Laser cutting zinc can be an intricate process and it’s important to do it right in order to get the best results. There are various factors to consider before you begin laser cutting zinc, including the laser power and speed, type of cutting gas and the appropriate settings. This guide will provide you with some tips and tricks to ensure you get the best results when laser cutting zinc.
Types of Laser Cutting Systems for Zinc
Understanding the Different Types of Laser Cutting Systems
cutter When it comes to laser cutting zinc, it can be tricky to know what kind of system you need to get the best results. There are a variety of laser cutting systems available, so it’s important to understand the different types and what they are best suited for so that you can find the perfect laser cutter to get the results you want.
Advantages of Using a Fiber Laser
Using a fiber laser is a great way to get the best possible results when laser cutting zinc. Fiber lasers offer a number of advantages over traditional CO2 and Nd:YAG lasers, making them an ideal choice for both industrial and consumer applications that require accuracy and precision in their laser cutting results. Fiber lasers are much more effective than their CO2 and Nd:YAG counterparts when it comes to cutting thick materials, including zinc.
Advantages of using a CO2 Laser
engraving Using a CO2 laser is the perfect way to achieve great results when laser cutting zinc. Here’s why it’s an excellent option for the job: First of all, CO2 lasers have a high power output, which is ideal for cutting thicker metal sheets. This makes it easy to work with zinc, which is known for being a particularly difficult material to cut.
Furthermore, you don’t have to worry about getting any messy cuts – the laser can create smooth and precise cuts, no matter how intricate the shapes. Second, the speed gains you get with a CO2 laser make it ideal for large projects with multiple parts.
Cost Considerations
When it comes to cost considerations for laser cutting zinc, one of the main things to keep in mind is the initial price of the machine itself. You want to make sure that you find a laser cutter that is powerful enough for the thick material of zinc yet still fits into your budget. Look for models that have multiple head configurations so that you can ensure that the laser is able to cut through the zinc with ease.
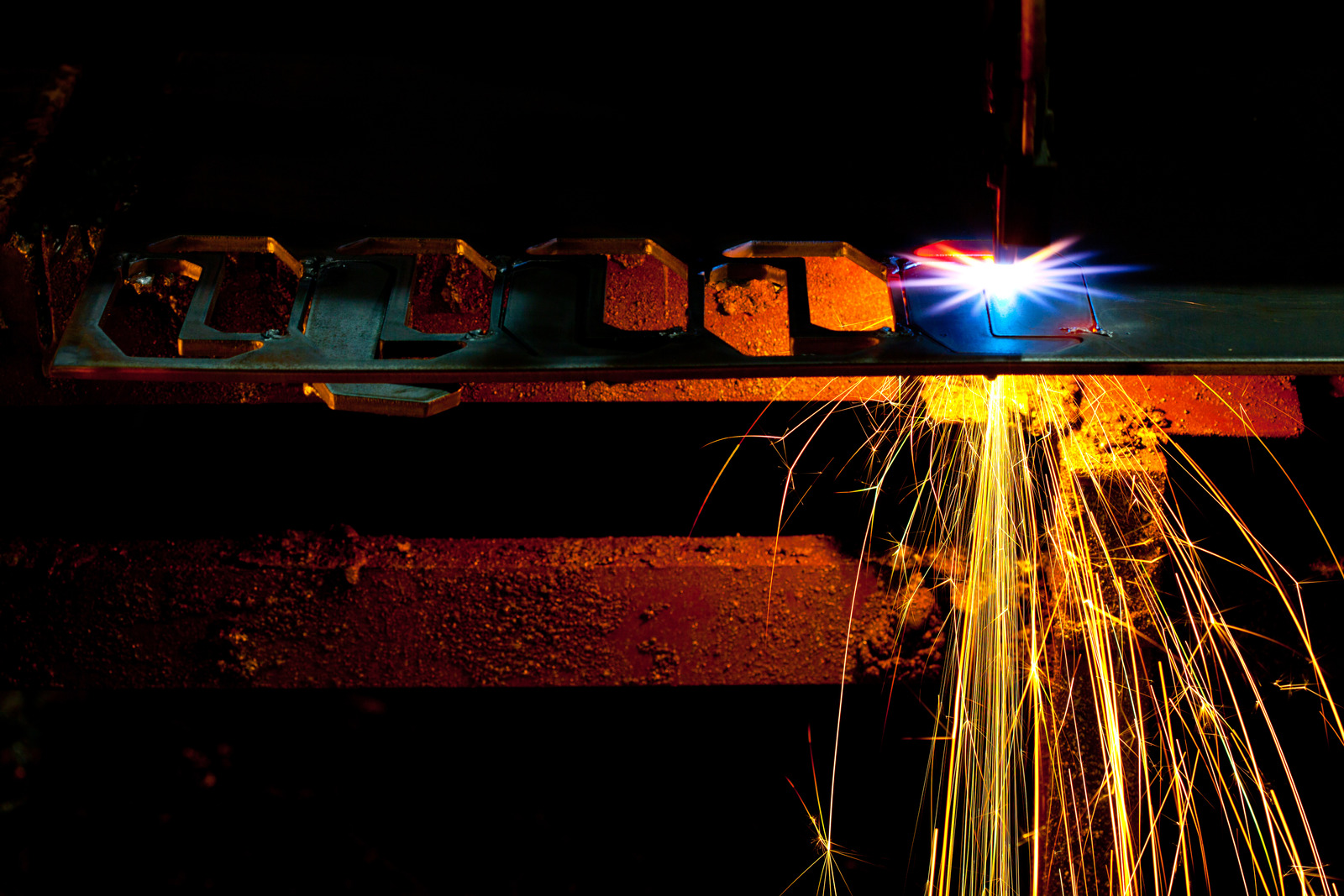
Preparing Zinc for Laser Cutting
Types of Zinc
cutter Zinc is a metal that is commonly used in products such as jewelry, coins, and belts. It is a highly malleable and ductile material, which makes it perfect for laser cutting. There are two main types of zinc: electroplated and hot-dipped.
