The ability to manipulate metal with lasers has greatly revolutionized the aluminium manufacturing industry. Not only can metal be machined quickly, but it can also be machined with greater precision. Laser cutting is one of the most popular ways to machine metal, but how does it compare to other aluminium manufacturing techniques? In this article, we will be comparing laser cutting to other aluminium manufacturing techniques to determine which is the most cost-effective and efficient process.
Types of Aluminium Manufacturing Techniques
Traditional Techniques
traditional cutting techniques When it comes to aluminum manufacturing, one of the most preferred metals is aluminum due to its lightweight and strength. Cutting techniques for aluminum, however, can be one of the more challenging materials to work with for any type of fabrication process. Traditional cutting techniques consist of mechanical processes carried out with tools like saws, drills and other hand tools.
These processes require manual labor, power tools, and time, making it challenging and often slow to complete projects.
Modern Techniques
traditional cutting In modern aluminium manufacturing techniques, laser cutting is one of the most sought after methods. This process involves using a laser beam to cut the aluminium into any part or shape. It is capable of working effectively with almost any aluminium type and alloys, making it one of the most preferred metals for laser cutting.
Although laser cutters are more limited in the materials they can cut compared to traditional cutting processes, laser cutters are a more energy-efficient and faster option for cutting metal compared to traditional cutting.
Advantages of Laser Cutting in Aluminium Manufacturing
Accuracy
traditional processes When it comes to accuracy, laser cutting holds clear advantages. Laser cutters are more precise than other cutting methods, making them very beneficial when it comes to manufacturing aluminum. The laser cutter will emit a focused laser beam that is very precise, meaning it can effectively work with the aluminum material.
This is one of the more challenging materials to cut, due to its lighter weight and higher hardness compared to traditional metals used in fabrication processes.
Speed
