When adjusting the settings for laser cutting, there is a delicate balance between achieving a perfect cut and overloading the machine. With this in mind, it is important to avoid common mistakes when making adjustments to parameters. In this article, we will discuss the most common mistakes to avoid when adjusting parameters for laser cutting and how to use the right settings to achieve an optimal result.
Common Mistakes to Avoid
Adjusting the Power too High or Low
When it comes to laser cutting, one of the most common mistakes you can make is adjusting the power output too high or too low. Power is the total amount of energy delivered from the laser to the material, and the level of power affects the quality of the cut and the speed of the cut. Too much power will cause extra heat, creating burned edges and potentially damaging the laser itself.
Poor Focus of Laser Beam
When adjusting parameters for laser cutting, one of the most common mistakes is poor focus of the laser beam. This means that the beam is either out of line or not the right distance from the material. Poor focus can result in issues such as burned material, overcutting, and weak cut quality.
The best way to ensure proper focus of the laser beam is to use a laser cutter with an adjustable cutting head. These types of laser cutters will have an adjustable cutting head that allows you to adjust the focus of the beam based on the material you’re working with.
Too Much or Too Little Air Pressure
One of the most common mistakes to avoid when adjusting parameters for laser cutting is having too much or too little air pressure. Air pressure is an important factor in laser cutting because it can affect the quality of the cut. Too much air pressure can cause inconsistencies in the cut and can damage the laser lens, while too little air pressure can cause inadequate cutting power.
It’s important to find the correct air pressure for your setup in order to optimize the cutting process.
Inadequate Lubrication
One of the most common mistakes to avoid when adjusting parameters for laser cutting is inadequate lubrication. Cutting with a laser without properly lubricating risks damage to the equipment, including possible overheating and damage to the laser head itself. Proper lubrication also helps to ensure a smooth, clean cut and can help extend the life of cutting tools.
To ensure proper lubrication, you should use a lubricant designed specifically for laser cutting. These lubricants are designed to reduce friction and heat buildup, which helps to minimize damage to the equipment. It’s important to reapply the lubricant regularly to keep it up to date.
Cluttered Cutting Area
When it comes to laser cutting, one of the most common mistakes is having a cluttered cutting area. This is because laser cutters need room to work and any extra materials, tools, or obstructions can obstruct the laser’s path and negatively impact the accuracy and precision of the cut. Additionally, clutter can block the laser’s view, which can lead to inaccurate results.
The best way to avoid this common mistake is to plan ahead and ensure your cutting area is clean and free of debris or other materials. Additionally, it’s important to keep the area clear of any smoke or gas, as this can interfere with the laser’s sensitive optics.
Tips for Adjusting Parameters Successfully
Begin with a Experimental Test Piece
When it comes to adjusting parameters for laser cutting, one of the most common mistakes to avoid is failing to start with an experimental test piece. Without an experimental piece, you risk ruining your final project due to incorrect settings. By doing an initial experiment with a test piece, you can get a feel for how your laser’s settings will affect the quality and cut of your final product.
To create an experiment piece, start by selecting materials that are similar to the materials you’ll be using for your final project.
Make Small Adjustments at a Time
When it comes to laser cutting, it’s important to remember that small tweaks can make all the difference. Adjusting parameters isn’t something that happens overnight, and shouldn’t be done hastily. It’s important to make “small” adjustments that will bring your project closer to perfect.
Not every tweak will be a “multiplier effect” improvement, but oftentimes, years of experience gives insight in how to lead up to a desired outcome. As with any creative process, there will be trial, error and adaptation with laser cutting and engraving. When adjusting parameters for a specific laser cutting project, it’s recommended to make small changes at a time.
Monitor Resulting Materials
Monitoring the resulting materials from laser cutting is paramount to ensuring successful results in laser cutting projects. This means making sure that the materials have been cut correctly and also that you have reached the desired thickness and tolerance levels. To monitor the results, it is recommended to inspect the cut parts to look for inconsistencies or potential defects.
