3D printing has revolutionized the way we produce items, positively affecting a variety of industries. At the forefront of this revolution has been laser cutting, which is increasingly being used to create 3D printed objects. Discover how laser cutting helps improve the accuracy, effectiveness, and speed of 3D printing operations in this exploration of laser cutting applications in 3D printing.
Benefits of Laser Cutting for 3D Printing
Ease of Use
Exploring Laser Cutting Applications in 3D Printing, Benefits of Laser Cutting for 3D Printing: Ease of Use When it comes to 3D printing, laser cutting offers many advantages compared to traditional methods. One of the most notable benefits of laser cutting is its ease of use. With laser cutting, the process is fast and simple, requiring limited setup time, and minimal to no manual labor.
The laser beam does all the work, resulting in an extremely precise and high-quality result.
Precision
When it comes to precision, laser cutting for 3D printing provides amazing benefits. With laser cutting, you can get intricate and highly detailed patterns that would not be possible with other types of 3D printing. Laser additive manufacturing is one of the latest technological advancements in 3D printing and has great precision, accuracy, and resolution.
The laser cutting system works by emitting a beam of energy at varying degrees of intensity and focus to the material being cut. This makes the material easier to manipulate and shape into intricate patterns.
Flexibility
When it comes to 3D printing, laser cutting is the perfect complement. With laser cutting for 3D printing, you can create intricate, precise and complex objects that are impossible to create with conventional 3D printing methods. While 3D printing can produce parts with impressive precision, laser cutting for 3D printing offers an even greater degree of flexibility.
Popular Laser Cutting Applications
Laser Repairs
Laser repairs is a key application of laser additive manufacturing and 3D printing technology. Using a laser cutter, highly precise and localized refinements can be made to 3D-printed objects, enabling repair, modification and finishing processes. This makes it possible to repair or replace parts that were 3D printed, as well as to expand functionality and quality.
Laser repair techniques can also be applied to other non-printed parts to extend their life or even enhance their structural integrity. By using laser-assisted additive manufacturing, 3D-printed objects can be repaired in situ, resulting in a finished product.
Functional Components
One of the great advantages of using laser cutting applications in 3D printing is its ability to produce highly detailed, functional components. By combining the accuracy and precision of a laser cutter with the wide range of materials used in 3D printing, users are able to produce components with incredible detail and durability.
Artistic Pieces
When it comes to 3D printing and laser cutting applications, artistic pieces represent one of the most popular and inspiring uses of this technology. Laser cutting allows users to create intricate designs and decorations in wood, plastic, fabric, and even metal. With a laser cutter, it is possible to create artworks with intricate details, captivating shapes, and stunning effects.
One of the most popular applications of laser cutting when it comes to artistic pieces is in the creation of custom made jewelry or sculpture. It is possible to create complex shapes and intricate detail with a great degree of accuracy that cannot be achieved with traditional tooling techniques.