conventional methods When it comes to manufacturing aluminium, laser cutting is often one of the most preferred metal cutting processes. Laser cutters are highly efficient, versatile and offer superior speed when cutting metallic objects. In comparison to traditional cutting processes such as sawing and drilling, laser cutters are a much more energy-efficient and faster option for cutting metal.
Conventional methods of cutting metals such as sawing and drilling require the use of multiple tools and machines which can be both inefficient and time-consuming.
Design Flexibility
other methods When it comes to aluminum manufacturing, laser cutting is one of the most preferred metal cutting processes due to its flexibility and precision. Through this process, intricate details and shapes can be cut with ease. The flexibility of a laser cutter also makes it well suited to cutting aluminum, one of the more challenging materials to work with.
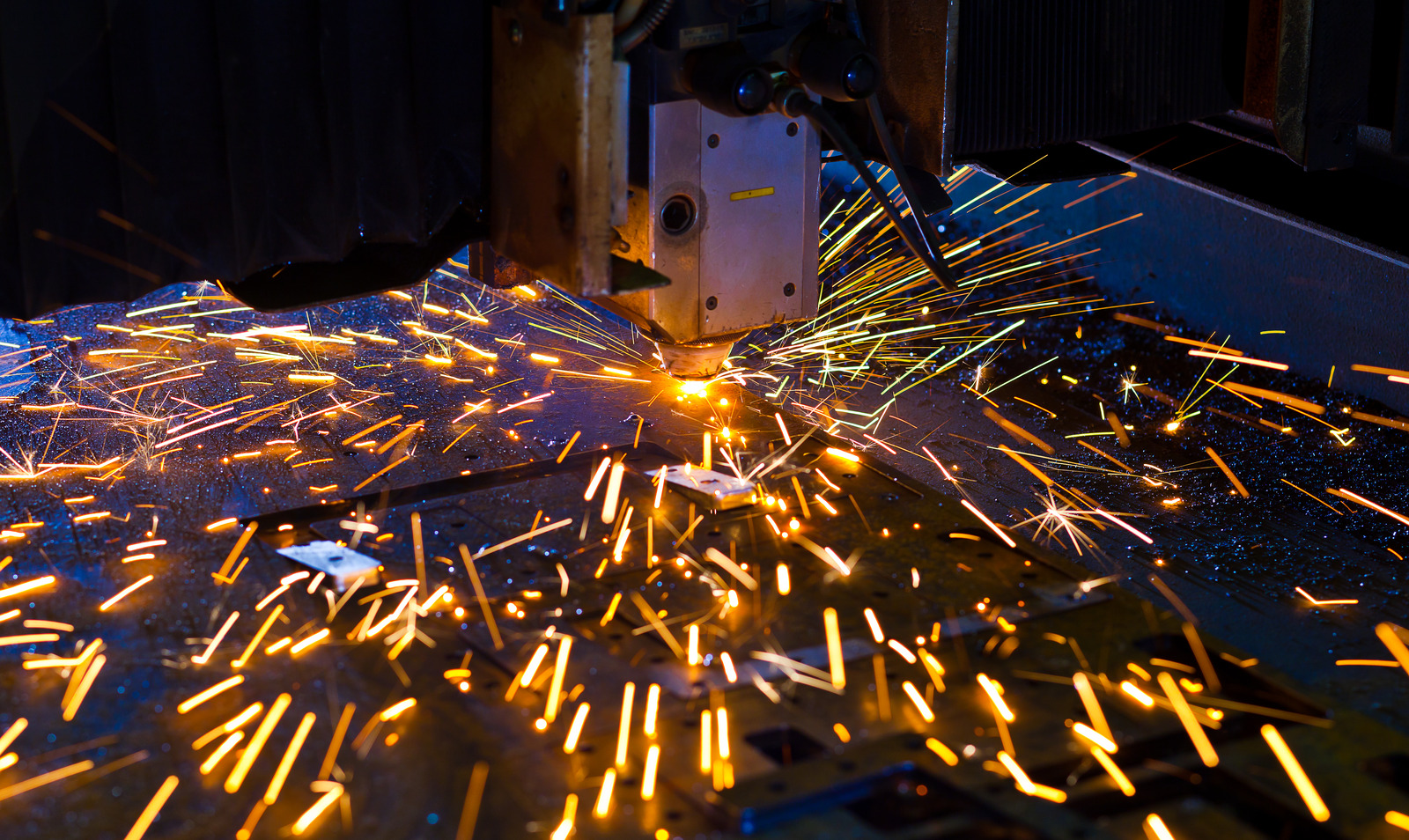
Disadvantages of Laser Cutting in Aluminium Manufacturing
High Initial Costs
other techniques One of the main disadvantages of laser cutting in aluminium manufacturing is the high initial cost. Laser cutters are more limited in the materials they can cut compared to other methods and aluminum is one of the more challenging materials to cut with lasers. Despite this, it is still the most preferred metal for laser cutting due to the accuracy of results and the many advantages associated with this method.
On top of the upfront cost of buying or leasing a laser cutter, operating and maintenance costs need to be taken into account. Since this is one of the more expensive cutting processes, fabricators need to make sure that the parts being made are worth the cost.
High Energy Usage
other types of cutting processes One of the main disadvantages of using laser cutting in aluminum manufacturing is the high energy usage. Laser cutters are a more energy-intensive production process than some of the other processes used in aluminum manufacturing, such as traditional cutting processes or even more modern automated processes such as CNC machines. This is because the laser beam used to cut aluminum is more powerful than the cutting tools used in more conventional methods.