Electroplated zinc, also known as Galvanized Zinc, is zinc that is electroplated onto a substrate, such as steel. This type of zinc is less resistant to scratches and is typically found in jewelry, coins, belts, and other decorative items.
Fumes and Safety Considerations
cutter When it comes to laser cutting zinc, it’s important to consider the potential hazards that come with the process. Specifically, the fumes that can be created when the laser interacts with the zinc. The zinc will begin to vaporize as soon as it experiences the heat from the laser, creating smoke and tiny particles of zinc oxide dust.
This dust can be extremely hazardous to one’s health, so it’s important to take safety precautions. This means wearing a protective breathing mask, long clothing to protect exposed skin, and working in a well ventilated area.
Cleaning and Surface Preparations
cut When laser cutting zinc, the first step is to ensure that the surface of the zinc is clean and free from foreign material. This not only ensures that the laser cutter will produce the desired results but that there is no risk of introducing contaminants into the environment. When preparing the material for laser cutting, the best results are achieved when the material is cleaned and surface prepared prior to laser cutting.
Setting Parameters for Optimal Results
Parameters of laser cutting
energy level When it comes to laser cutting zinc, the right parameters are essential for achieving the best results. To get the most accurate and detailed results, you need to find the perfect laser energy level for the job. This means adjusting the speed, power, and focus of the laser beam to achieve a specific result.
The speed at which the laser beam is fired is an important factor when it comes to achieving the desired results with a laser cutter. If the speed is too slow, then the laser beam may not cut all the way through the material.
Finding the best focus and focal power
setting Finding the best focus and focal power is key to getting the best results when laser cutting zinc. The focus and focal power you use will depend on the type of laser cutter you have and the type of material you are engraving. Focusing and adjusting the focal power to the right levels will help you create the perfect laser settings for the job.
Obtaining the correct cut width, speed and power
engraving settings Getting the best results out of laser cutting zinc will depend on various settings, such as cut width, speed, and power. To get the most out of zinc with a laser cutter, you will need to fine-tune these parameters. Cut Width – This is the size of the beam that is used to cut the zinc.
A smaller cut width is better for intricate designs, while a wider cut width is needed for faster, coarser cutting.
