When it comes to laser cutting, precision is key. Quality control standards ensure accurate and repeatable results to end-product specifications. However, establishing effective quality control standards can be a daunting task, and if done incorrectly, it can lead to costly mistakes. In this article, we will discuss the common mistakes to avoid when setting laser cutting quality control standards so that you can ensure the best possible outcomes.
Common Mistakes to Avoid
Not Taking Product Tolerances into Account
One of the common mistakes to avoid when setting laser cutting quality control standards is not taking product tolerances into account. Tolerance is the amount of variation or tolerance allowed in the final product’s dimensions and is decided based on the purpose and quality of the product. Laser cutting quality should take into account the final product’s tolerances in order to ensure the quality of the product remains within the designated range.
Without taking product tolerances into account, the laser cut product’s quality may not meet the desired standards.
Not Establishing a Repeatable Process
One of the most common mistakes to avoid when setting laser cutting quality control standards is not establishing a repeatable process. This is an incredibly important step in ensuring top quality standards are met when using a laser cutting machine. The idea behind creating a repeatable process is that all components are made the same way each time, so that consistent results can be achieved.
Ignoring Thermal Effects
When it comes to setting laser cutting quality control standards, one of the most common mistakes people make is ignoring the thermal effects of the laser cutting process. This is especially important with modern laser cutters, as the process relies on using light to cut materials. The amount of heat generated when the laser beam comes into contact with the substrate can cause significant changes in the material and the manufacturing process, making it essential to take the thermal effects into account when setting up quality standards.
Not Following Regulatory Requirements
When it comes to quality laser cutting, one of the biggest mistakes businesses can make is not following regulatory requirements. In order to develop a successful process and product, businesses must understand and adhere to the guidelines and regulations set by relevant governing bodies. Quality control standards must also be closely monitored to ensure quality laser cutting.
Unfortunately, organizations often neglect to prioritize regulatory requirements and neglect to consider any local or regional laws or regulations. Quality control processes are also too often overlooked for overly complicated setting standards. Businesses should make sure that setting standards are tailored to the specific needs of their specific process and product, as this is crucial for ensuring quality products.
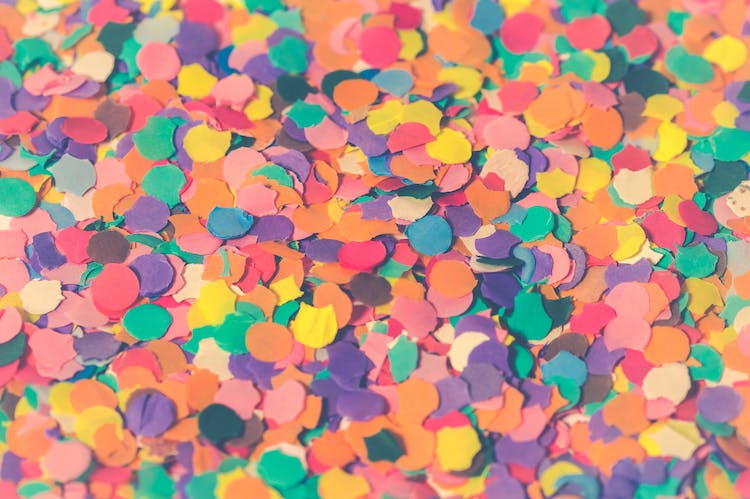
Best Practices for Laser Cutting Quality Control Standards
Establish Clear and Balanced Quality Objectives
When it comes to setting laser cutting quality control standards, one of the biggest mistakes is not establishing clear and balanced quality objectives. It is essential that a set of standards is created which clearly define and differentiate the acceptable limits of quality and fit desired by the end user. While it is important to ensure that the cut quality meets the wishes of the customer, it is also important to make sure that the customer remains realistic in their expectations.
Quality objectives should take into account the desired speed and the cost of laser cutting, ensuring that the laser cutting process is not too slow or expensive that it becomes prohibitive.
Seek Out Automation and Software Solutions
One of the most common mistakes when it comes to setting quality laser cutting standards is relying too heavily on manual processes. It’s important to remember that humans are error-prone and that mistakes can happen with any system. To ensure that you are consistently producing the same quality of product, you should be automating your processes as much as possible.
This can include using industrial cutting software that can determine the correct settings to produce the most precise cuts, as well as automated inspection tools that can monitor your laser cutting procedures.
Utilize Monitoring and Documentation Tools
When it comes to setting laser cutting quality control standards, one of the most common mistakes is to forget about monitoring and documentation tools. Implementing a system for monitoring and documenting the results of your laser cutting processes is one of the best practices for improving and maintaining the quality of your final product. The best way to go about this is to first determine the goals that you want to achieve and the metrics that you want to track.
For example, you might want to track the levels of carbon in the metal, or the consistency of the cuts.