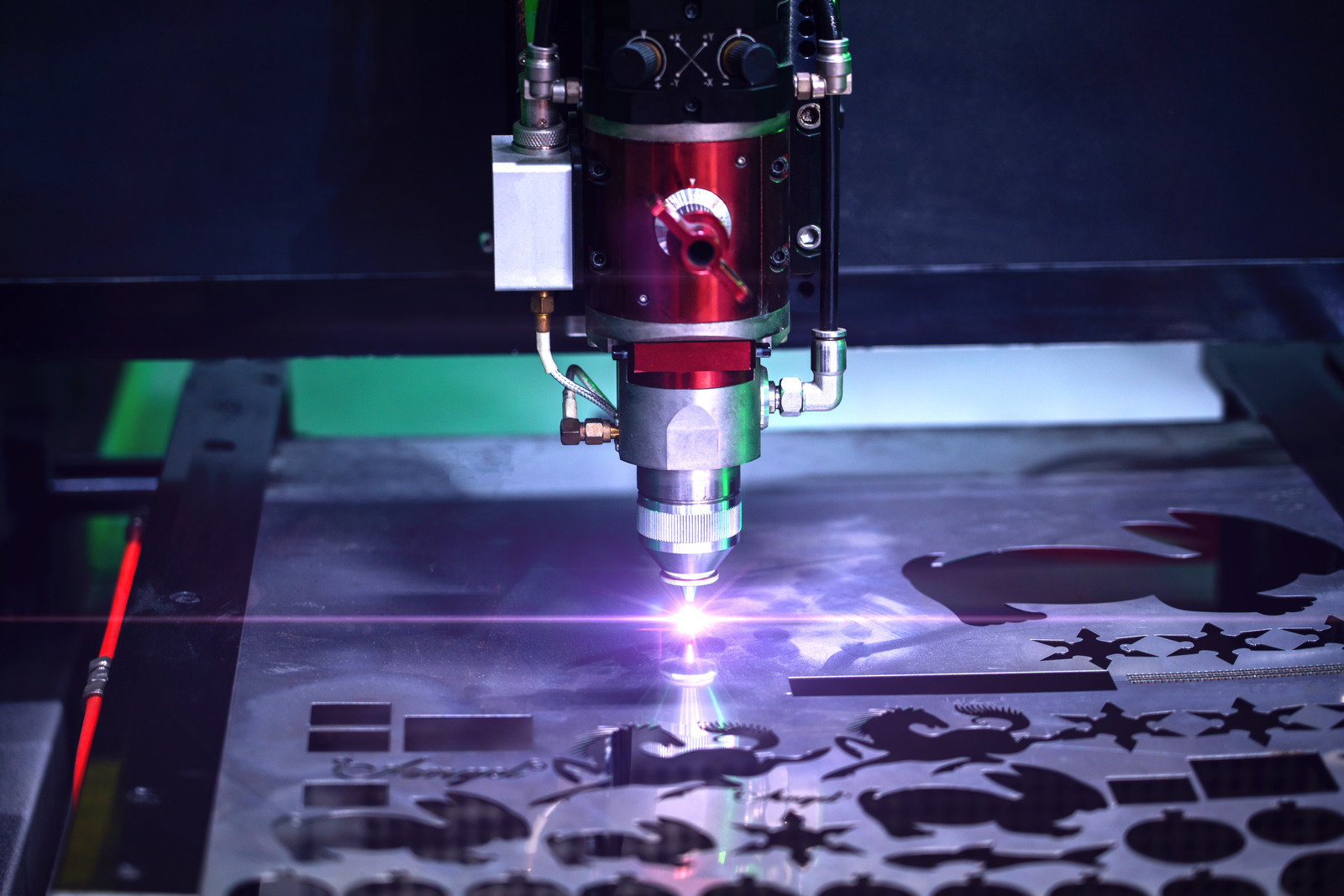
Other Factors to Consider When Comparing Laser Cutting to Other Aluminium Manufacturing Techniques
Specialized Use Cases
traditional methods When it comes to comparing laser cutting with other aluminium manufacturing techniques, specialized use cases must be considered. Laser cutters are more limited in the materials they can cut, but can effectively work with aluminum, making it one of the more challenging materials to work with. Compared to other manufacturing techniques, laser cutting is often the most preferred as it is one of the cutting processes to be able to manufacture in the most precise manner.
Automation of the Process
When it comes to automation of the process, laser cutting is the most efficient and preferred method for the manufacturing of aluminum. Laser cutters are more limited in the materials they can cut, but aluminum is one of the materials laser cutters can effectively work with. Laser cutting is one of the more challenging materials to cut, but it is also one of the most preferred metal to use during the cutting processes.
Laser cutters are a more energy-efficient and faster option for cutting metal compared to other fabrication processes such as sawing and plasma cutting.
Safety Concerns
traditional methods like sawing Safety Concerns: When laser cutting aluminum, there are multiple safety issues to consider. One of the main safety issues is the potential for particles, including metal particles and gas, to escape the cutting area. As aluminum is one of the more challenging materials for laser cutting, most laser cutters are limited in the types of aluminum they can work with.
