The development of laser cutting tolerance monitoring systems can be pretty complex, but automation tools can make this process more efficient. Exploring these automation tools can help Laser Cutting operations become more accurate and productive, while reducing the number of mistakes made due to changing tolerances. In this article, we will discuss the automation tools available, and how they can be used to monitor and adjust laser cutting tolerances.
Automation versus Manual Control
Pros and Cons of Automation
When it comes to laser cutting, automation offers many advantages over manual control. Automation allows for more precise and consistent cuts, as well as high-speed production. Automated systems also require less labor and can reduce the potential for error and waste.
The primary benefit of automated laser cutting is that it eliminates user error and produces consistent, accurate cuts. Automated systems can produce extremely precise cuts and radii, with tolerances of a few hundredths of an inch or less.
Benefits of Utilizing Automation Tools
automation When it comes to cutting pieces of metal, plastic, or other materials accurately and effectively, laser cutting tools are the most efficient and cost-effective option. Automation tools help automate and monitor the process, taking out the guesswork and ensuring that products are cut precisely according to exact specifications. Automation tools are especially beneficial in operations where tolerances are important, such as creating precision parts for automotive or aerospace applications.
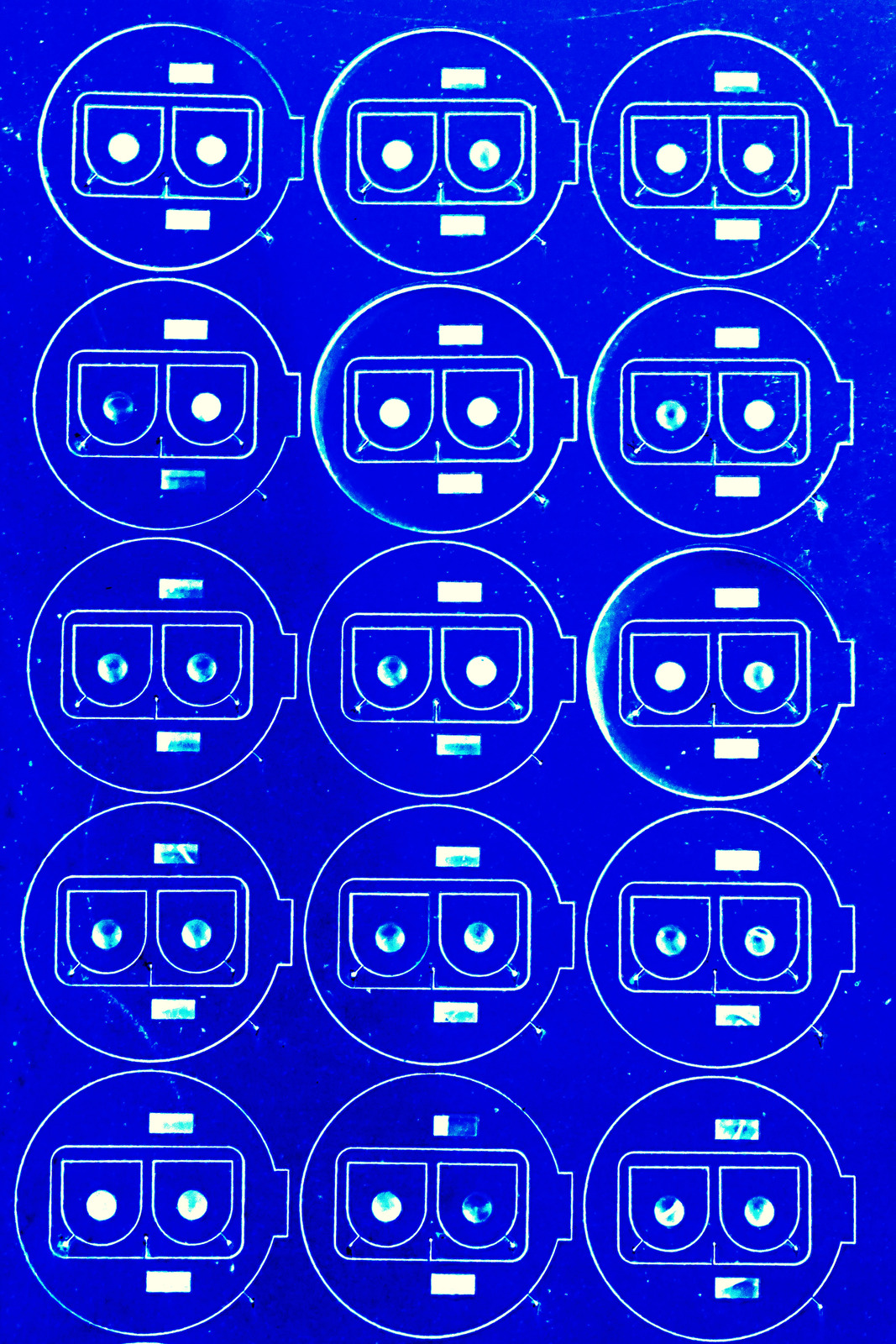
Laser Cutting Instrumentation
Sensors and Lasers
instrumentation When exploring automation tools to help monitor and adjust laser cutting tolerances, it is important to understand the components involved in a laser cutting instrumentation setup. One of the core components of any laser cutting machine is the laser itself. Laser cutters use focused beams of light to create precise cuts of material.
