In this article, we will explore the process of configuring laser cut elevation designs for maximum accuracy. From incorporating CAD/CAM systems in your design to understanding the details of power settings, we will provide a comprehensive overview of the techniques you can employ to ensure your elevation designs are accurately executed with laser cutting.
Best Practices for Achieving Maximum Accuracy
Consider Mechanical Accuracy of Laser Cutters
accuracy When it comes to configuring laser cut elevation designs for maximum accuracy, one of the most important considerations is the mechanical accuracy of your laser cutter. Laser cutters are incredibly precise tools, but there are still inherent limitations and sources of inaccuracy that you should be aware of in order to maximize accuracy in your cut. To start, it’s important to consider what type of laser cutter you will be using.
Ensure Material Thickness is Suitable
accuracy In order to achieve maximum accuracy with laser cutting designs, it is important to ensure material thickness is suitable for the laser cutter. Different laser cutters are designed for different thicknesses of materials, and so it is important to check what range of thicknesses the laser cutter is suitable for.
Analyze Vector Design Element Parameters
accuracy Elevation designs are often complicated and require accuracy in order to produce precise results. Configuring laser cut elevation designs to achieve the highest possible accuracy is not a straightforward process. It’s important to analyze all the vector design element parameters for your project, including the heights and widths of shapes, the distance between shapes, and the angles of the shapes.
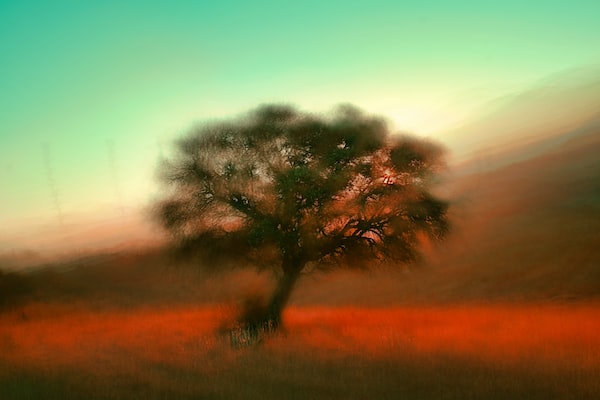
Technologies for Achieving Maximum Accuracy
Automated Registration and Positioning
accuracy Accuracy is an important factor when it comes to laser cutting, especially when producing intricate designs with specialized materials. Automated registration and positioning technologies help provide that accuracy, allowing you to achieve a higher level of precision and uniformity overall. Automated registration and positioning systems use a variety of methods to guarantee accuracy in laser cutting designs.
Some systems work by using a camera to record the exact placement of the laser beam on the material before and after each cut. This information is then compared to a design file, helping the system make any necessary adjustments to keep the cuts accurate.
Closed Loop Positioning
Closed Loop Positioning is a key part of achieving maximum accuracy when laser cutting designs. This technology works by providing input to a laser cutter’s cutting head in the form of feedback. This feedback includes the height and position of the cutter head relative to the material being cut.
By using Closed Loop Positioning, the laser cutter is able to continuously adjust the head position and pressure to ensure a steady and accurate cut. Closed Loop Positioning is based on a servo motor, also known as a feedback system.
Advanced Laser Scanning
designs Configuring laser cut elevation designs for maximum accuracy is a complicated process that typically demands specialized skill and knowledge. As such, advanced laser scanning technologies can prove invaluable to collectors looking to achieve maximum accuracy with their designs. Advanced laser scanning utilizes a laser beam to rapidly scan objects from multiple angles to acquire precise measurements.
This data is then used to create dimensional and graphical models. By accurately capturing a model’s components, laser scanning technologies allow for precise replication of complex 3D structures and designs.
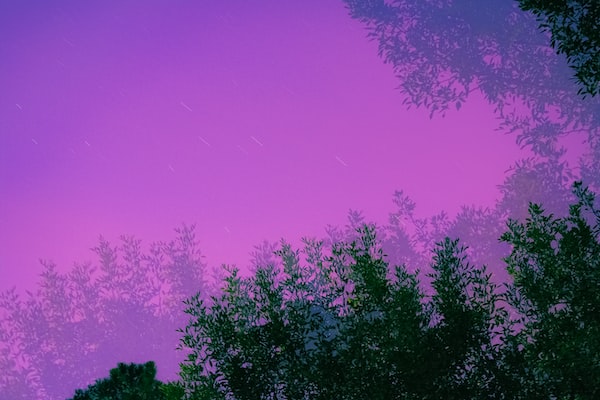
Mistakes to Avoid when Configuring Laser Cut Elevation Designs
Incorrectly Segmented Vector Shape
One of the most important mistakes to avoid when configuring laser cut elevation designs is incorrectly segmented vector shapes. Vector shapes are the outlines used to create laser cut designs, and if they are not segmented properly, the resulting design could end up being inaccurate. To segment a vector shape, the cutter needs to be given directions so it knows where to make the cuts.