Additionally, the open environment of a laser cutting area presents potential fire hazards, and the laser cutting process emits fumes and smoke that must be properly ventilated.
What are the advantages and disadvantages of laser cutting?
manual or mechanical cutting When it comes to aluminum fabrication, laser cutting is one of the most preferred metal cutting processes. This process is made even more efficient thanks to modern laser cutters, which are often more energy-efficient and faster compared to manual or mechanical cutting processes. One of the main advantages of laser cutting aluminum is that it can effectively work with one of the more challenging materials to cut.
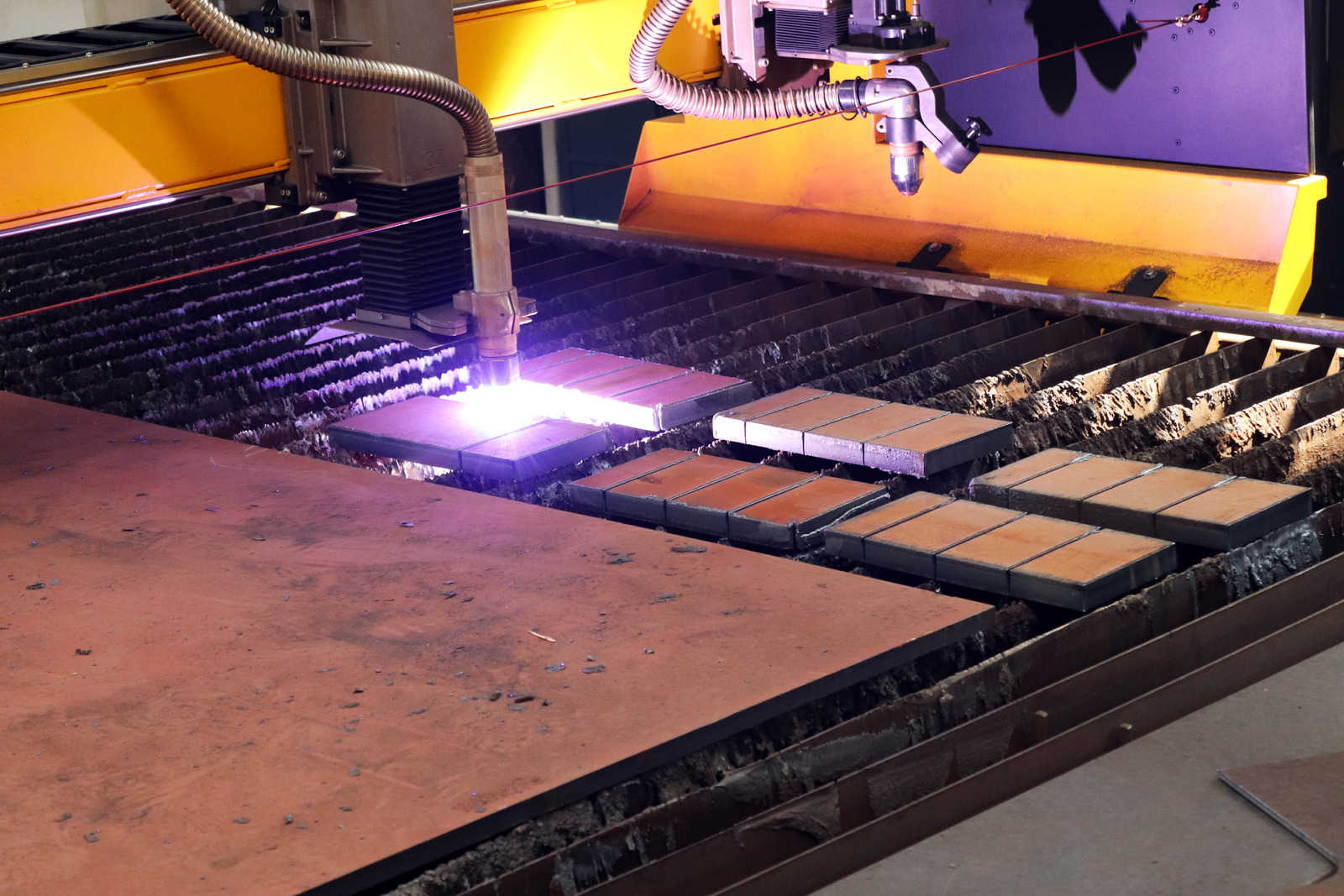
Why is a laser cutter an efficient method of manufacturing?
traditional methods Using a laser cutter to manufacture aluminum is an efficient and cost-effective method, particularly when compared to other common manufacturing techniques. Laser cutters are capable of cutting a variety of metals, including aluminum, one of the more challenging materials to work with. This makes the process of cutting and fabricating aluminum comparatively easier when using a laser cutter.