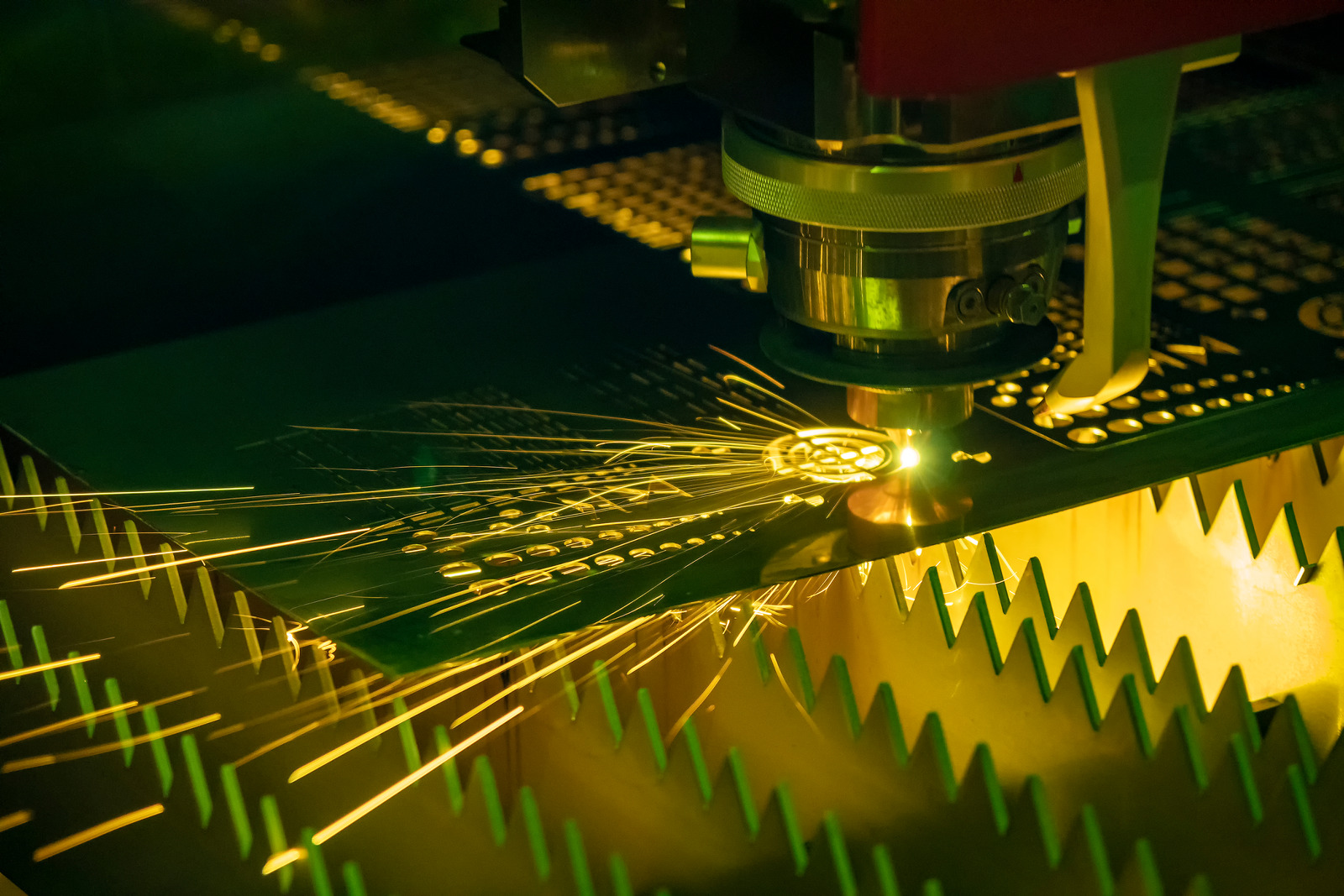
Post-Cutting of Zinc
Cooling and Finishing the Cut
cutter The Cooling and Finishing the Cut section of laser cutting zinc is a critical step to getting the best results. After the laser cutter has finished the cutting job, it’s important to ensure that the metal is cooled properly. Zinc has a high heat tolerance, but it is still prone to warping and distortion when it’s exposed to high temperatures post-cutting.
This could ruin the final results. To prevent this, allow the metal to cool naturally in whatever state it was cut in.
Inspecting the Results
job After the laser cutting process is complete, it is important to inspect the results. To do this, start by evaluating the quality of the cut path. Make sure there are no burrs or spikes, which could be a sign of an improperly designed DXF or an incorrect laser cutting setting.
Next, check that all of the edges are clean and sharp. Any roughness indicates an improper focus setting or an undersized nozzle. Once you have verified that the laser cutter has cut the zinc cleanly, you can determine the accuracy of your project.