Identify Assignable Causes
When it comes to setting laser cutting quality control standards in any industrial setting, it is important to be aware of and identify the assignable causes of problematic cuts. Knowing what is causing poor cuts can help identify problem areas, and prevent future issues from occurring.
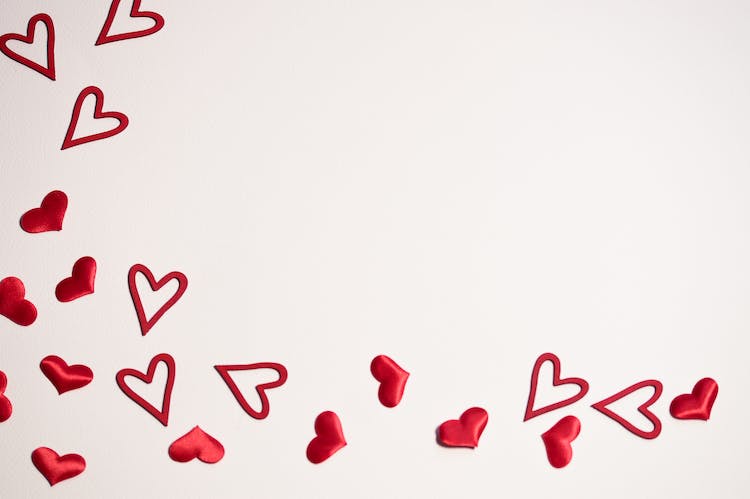
How can I improve my laser cut quality?
Setting laser cutting quality control standards can be a daunting task. It’s important to get it right, as improper settings can cause problems ranging from uneven cutting, poor material utilization, or damaged finished products. To improve your laser cut quality, it is important to identify and avoid the most common mistakes.
One of the biggest mistakes is failing to properly adjust the standard settings to match the specific parameters of the laser cutter. Each laser cutter is slightly different, and the settings need to be tailored to that specific machine. Every component should be calibrated properly, from the laser itself, to the optics and power delivery systems.
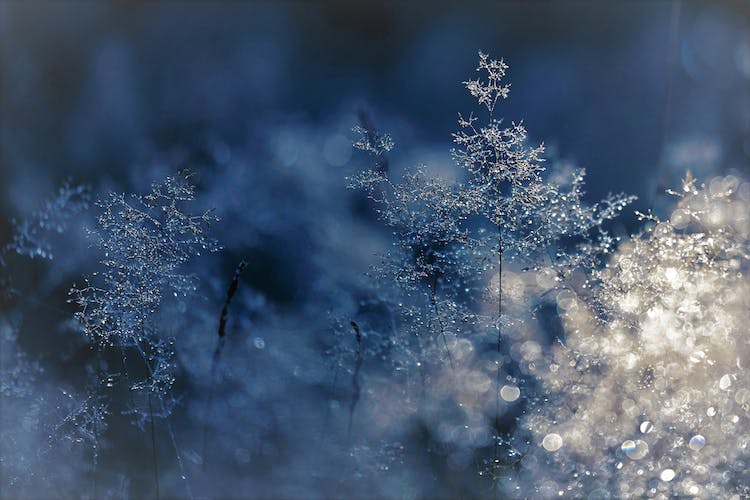
Conclusion
Taking the Right Steps to Ensure Quality Control Standards are Properly Implemented
When it comes to setting quality control standards for laser cutting, there is no one-size-fits-all solution. Every type of laser system, material, and job will require tailored quality control settings, and the biggest mistakes you can make are to neglect the task or try to use shortcuts. Taking the right steps to ensure the quality control standards you set for laser cutting are properly implemented will save time, improve the quality of work, and enhance the overall efficiency of your operations.
Summary of the Benefits of Following Best Practices for Laser Cutting Quality Control Standards
Having quality control standards in place is an essential part of laser cutting that often goes overlooked. Following best practices is a must if you want your finished product to live up to the expectations of your customers. By implementing and adhering to the right laser cutting quality control standards, you’re ensuring the highest level of accuracy and precision, creating repeatable cuts that consistently match your design.
By taking the time to research and set the right standards, you will be able to achieve consistent repeatable results of the highest quality.
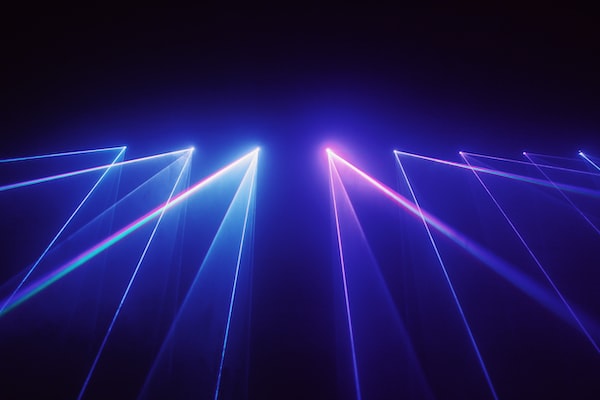