Laser cutting is a valuable tool in today’s world of automation and manufacturing. Whether used for cutting thin metals or intricate fabrics, laser cutting technology has revolutionized the way we think about production. However, when it comes to laser cutting, cost is an important factor to consider. In this article, we will be examining the various factors that affect laser cutting cost and how they can be managed to bring down total costs.
Material
What types of materials lend themselves to laser cutting
When it comes to laser cutting, many factors come into play when it comes to how much it costs. One of the most key elements to determine when it comes to cost determination is the type of material used. Different materials require different settings and techniques in order to be cut using a laser cutter, some of which are more expensive to process than others.
Some materials lend themselves better to laser cutting than others due to their properties. Some materials are more reflective than others, for example aluminum. This means that when it hits the laser, it reflects more energy back to the laser source, making the process of cutting it more difficult.
Quality of material and its effect on cost
When it comes to laser cutting costs, one of the most important factors to consider is the quality of the material. Using materials that have a higher quality often leads to higher cutting costs, but they are often also more reliable and more precise. Higher quality materials can also stand up to higher temperatures and pressures, making them ideal for more complicated cutting operations.
In addition, quality materials often require fewer passes, which can help to reduce overall cutting costs. On the other hand, lower quality materials might be more cost-effective, but they often require more passes, leading to higher Laser Cutting Cost. This can make it difficult to achieve accuracy and quality when laser cutting materials.
Labor
The training of the laser operator
When it comes to the costs associated with laser cutting, the experience and training of the laser operator can play a big role. Laser cutting involves highly precise and intricate processes, so the skills and knowledge of the operator are essential for ensuring the accuracy and quality of the results. The laser operator must have a strong understanding of the machine, its settings and capabilities, the materials it’s cutting, and the overall fabrication process.
Automation and its impact on labor costs
When it comes to trying to reduce the labor costs associated with laser cutting, automation can be a big help. Automation can allow you to cut down on wasted time, reduce errors, and ensure continuous production. This is because automation eliminates the need for manual labor in some tasks, including controlling the laser cutting system, ensuring consistent speed and accuracy, and generally just keeping an eye on the system.
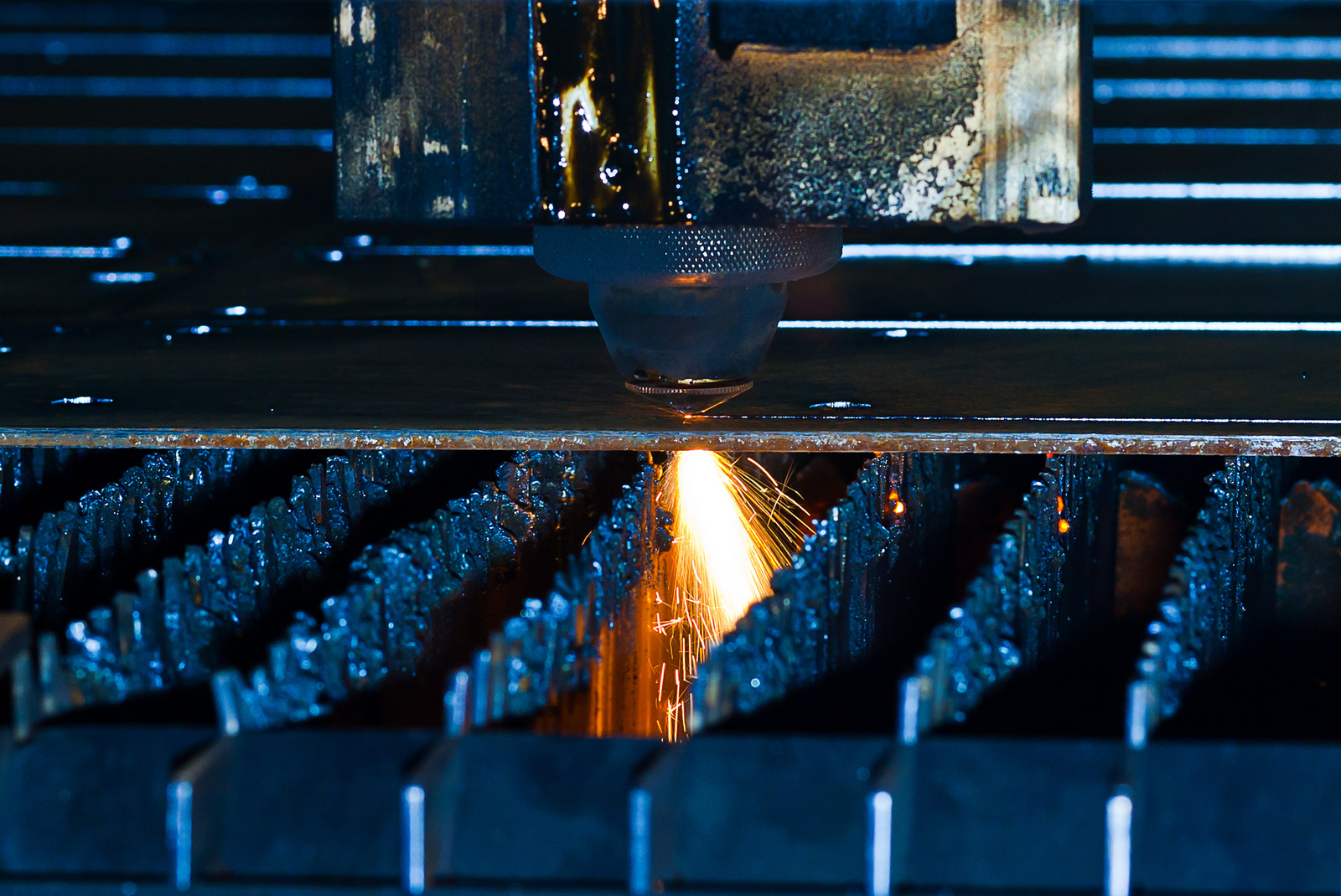
Time
Preparing the material for the laser machine
cost Having the correct material setup is a crucial element when it comes to laser cutting costs and time. Properly preparing the material for the laser machine ensures the cutting process will be accurate and will provide you with the desired result. Before embarking on the actual laser cutting process, one must consider the different factors which make the process more efficient.
These factors will ultimately play a role in the laser cutting costs and time. The first factor to consider is the actual material being used.
Impact of job complexity on completion time
When talking about the various factors that affect laser cutting costs and time, job complexity is an especially important factor to consider. This is because more complex or intricate laser cutting jobs typically require more time to plan, prepare, and execute. For example, if a job requires cutting intricate shapes and designs out of a variety of materials, the laser cutting process will be more complex and require more time to complete than a job requiring precise cutouts from a single material.