These directions come in the form of lines, called nodes, that must be placed along the vector shape. These nodes need to be placed as accurately as possible, as any misplacement can result in a distorted design.
Incorrectly Set Vector Position
accuracy When it comes to configuring laser cut elevations designs for maximum accuracy, one mistake to avoid is incorrectly setting the vector position. Vectors are the line paths that the laser follows to cut the material. To get the most accurate cut, you need to make sure the vectors are positioned perfectly in the design software before being sent through the machine.
The biggest problem with incorrect vector positioning is that it can lead to uneven, inaccurate cuts.
Failing to Calibrate the Laser Head
Failing to calibrate the laser head is one of the most common mistakes when configuring laser cut elevation designs for maximum accuracy. In its simplest form, calibration is the process of setting up the laser cutter so that it is correctly aligned and to ensure that the finished product is accurate. Before a design is cut, it is important to ensure that the laser head is properly calibrated.
A badly calibrated laser head can lead to inaccuracies in the design such as incorrect dimensions, warping, or misalignment.
How precise can a laser cutter cut?
When it comes to configuring laser cut elevation designs for maximum accuracy, it’s important to understand how precise a laser cutter can cut. Laser cutting is a process in which a focused beam of light is directed onto a material to create highly accurate and intricate designs. Laser cutters are incredibly precise, making them ideal for projects that require intricate and fine detailed cuts.
The accuracy of a laser cut is determined by the size of the beam diameter, the quality of its optics, the type of laser source and the beam alignment.
How do you laser cut topography?
Laser cutting is a great way to create intricate designs out of a variety of materials, including wood, paper, and plastic. It involves using a high-powered laser to cut shapes into the surface of a material, usually with precision accuracy. When it comes to topography and elevation designs, laser cutting provides a way to quickly and accurately produce them.
To begin with, you need to create the design for your laser-cut elevation. You can make this design manually, with CAD software, or with specialized software that’s designed specifically for laser cutting.
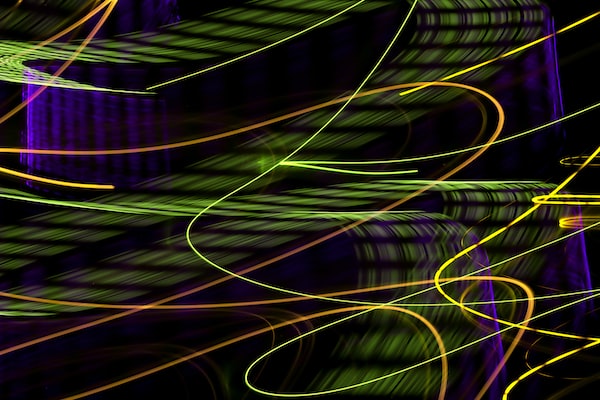
Conclusion
Summary of Tips for Achieving Maximum Accuracy
The process of configuring laser cut elevation designs for maximum accuracy is complex. To achieve the best possible outcome, there are a few critical tips to keep in mind. The first is to always use the highest quality laser cutters and materials for accuracy and consistency. Secondly, it is important to carefully consider the design of the pattern and to double check measurements and settings before the cutting begins.
- Follow the manufacturer’s instructions when setting up and using your laser cutter. Check the supplier’s guide to make sure you have the right settings before beginning a job.
- Measure the project with a metric ruler to ensure accurate cuts. Double check the measurements before each cut and make adjustments as necessary.
- Use the correct materials for your project. Choose the type, size and thickness of material for your project that will best allow for precise cuts.
- Perform regular maintenance on your laser cutter to keep it in top condition. Keep the lens and filters clean, as dirt and dust can affect the performance of the machine.
- Test a piece of scrap material first before cutting your final project. Test different settings to see which setting is right for your project. This will help ensure that you get the most accurate final product.
Benefits of Achieving Maximum Accuracy
Achieving maximum accuracy when configuring laser cut elevation designs means that you can produce highly precise and intricate products with a laser cutter. By leveraging the full capabilities of a laser cutter, you can create highly refined products that stand out among competitors. One of the most notable benefits of achieving maximum accuracy when configuring laser cut elevation designs is improved aesthetic value.
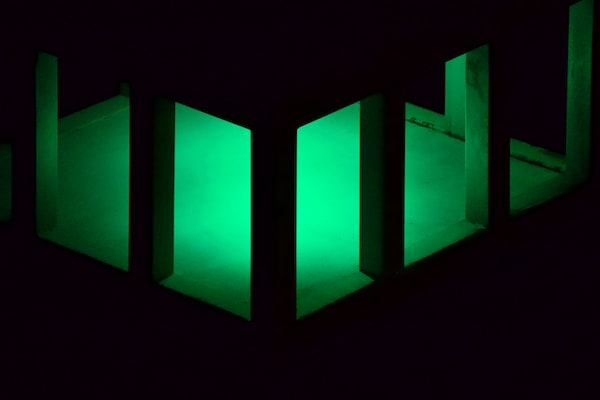