quality assurance and issue resolution
When incorporating laser cutting into your rubber sheet manufacturing process, it is important to consider how to ensure quality assurance and how to address any issues that may arise. Quality assurance is a key part of any production process and needs to be taken seriously to ensure that the end product meets the standards set by the company. Laser cutting is no different and requires the same rigor and attention as any other step in rubber sheet manufacturing.
For quality assurance, it is important to ensure that the laser is well-maintained and that all of the settings are accurate and appropriate for the particular job.
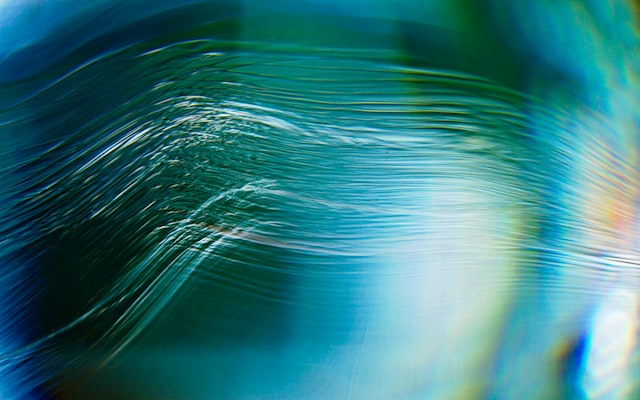
Can you laser engrave rubber?
rubber Yes, you can laser engrave rubber as part of your rubber sheet manufacturing process. This process begins with using a laser beam to cut the rubber sheet into desired shapes and sizes. This laser cutting is a more precise and accurate way to cut rubber than other methods, as it creates a more precise end product.
The laser cutting process typically works by directing focused light, typically from an ultraviolet or infrared laser beam, onto the rubber sheet.
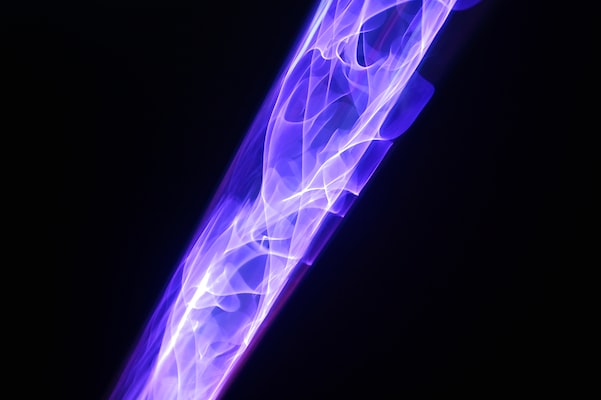
Conclusion
Final thoughts on the benefits of laser cutting in rubber sheet manufacturing
In conclusion, incorporating laser cutting into the rubber sheet manufacturing process can bring about a variety of advantages. This advanced tactic of cutting rubber allows for the production of precise and complex rubber pieces, which can save time and energy. Laser cut rubber pieces are far more accurate than other methods of cutting rubber and can produce pieces with perfect edges and clean lines.
Furthermore, laser cutting helps to reduce waste in the cutting process, as only minimal amounts of material is removed in the cutting process. Finally, this approach of laser cutting rubber for manufacturers also offers increased safety for workers. Defective or hard-to-reach cuts can be made more easily, reducing the likelihood of injury.
Further research and resources
Incorporating laser cutting into your rubber sheet manufacturing process can be a great way to expand your production capabilities and make your manufacturing process more efficient and cost-effective. As with any complex manufacturing process, it’s important to do additional research to ensure you get the most from your laser cutting machines. At the conclusion of this series, we’ve provided a few tips and resources for further research.
Firstly, it is essential to determine the most efficient rubber sheet production methods for your organization.
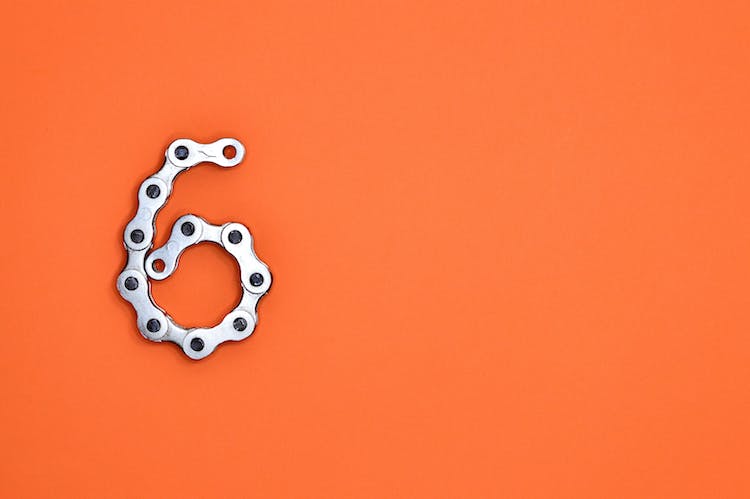