Welcome to this exploration of how laser cutting kerf affects detail in fabrication. This topic is critically important for anyone involved in fabrication, manufacturing, and design, as any minute inaccuracy in the cutting process can lead to costly and time-consuming delays. Through this investigation, we will gain a better understanding of the effects of laser cutting kerf on the precision of detail in fabrication.
Effects of Laser Cutting Kerf on Detail in Fabrication
Minimal and Precise Detail
detail When it comes to creating intricate detail in projects and fabrications, laser cutting technology is often the best choice. Laser cutting provides accuracy, consistency and precision that is unparalleled in other fabrication methods. Laser cutting is often preferred for creating high-quality cuts with minimal kerf (the width of the cut) and precise detail.
Kerf is the width of the slot left behind after the cutting process is completed. In industrial laser applications, the kerf can be optimized to produce the desired cut thickness, width and shape while still keeping the material intact.
Possibility of Warping and Delamination
Kerf One aspect of laser cutting that impacts detail in production is the phenomenon known as kerf. Kerf is the width of material removed in the process of laser cutting and is often referred to as a “burn line” in the material. While the width of the kerf varies depending on the level of detail needed in the item being laser cut, it is typically narrow, usually ranging from just over 0.2mm to a few millimeters wide.
Choosing the Proper Kerf Width
Factors to Consider
When it comes to fabrication, laser cutting offers a unique way to create detailed pieces with precision. This process is widely used in many industries, from automotive and aerospace to jewellery and apparel. One of the main factors to consider is the kerf width.
The kerf width of a laser cut is the size of the gap formed between the two parts of the material being cut. Choosing the right kerf width is essential to ensure that your finished product will meet your quality and detail expectations. Generally speaking, the narrower the kerf width, the more details you can achieve.
Pros and Cons of Wide or Narrow Kerf Width
The kerf width in laser cutting affects the detail of your fabrication work, and requires careful consideration when using a laser cutter – that is, you should consider the pros and cons of a wide or narrow kerf width when planning your project. There are a few pros to choosing a wide kerf width when cutting fabrications with a laser cutter. First and foremost, a wide kerf width will reduce your cutting time immensely, as the laser cutter will be able to cut through material more quickly.
This, in turn, can save you money since you will be able to cut through more material in less time.
Examples of Laser Cutting Kerf in Fabrication
Fabrics and Textiles
fabric When it comes to fabrication, one of the most important aspects of the process is the detail you can achieve with your materials. This is where laser cutting comes in. Laser cutting is an efficient and precise way to cut fabric, allowing you to achieve intricate and detailed designs.
Laser technology works by using a beam of light that is precisely focused to precisely cut the material. There is one factor, however, that affects the level of detail you can achieve with your fabric when using laser cutting: kerf width.
Metal Components
metal When it comes to fabricating metal components, laser cutting is a popular and efficient method for cutting intricate shapes out of metal parts. Laser cutting is a process that uses high- powered lasers to heat metal, which causes it to melt and vaporize away, allowing for metal components to be cut to precise specifications.
What effects the width of the cutting kerf in sheet metal cutting?
When it comes to making intricate design details in sheet metal fabrication, the width of the cutting kerf is an important factor to take into consideration. The kerf is the width of the slit or groove that is left behind in the metal once the laser cutting process is complete. The width of the kerf affects the accuracy, precision, and detail of the finished product.
The width of the laser cutting kerf is determined by a number of factors, the most important being the power of the laser, the type of material being cut, and the speed of the cut.