When compared to other traditional methods of cutting aluminum such as saws, drills, and shears, laser cutters are a more energy-efficient and faster option for cutting metal. Furthermore, laser cutters provide higher precision and accuracy when cutting aluminum as compared to other methods.
What are four disadvantages using the laser cutter?
many other cutting processes When it comes to laser cutters, there are several disadvantages that should be taken into consideration. Firstly, laser cutters are more limited in the materials they can cut. While they can effectively work with aluminum they are not suited to cutting many other metals.
This limits their range of applications. Secondly, when compared to other metal cutting processes, laser cutters are one of the more challenging materials to work with. This is due to the equipment that is required and the levels of precision that need to be maintained.
As a result, laser cutters require specialized training, and it is not always easy to find trained personnel to perform the work.
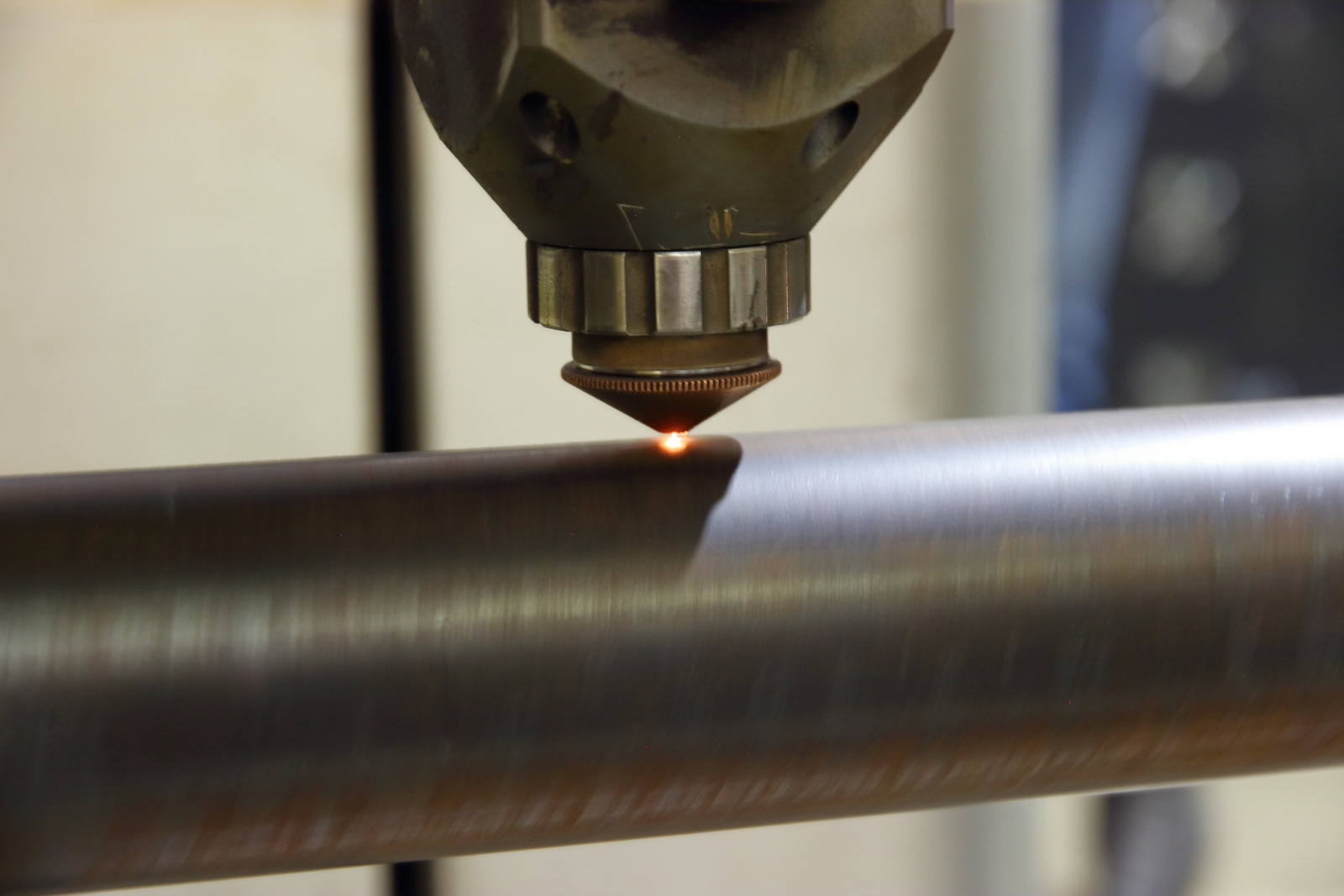
What type of laser can cut aluminum?