These focused lasers are usually generated by gas tubes or solid-state lasers, depending on the type and size of machine being used. Next in the automation setup are the sensors.
Types of Lasers
instrumentation Exploring different types of lasers, their capabilities, and how they can be integrated into laser cutting instrumentation is key to understanding the accuracy of the process. Lasers come in many shapes and sizes, but cutting lasers are usually either CO2 (carbon dioxide) lasers, neodymium-doped yttrium aluminum garnet (Nd: YAG), or diode-pumped solid-state (DPSS) lasers.
Automation Tools used to Monitor and Adjust Laser Cutting Tolerances
tolerances Automation tools can be a powerful way to help monitor and adjust laser cutting tolerances. Specifically, laser cutting instrumentation can provide an automated set of means by which to measure, monitor and adjust laser cutting tolerances. Such instruments generally measure the amount of energy inputted into the laser cutting process, the output power, the size of the cut, the beam width, and the exact location of the cut.
In addition to measuring and monitoring, laser cutting instruments can also be used to adjust the cutting tolerances of the laser cutter as necessary.
An In-Depth Look at Automation Tools
Cutting Acquisition Programs
process Cutting acquisition programs are pieces of software designed to help with the laser cutting process. They allow operators to define various parameters within the laser cutter and automate the entire process. This helps ensure that material is cut to the exact specifications and tolerances needed.
Cutting acquisition programs can be tailored to the specific type and make of the laser cutter being used. This ensures that they are compatible and produces the most accurate and consistent laser cutting process possible.
Material Optimization Tools
software When it comes to laser cutting, material optimization tools are essential. These tools are used to help ensure that components are cut as precisely as possible and within the given tolerances. This is crucial when creating parts with complex shapes, because the smallest detail can make a huge difference in the finished product.
Material optimization tools are used to identify and compensate for various imperfections in the surface of the material being cut. These imperfections could include tiny grooves, variations in the thickness of the material, or defects in the cutting line.
Feed Systems
machine Feed Systems play a critical role in laser cutting, as they support and drive the laser cutting process. Feed systems are responsible for guiding the laser cutting tool and ensuring that it maintains the correct depth and speed. In order to maintain accuracy and precision, laser cutters need to be adjusted when necessary in order to achieve the desired results.
Quality Management and Tracking Software
tolerance When it comes to optimizing laser cutting tolerances, quality management and tracking software are essential automation tools. Quality management and tracking software help to ensure that your laser cutting devices remain accurate and efficient while being used in production. Quality management software allows machine operators to quickly view, measure, and analyze results in real-time, providing faster feedback and more accurate laser cutting tolerances.
With quality management and tracking software, machine operators can easily set and monitor the desired cutting tolerances and parameters.
Applications for Automation Tools
Automated Laser Cutting
machine Automated laser cutting is a cutting technology used to cut materials of different types, from wood to metals, with a high-power laser beam. This type of cutting is often used in manufacturing and other industrial uses, but can also be used in DIY projects. Automated laser cutting machines come in a variety of shapes and sizes, and can be used to cut not just metal, but also plastics, fabrics, paper and many other materials.
Automation tools are used to help effectively monitor and adjust laser cutting tolerances as cuts are made. When this kind of precision is necessary in metal fabrication, there is no better way to do it than with automated laser cutting.
Automated Edge Trimming
tolerances When it comes to laser cutting, automated edge trimming is a hugely useful automation tool. This tool uses lasers to trim off any excess material left over after the laser cutting process, ensuring that the edges of the product meet exacting tolerances. This helps to ensure that all the parts are perfectly cut and accurately fit together.
The automated edge trimming process works by using a laser cutter. This laser cutter follows the outline of the product that was cut by the initial laser cutting tool.
Conclusion
The Advantages of Automation Tools for Laser Cutting
Automation tools are essential for achieving the highest standard of laser cutting accuracy and repeatability. Automation tools such as laser cutting machines enable improved production efficiency, quality assurance, and cost reduction for laser cutting applications. Automation tools help to monitor and adjust laser cutting tolerances during production runs, thereby ensuring accurate and consistent laser cutting results.
Challenges with Automated Controls
tolerances The use of automation tools to monitor and adjust laser cutting tolerances can come with its own set of challenges. Although automation offers numerous benefits, including improved accuracy, increased productivity, and material savings, there are a few considerations to keep in mind before integrating automation into your cutting process. Firstly, not all laser cutting tools are compatible with automation, so it is important to make sure the right tool is used.
Considerations for Determining whether Automation Tools are Right for You
machine One of the key considerations for determining whether automation tools are right for you when it comes to laser cutting tolerances is the complexity of the job. If you’re cutting complex shapes or intricate details, an automation tool can be a great way to ensure accuracy. Automation tools also come in handy for jobs that need to be completed quickly and for repetitive tasks, where the settings rarely change.
It’s worth remembering, however, that automation tools are often more expensive than manual methods, can be complex to program, and may require additional training for operators.