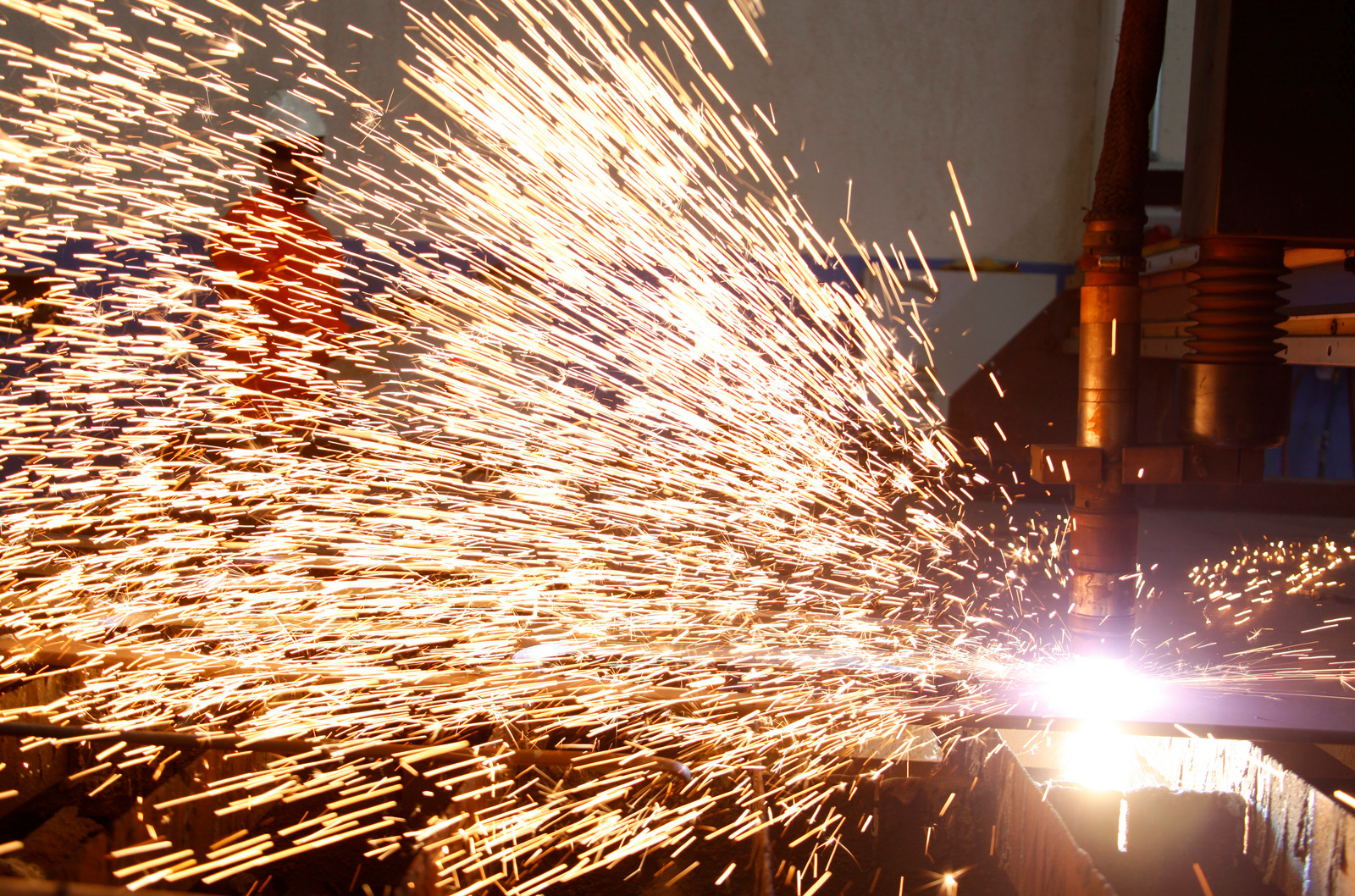
What is laser kerf and why is it important?
Laser cutting is a method of precision cutting of metal, plastic, or other material using a powerful directed heat or light source. It is one of the most precise and efficient methods for cutting material and is used in industrial settings for a variety of purposes. Laser cutting introduces very little stress to the material being cut, making it an ideal choice for delicate or intricate cuts.
Kerf is the width of material removed when cutting with a laser beam.
What factors affect the width of the kerf?
When it comes to laser cutting, the width of the resulting kerf (the area of melted or burned material that is removed from the workpiece or material) can vary depending on a number of different factors. The width of the kerf can be affected by the size of the laser beam, the speed of the laser, the cutting definition, the material type, and the power of the laser. The size of the laser beam plays a major role in determining the width of the kerf.