other techniques When it comes to laser cutting aluminum, the most preferred metal for this type of cutting is CO2 laser cutters. CO2 laser beams are optimally shaped for cutting metal and can effectively work with aluminum, one of the more challenging materials to cut. While there are other types of lasers available for cutting aluminum, such as fiber lasers and YAG lasers, these are less commonly used for aluminum cutting.
How powerful of a laser to cut aluminum?
other fabrication processes Laser cutting aluminum is a very powerful and precise way to form and shape metal components. It produces accurate and high-quality results with less waste, making it one of the most preferred metal fabrication processes. When it comes to lasers cutting aluminum, the power of the laser used is very important.
Generally, the more powerful the laser, the thicker the aluminum that can be cut through. The power of the laser used will also affect the speed of the process – with a more powerful laser, the cutting process is likely to be faster.
What are 5 advantages of using a laser cutter?
The use of lasers over other manufacturing techniques for aluminum fabrication has many advantages. Firstly, laser cutting aluminum is incredibly precise as lasers precisely cut along designated lines on the material. Second, laser cutting results in reduced machining time per component while using minimal energy, decreasing labor costs and other material wastages. Third, lasers offer great flexibility in terms of designs.
- Precision: Laser cutters offer unparalleled accuracy and detailed cuts for intricate shapes, smooth edges, and nearly any desired pattern.
- Versatility: Aluminium laser cutting allows you to produce both simple and complicated designs quickly and efficiently.
- Cost-Effective: Laser cutting is typically cheaper than other aluminium manufacturing techniques, such as die cutting and stamping.
- Quality: Laser cutting produces superior quality cuts compared to traditional methods.