Also, it is helpful to take measurements of the parts to make sure they meet the desired specifications. When adjusting the laser parameters, you want to be sure to make small adjustments rather than large ones. Small adjustments will allow you to track how the changes affect the cut parts.
Which of the following is not suitable for a laser cutter?
When adjusting parameters for laser cutting, it is important to know which material is suitable for laser cutting and which is not. Laser engraving is not suitable for laser cutting. It’s tempting to substitute laser engraving for laser cutting, but doing so will almost certainly result in a ruined piece of material.
The reason laser engraving is not ideal for trying to achieve a laser cutting effect is because a laser engraver only creates etchings into the surface of a material, while a laser cutter can make precise and clean cuts into several different types of materials.
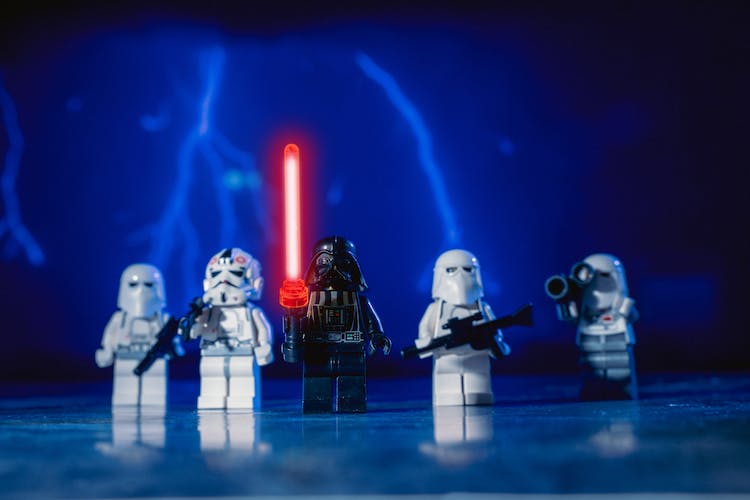
Conclusion
Summary
In conclusion, when it comes to laser cutting, it is important to remember the common mistakes to avoid in order to produce the best possible results. It’s all about setting the right parameters for the type of material, thickness, method, and power level of the laser to ensure an accurate and efficient cut.
Takeaway Message
The main takeaway message when it comes to adjusting parameters for laser cutting is that you should always pay close attention to the details. It’s easy to get caught up in the excitement of getting something done quickly, but in the end, taking the time to properly adjust the parameters will pay off with a better finish and lower risk of damage or mistakes. It’s essential to properly research the type of material you are using, take extra care in adjusting the power, speed, focus, and other settings to make sure they are appropriate for your project.
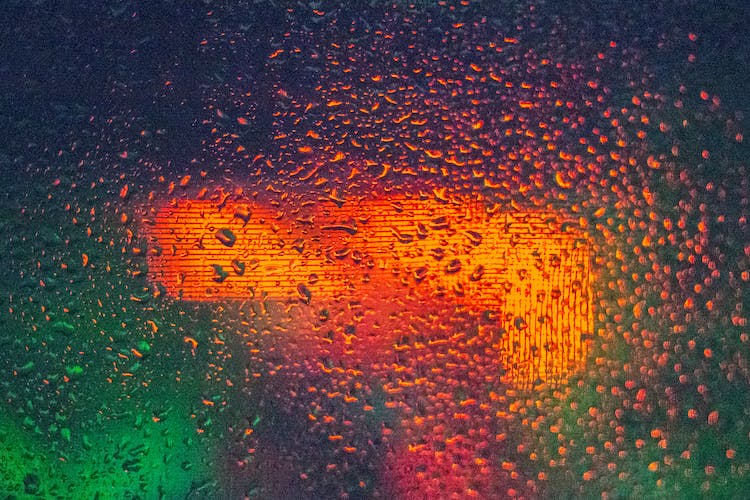