Equipment
The type of laser cutting machine and its cost
When it comes to laser cutting, the type of machine used can have a huge impact on the cost. Laser cutters come in a variety of shapes, sizes and power. The cost of the machine will often be dependent on the features and power it offers.
For example, higher power laser cutters are likely to cost more than those with lower power, but the flexibility and accuracy of a higher power machine could help you save time and money in the long run. The size of the machine will also affect the cost.
Maintenance of the laser machine and its effect on cost
When it comes to laser cutting, maintenance of the laser machine is one of the major factors that affects the cost of the equipment. Regular upkeep and maintenance of the equipment helps to ensure that it performs effectively and is running safely. Without proper maintenance, the laser cutter can quickly become unsafe and inefficient, resulting in costly repairs or replacement.
The type and quality of the maintenance needed for the laser machine is largely dependent on the operating environment and usage.

Energy
Cost of power affects job complexity
When it comes to commercial laser cutting, the cost of energy is often a major factor that determines the complexity of the job. This is because laser cutting requires the use of a powerful laser cutter, which requires a source of electricity. Therefore, the cost associated with powering the laser cutter can have a direct impact on the cost of the cutting job.
When it comes to commercial laser cutting, the laser cutter is powered with a high-voltage power supply, which is typically rated in Watts.
Impact of waste removal system on total energy cost
The waste removal system is an important factor that affects the total energy cost of laser cutting. The amount of energy consumed is related to the speed at which the laser beam moves across the material. A high-speed laser beam will generate more heat and require more energy to cut through the material.
In addition to the actual energy required for cutting, the waste removal system also affects the total energy cost of the laser cutting process. The waste material generated during laser cutting must be extracted away from the cutting area in order to prevent damage to the machine and materials being worked on. This extraction process requires energy, as the often high-pressure exhaust system must be maintained.
Pre-Processing
Any preparations needed for the laser cut material
Before any laser cutting process takes place, the material that is going to be cut needs to be sufficiently prepared. This isn’t just necessary for the sake of achieving a quality cut, but it can also have an effect on the laser cutting costs. So, what preparations need to be done before you can begin laser cutting?
The most important thing is to make sure that the material that is being used is suitable for laser cutting in the first place. Some materials can react to laser cutting in unpredictable ways, and trying to cut these materials can lead to excess costs if the cut is unsuccessful. Additionally, the material needs to be cleaned and coated correctly to ensure the best possible result.
Additional costs of pre-processing
Pre-processing is an important step in laser cutting. It involves tasks that must be completed prior to the actual cutting process, such as applying masks, applying adhesives, and aligning the material. It is an essential part of the laser cutting process, since it prepares the material for laser cutting and helps to ensure that the finished product is free of defects.
Unfortunately, pre-processing comes with additional cost factors. In addition to the cost of the materials, there are several other cost factors to consider when it comes to pre-processing. Of these, the cost of any additional materials required, the cost of labor, and the cost of equipment are the most significant.