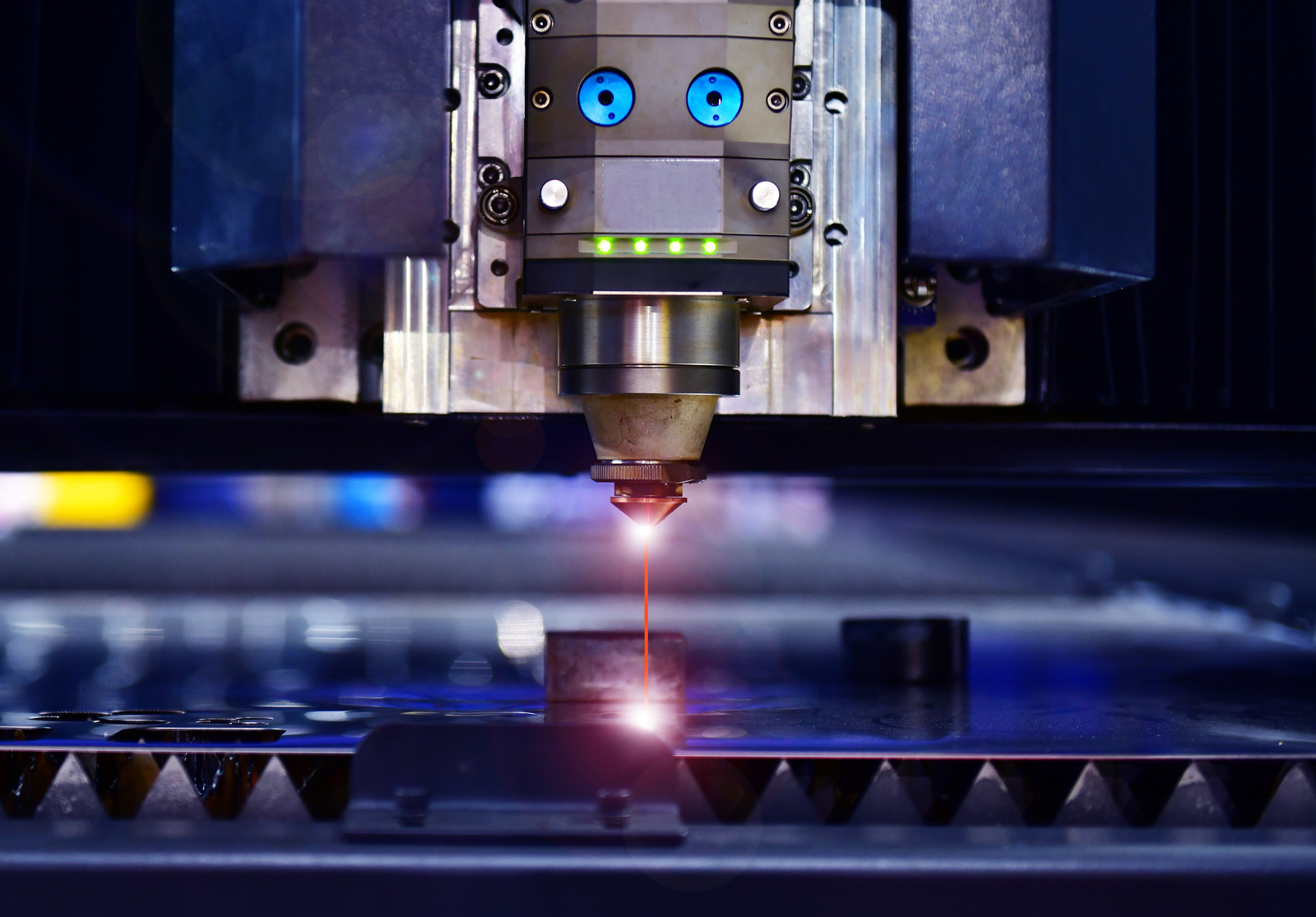
Adaptability and Innovation
Design Optimization
When it comes to 3D printing, design optimization is essential for successful fabrication. In the context of 3D printing, design optimization refers to the ability to tailor a 3D model using laser cutting applications to achieve a certain look or functionality. Laser additive manufacturing, where a laser is used to melt, fuse and bond particles together, is one way to optimize designs.
This process is often referred to as laser cutting or laser engraving. Using laser technology to optimize 3D printed designs allows for greater flexibility and control when designing parts.
Automation
When it comes to automation, 3D printing and laser cutting are two of the most popular tools in the modern-day industry. Not only are they capable of producing complex components at high speeds, but they are also highly adaptable to new applications due to their flexibility. 3D printing is a form of additive manufacturing, which involves depositing plastic and metal material into a design form in layers, while laser cutting is a form of subtractive manufacturing, in which metal and other materials are cut from a sheet by a laser beam.
Design Customization
When it comes to 3D printing and laser cutting applications, design customization is a major factor. The ability to tweak the design with precision allows for greater innovation and creativity. Laser cutting has allowed for greater adaptability by giving user’s the ability to create very intricate pieces, oftentimes with more precision than with 3D printing.