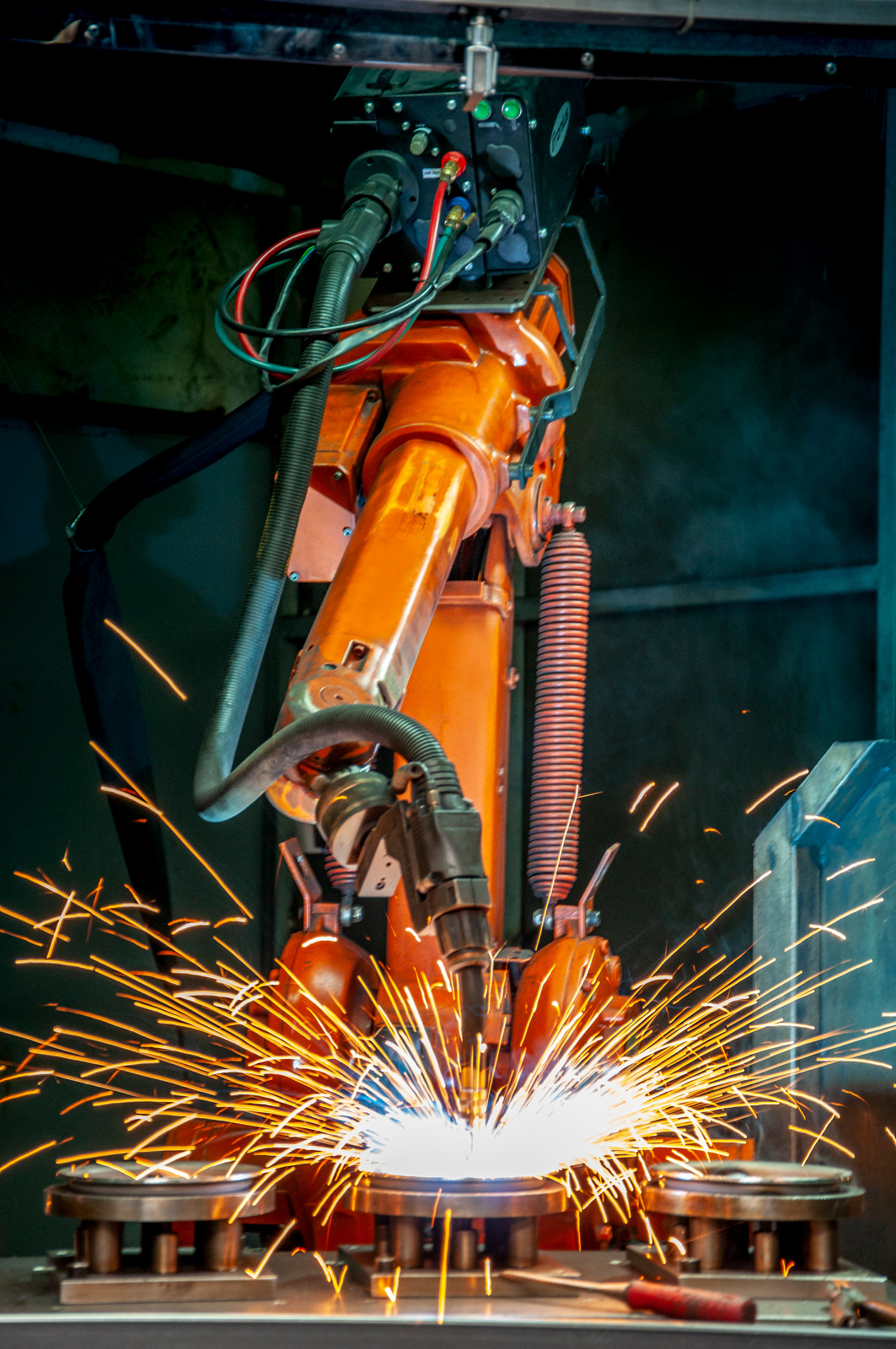
Can you laser-cut zinc?
cutting Yes, you can laser-cut zinc! Laser cutting is a type of machining that uses a laser beam to slice through metal, plastic, or other materials. This process is very precise, and provides a high-quality cut with very little post-processing required.
Depending on the material, thickness, and power of the laser cutter, you can achieve the perfect laser cutting results on zinc. When it comes to obtaining the best results with laser-cutting zinc, the speed, power, and focus of the laser is key. To start, you’ll want to optimize the laser speed so it’s not too fast, or too slow.
Conclusion
Summarizing the Important Points
In conclusion, when looking for the best results when laser cutting zinc, there are several important points to consider. First, make sure to choose the right settings on the laser cutter for different thicknesses of zinc materials. Second, always make sure the material is properly secured and secure any loose pieces of material.
Third, take into account the type of laser cutter, wattage, and speed all have an effect on the quality of laser cutting.
Tips for Even Better Results
engraving When laser cutting zinc, there are a few extra tips for achieving even better results. Here are some things to keep in mind for finding perfect laser engraving results. First, use the best tools available.
Investing in a quality laser cutter designed for cutting zinc is key. Consider professional-grade machines that are capable of accurate and consistent cuts. Many professional grade machines offer higher powered lasers and options for adjustable cutting speeds, which provide the most precision when cutting zinc.
Next, make sure the thickness of the zinc material you’re using is consistent. This is important for ensuring even, precise laser cuts.