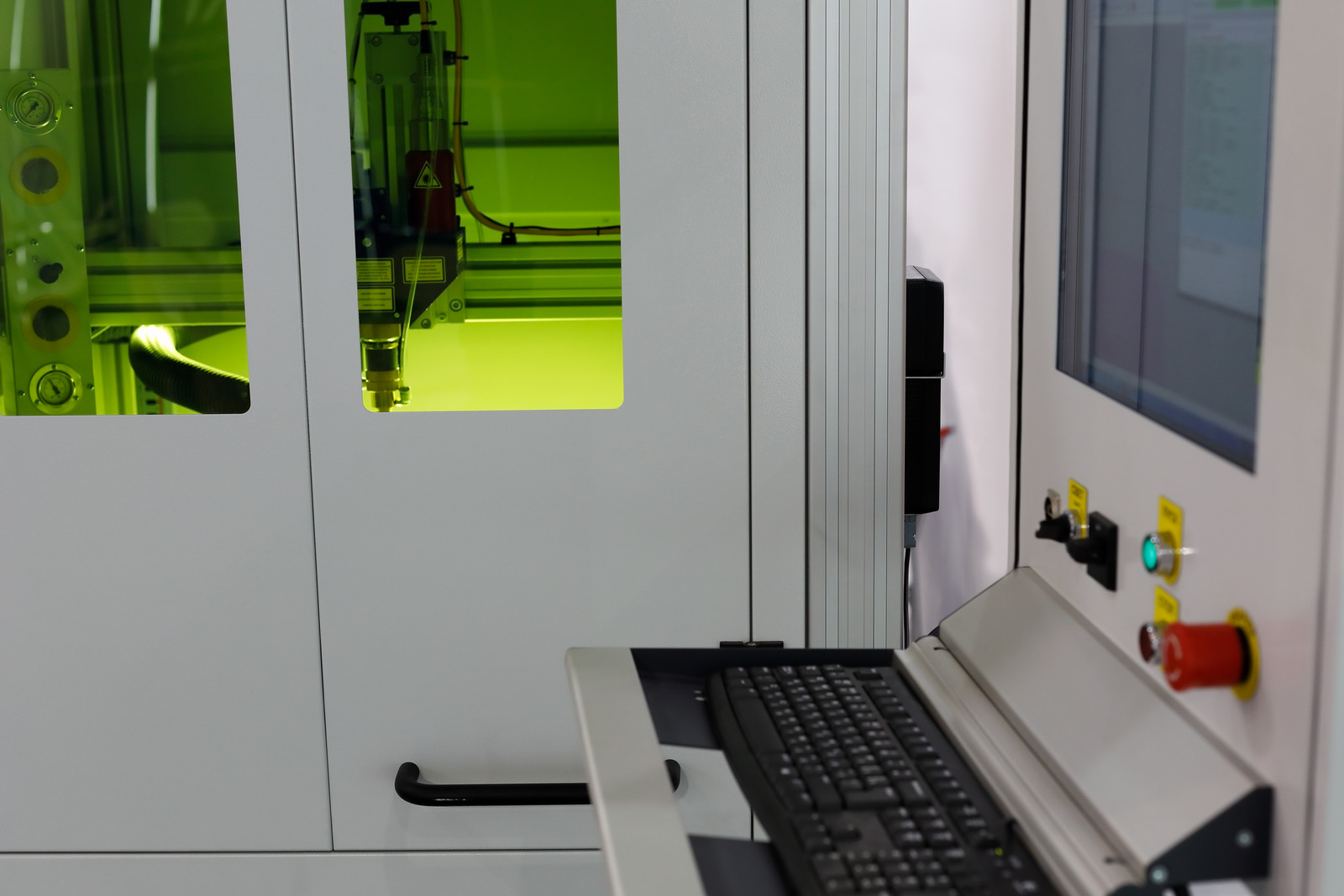
How much does laser cut cost?
The cost of laser cutting can vary depending on a variety of factors. It depends on the type of material you are cutting, the size of the cut, the type of laser cutter used, the complexity of the shape that is being cut, and the power of the laser cutter used. The type of material you are cutting can affect the overall cost of a laser cutting project.
Materials such as metal can be expensive to laser cut due to the complexity of cutting and the type of laser cutter required to cut through the material. On the other hand, materials such as wood, paper, or foam are much less expensive and require less power to be cut through.
Conclusion
Recap of factors that affect laser cutting cost
When analyzing the various factors that affect laser cutting cost, there are a few important things to consider. The first is the type of laser cutter used. Some laser cutters are more advanced and powerful than others, meaning they cost more to operate.
Additionally, the speed of the laser cutter plays a significant role in cost. Slower machines require more time and, therefore, are more expensive to use than faster machines. Material costs also have a big impact on laser cutting cost.