- Speed: Laser cutters are fast and can quickly produce a wide variety of components.
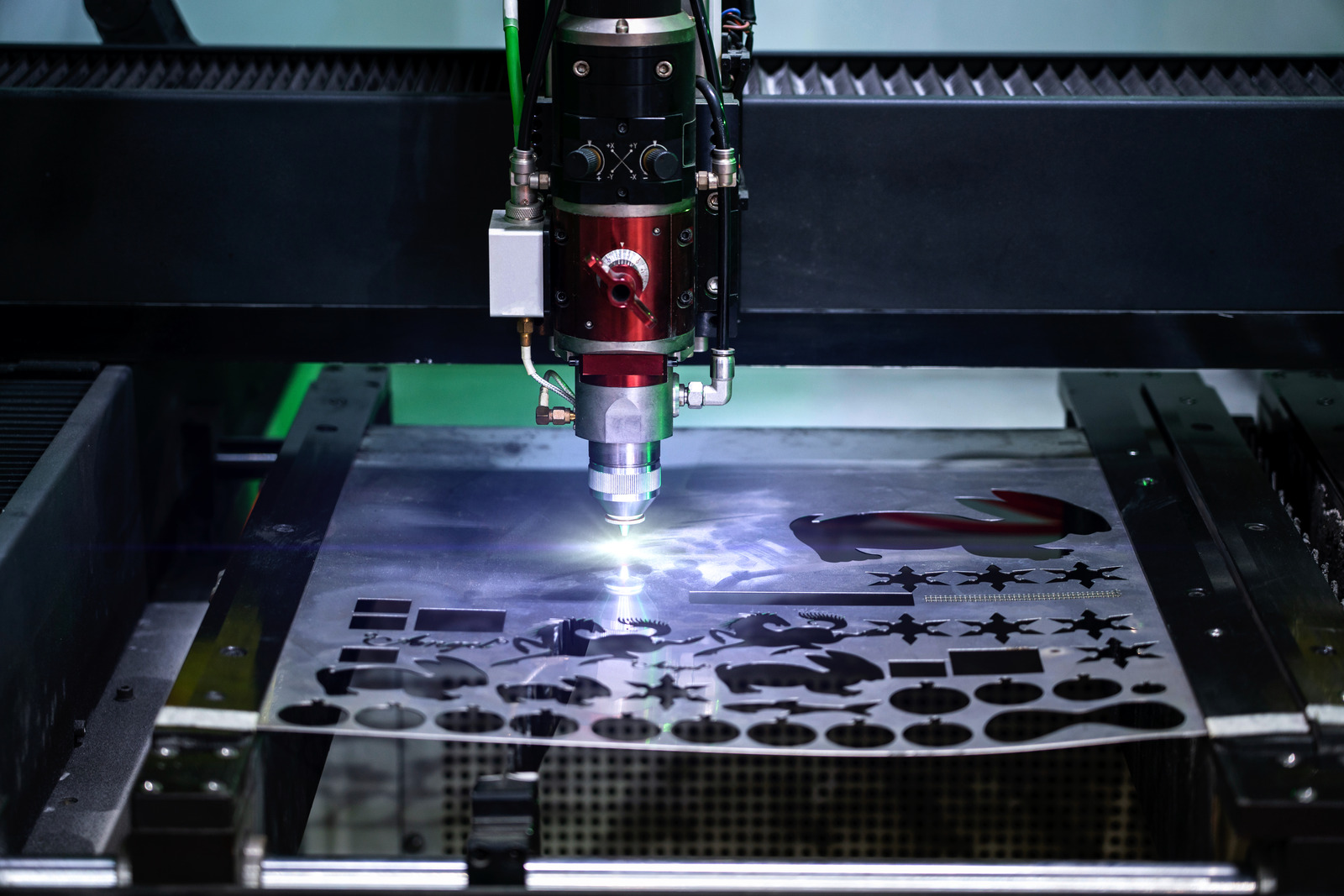
What are two advantages of laser cutting?
other techniques Laser cutting offers a variety of advantages for cutting aluminum. One of the main advantages is the precision of the cuts. Laser cutters have extremely fine-tuned optics that allow for an incredibly precise dimensional accuracy.
Another advantage of laser cutting is that it allows for very intricate contours when cutting the Aluminum. This makes it easier to produce complex shapes and designs quickly and efficiently. Laser cutters are also more limited in the materials they can cut than traditional cutting processes such as punch and shear cutting.
This makes them a great choice for different types of metal, including aluminum, which is one of the more challenging materials to work with.
Conclusion
Summary of Laser Cutting vs Other Aluminium Manufacturing Techniques
other methods Laser cutting is one of the most popular metal fabrication processes for forming aluminum components. It is a highly precise process that uses a powerful laser beam to cut the material, creating intricate shapes and details. Laser cutters are fast, accurate and reliable, and offer superior quality control.
They are also one of the more energy-efficient and faster options for cutting metal compared to other methods. However, laser cutters are limited when it comes to the materials they can cut.
Pros and Cons of Laser Cutting vs Other Aluminium Manufacturing Techniques
other processes When it comes to manufacturing aluminum, laser cutting is one of the most preferred metal fabrication processes. This is primarily because it is one of the most energy-efficient and faster options for cutting metal compared to other processes. Laser cutters are also able to effectively and accurately work with aluminum, one of the more challenging materials to cut compared to other metals.