When it comes to 3D printing, the user has to design the model beforehand, however with laser cutting, one can make custom designs from existing materials after the material has been cut.
Challenges of Laser Cutting and 3D Printing
Safety Considerations
When it comes to 3D printing, safety considerations are paramount. With laser additive manufacturing, the safety concerns are even greater. Laser cutting and 3D printing involves working with dangerously powerful and precise laser beams.
Therefore, it’s important to take proper precautions when exploring laser cutting applications in 3D printing. When working with these powerful laser beams, there are several safety considerations that must be taken into account. First, it’s important to always wear the appropriate eye protection, such as goggles or a face shield.
High Upfront Costs
One of the primary challenges when it comes to exploring 3D printing and laser cutting applications in 3D printing is the cost associated. The upfront investment for the equipment can be quite a high, particularly when it comes to the more sophisticated machines. While it’s true that you can purchase a basic 3D printer for less than $1,000, with laser cutting and laser additive manufacturing machines you’re looking at not just the cost of the machine itself, but also the cost of the materials and supplies necessary to use the machine.
Machines and Materials
Services that utilize 3D printing and laser cutting to create customized products are becoming increasingly prevalent in today’s society. The machines and materials used in these services are capable of producing highly intricate, detailed designs. 3D printing is a type of additive manufacturing technology that builds up objects layer by layer using various materials, such as plastic, metal, or resin.
The most common types of 3D printers are FDM (Fused Deposition Modeling) and SLA (Stereolithography).
How is laser used in 3D printing?
3D printing has revolutionized the manufacturing industry, allowing for rapid prototyping and production of small parts and components. In particular, laser cutting has become an integral part of 3D printing technology, as it can be used to produce fine details and intricate shapes that cannot be achieved with other methods. Laser cutting is a process that uses intense, focused light to cut or melt materials.
In 3D printing, this technology is used to precisely cut or melt the material that is deposited during the printing process. This type of 3D printing, often referred to as laser additive manufacturing, utilizes the laser cutting process to create complex geometries and intricate details that can’t be produced with traditional methods.
Can you laser cut with a 3D printer?
The short answer to the question, “Can you laser cut with a 3D printer?” is yes, you can. The process is known as Laser Additive Manufacturing (LAM) and involves using an integrated laser cutter and 3D printer to cut materials into 3D shapes and sizes.
LAM combines both laser cutting and 3D printing technologies to create complex geometries and shapes. The laser is used to precisely cut and shape the 3D printing material according to predetermined specifications. The result is complex geometries with smooth surfaces and no post-processing.
The advantages of using LAM are numerous, including precision and repeatability.
Conclusion
Overview of Benefits and Challenges
As 3D printing continues to evolve, so too do advances in laser additive manufacturing. Laser cutting has become an increasingly popular option for various 3D printing applications due to its benefits and versatility. The key benefits of using laser cutting for 3D printing include precision, speed, and ease of use.
With laser cutting, 3D printers can more precisely and quickly produce parts for a variety of industries – from the automotive to medical sectors. The technology can also be applied on any scale, from small-scale prototypes to large-scale production runs, and is more accurate than other methods of additive manufacturing.
Summary
In conclusion, exploring laser cutting applications as part of 3D printing technology has revealed a plethora of potential solutions and possibilities. Laser additive manufacturing and 3D printing have opened up an entirely new world of design and manufacturing solutions, enabling users to rapidly create and fabricate parts and products in a wide range of materials. The advent of laser cutters and 3D printers allows for the fabrication of uniquely designed components that weren’t previously possible with traditional manufacturing techniques.
Wrap Up
In conclusion, exploring laser cutting applications in 3D printing is a fascinating and ever-evolving field. This technology is still new, but it allows for rapid production of complex components. It combines the traditional art of laser cutting with the ever-expanding possibilities of 3D printing.
By using this method, complex materials can be formed quickly in an efficient and repeatable manner, and cost reduction of components can be realized.