The thickness and type of material will both influence the cost, as well as the amount of material needed for the job.
Tips for reducing cost and increasing efficiency
Examining the various factors that affect laser cutting cost is important in order to determine the best cutting method for a given job. Key factors to consider include laser wattage, material thickness, material type, and cutting speed.
- Ensure that you are selecting the right laser power for the job. Higher power can result in faster cutting speeds but may be more expensive.
- Consider the different materials that are available when selecting the right cutting material. Different materials may require different laser power levels and result in different costs.
- Utilize automated nesting to save on material costs by nesting parts together in the most efficient way and reducing waste.
- Invest in a good quality and reliable cutting machine for increased efficiency and longevity, allowing for longer periods of use with less downtime.
- Consider advanced cutting options such as interior shape adjustment and bevel cutting for more complex designs. These options can save time, labor, and material costs.
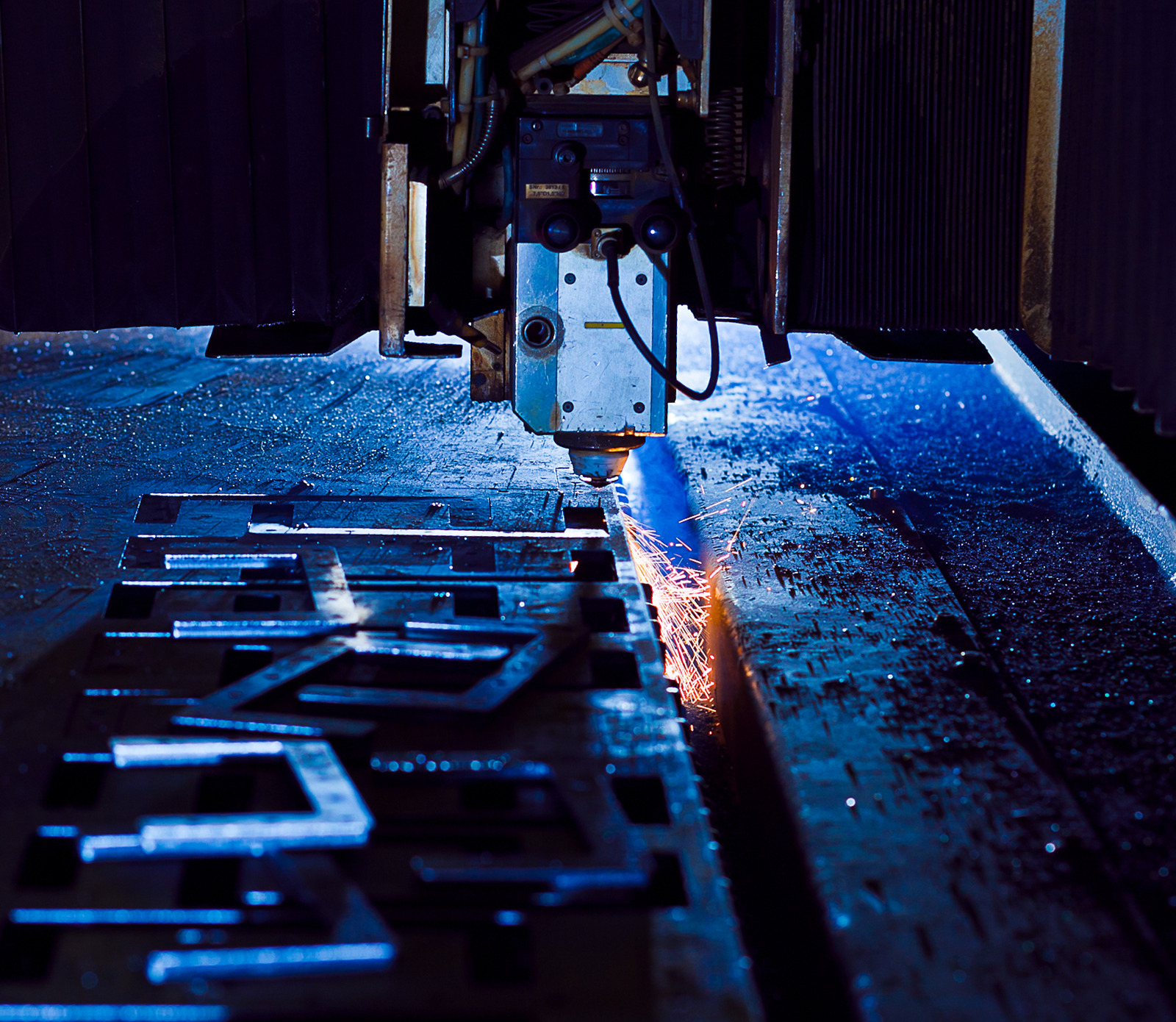