Final Thoughts and Recommendations
other techniques In conclusion, laser cutting aluminum is one of the more challenging materials to work with, but it has some significant advantages. Laser cutters are a more energy-efficient and faster option for cutting metal compared to other techniques like manual cutting or waterjet cutting. In addition, since laser beams do not require any sort of contact with the metal it reduces the risk of damage and contamination to the finished product.
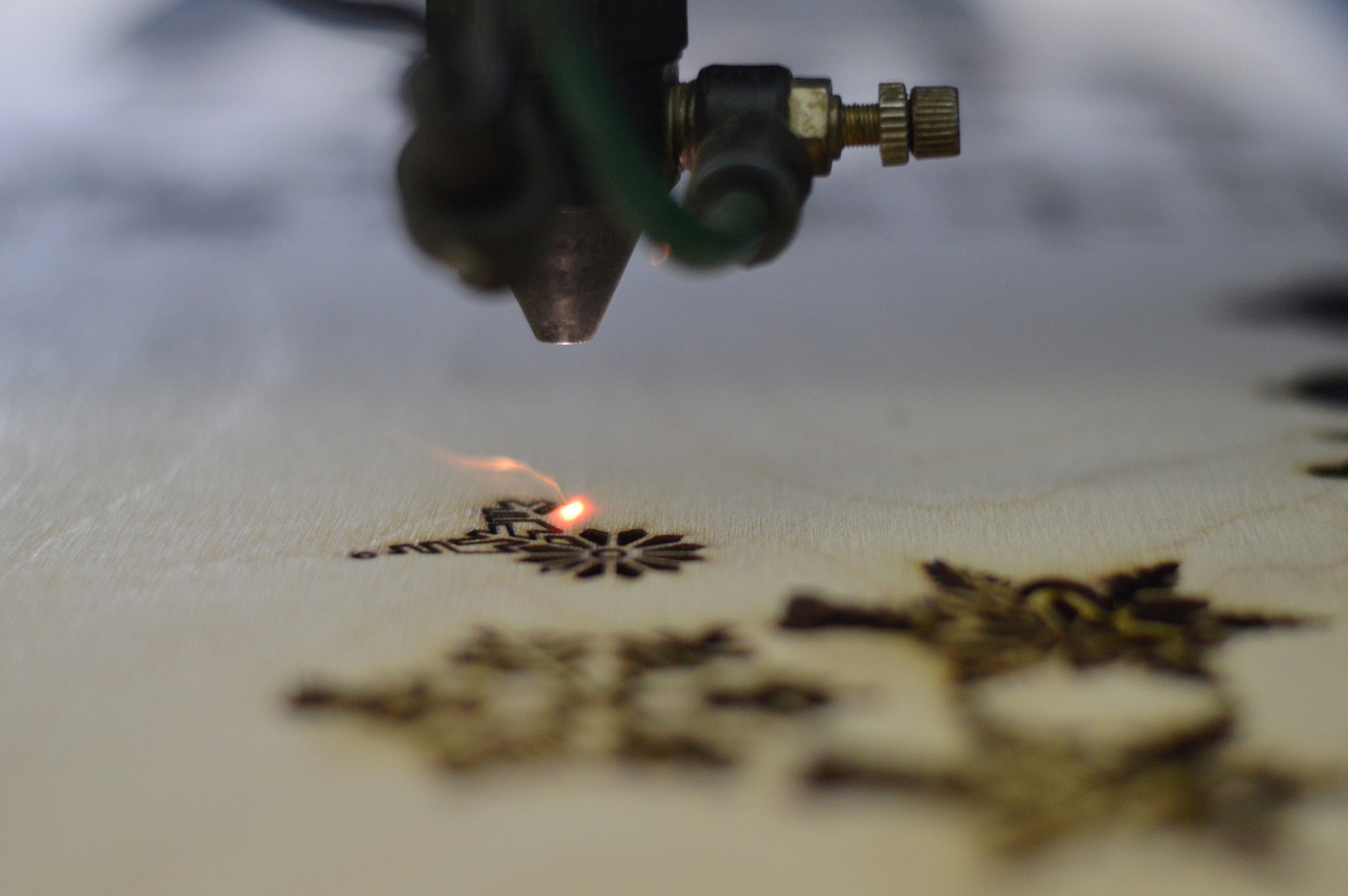