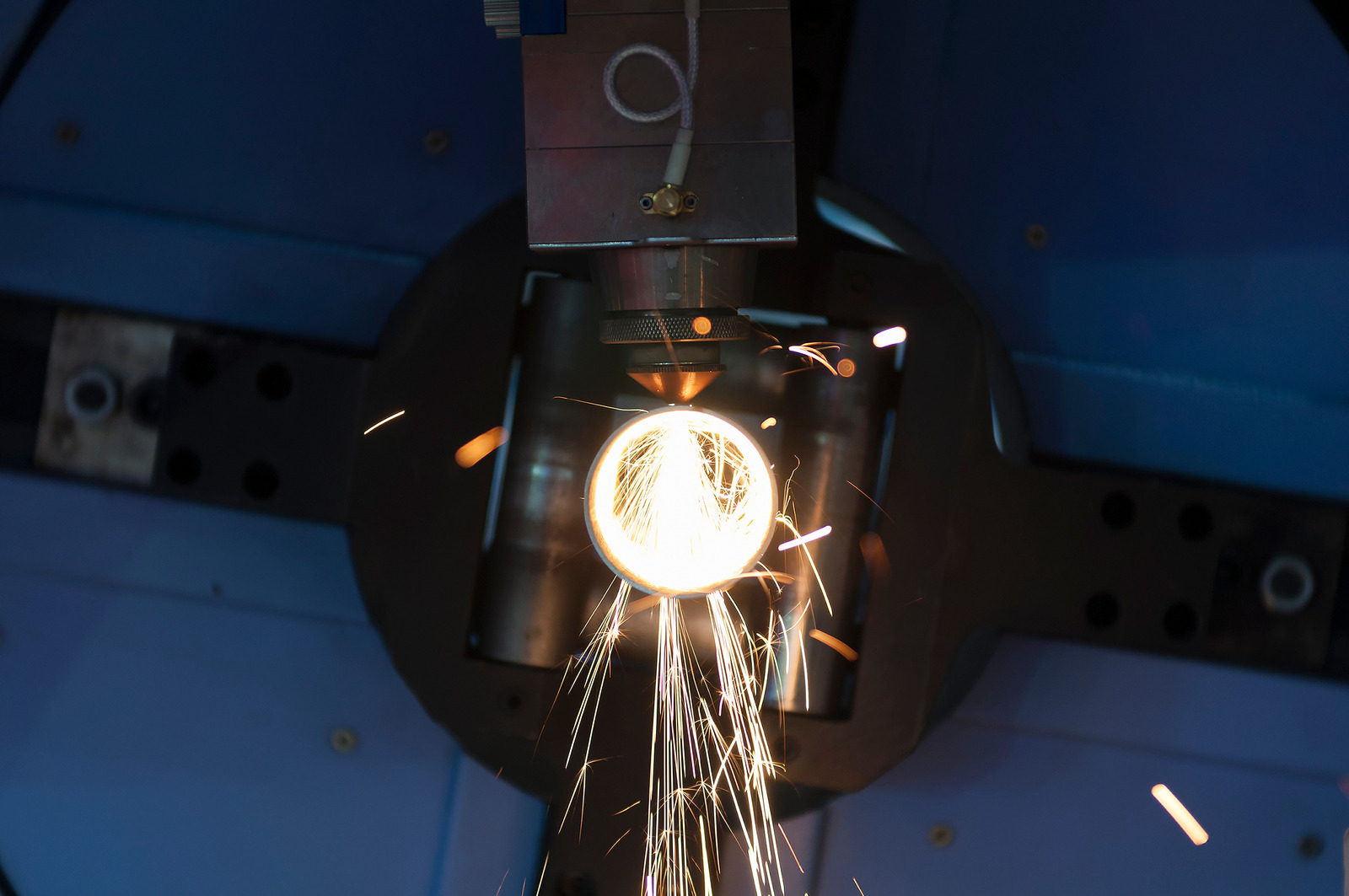
How do you account for KERF in laser cutting?
ters When it comes to laser cutting, one of the most important concepts to understand is KERF, or “Kerf Width.” KERF is the width of the cut made by the beam of the laser in a material. When it comes to designing and manufacturing products, engineers must consider the KERF of the laser cutter that is being used to accurately account for the material that has been cut out of the product during the fabrication process.
By taking the KERF of the laser cutter into account, engineers are able to create designs that will minimize the amount of material wasted due to incorrect cut size.
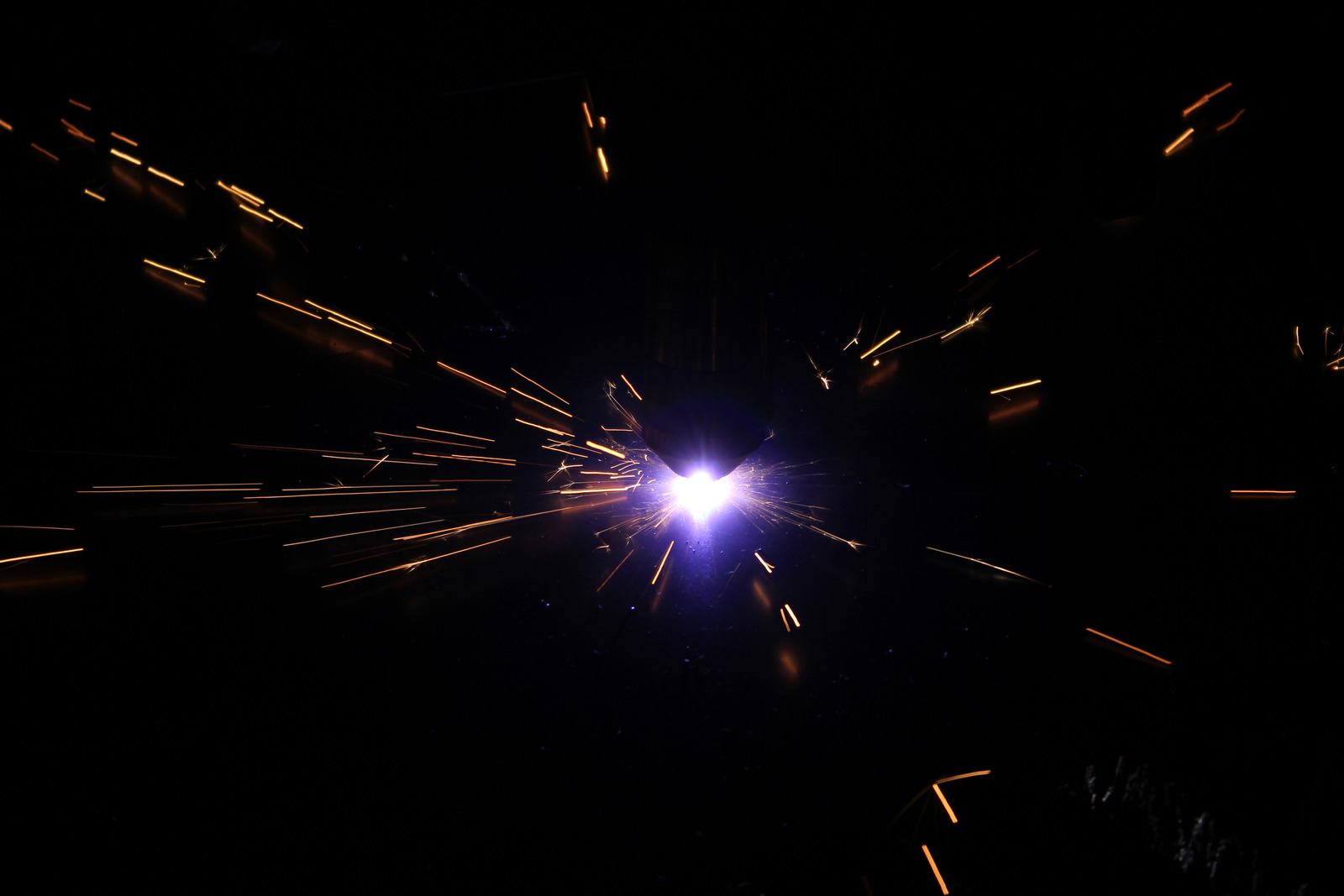
Conclusion
Benefits of Laser Cutting Kerf
Laser cutting is a popular fabrication technique that uses a focused beam of light to burn through a variety of materials. One advantage of laser cutting is its ability to produce intricate designs with a very small kerf, or cutting line. A kerf is the space between two cuts and is typically only a few times more than the beam width.
For certain applications, the width of the kerf can affect the accuracy and detail of the part.
Challenges of Laser Cutting Kerf
When it comes to laser cutting, the kerf (width of cut) of the material being cut can present some challenges. The kerf is determined by the power used to cut the material, and when the kerf is too wide, the detail of the design can be compromised. The power used for cutting affects the width of the kerf, and if the power is too high, then the kerf can be too wide for some materials.
To ensure that the desired level of detail is achieved, it’s important to understand the power settings and adjust accordingly. That said, when it comes to precision cutting, there are a few other challenges to consider.