If you’re working with laser cutting for HDPE (High Density Polyethylene) you need to make sure that you have a good set up process to ensure the best quality and safety. In this article, we’ll cover the various steps and processes needed to properly and optimally set up your laser cutting process for HDPE material. We’ll discuss the importance of choosing the right laser, the right cutting speed, and other considerations such as pre-heating the material and the use of exhaust systems.
Preparing Your Laser Cutter for Cutting HDPE
Setting up your machine for optimal cutting of HDPE
When setting up your laser cutter to cut HDPE, the key is to create your perfect process. Start your setup by calibrating the laser output to the material thickness. Different machine settings are available to manage the power, speed, and focus of the laser beam.
Finding the best settings for the material will require some trial and error. Once you’ve determined the ideal power and speed, the beam needs to be set for the proper focus.
Selecting the correct laser and power settings
When it comes to setting up your laser cutter to cut HDPE, the first and most important step is selecting the right laser cutter. Many different models of laser cutters are available on the market and with a variety of capabilities, so it’s important to select one that correctly meets your needs. When selecting a laser, start your research by considering the types of projects you plan to do, the size of the material you need to cut, and the level of accuracy required.
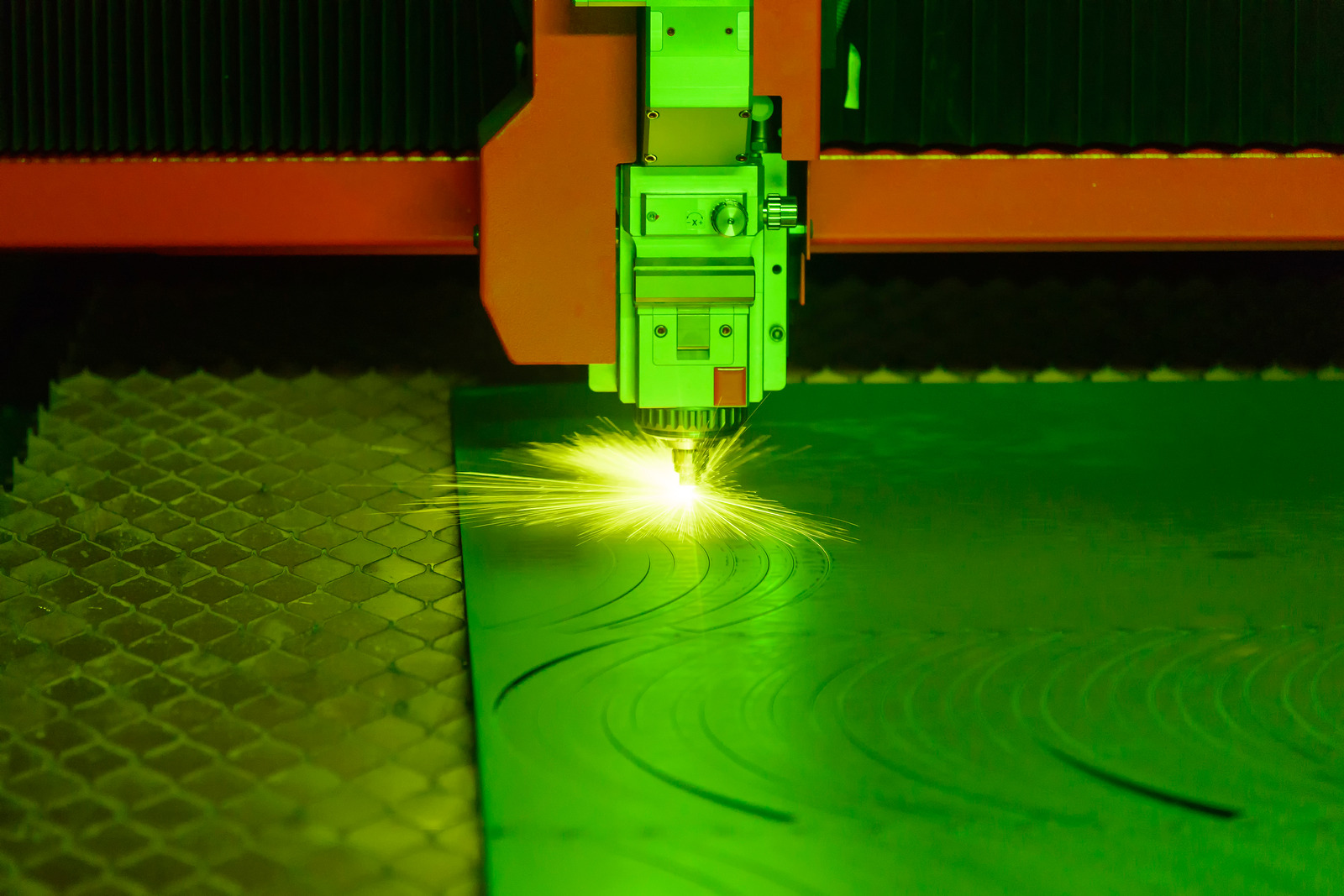
Optimizing Workflow for HDPE
Pre-processing data to prepare for laser cutting
Before you can begin laser cutting HDPE, you need to preprocess the data. This process is an essential part of setting up an optimally efficient laser cutting workflow. Creating your laser cutting path is the starting point in producing quality HDPE products.
The best cutting path for HDPE is one that efficiently utilizes your laser cutter capabilities and maximizes the time you spend on cutting.
Setting up the correct part orientation to improve cutting quality
When it comes to laser cutting HDPE, one of the most important components of the process is setting up the part orientation correctly. To ensure optimal cutting quality, it is essential to take the time to create your setup correctly. The best way to start your setup is by using a program that is tailored for laser cutting.
This will give you a basic guide for setting up the part orientation, as well as provide a template that you can use for the laser cutter. Make sure to use a fully adjustable laser cutting table to get complete control over the cutting process.
Troubleshooting Common Problems
Reducing charring and distortion to maximize finish quality
When it comes to laser cutting HDPE materials, the proper set-up of your laser cutting process can be the difference between a perfect cut with minimal charring and distortion, and an uneven cut with tons of charring and burned edges. To start your process off on the right foot, it’s important to take a few preliminaries into account. First, consider the power of the laser you’re using.
Identifying the source and causes of laser cutting issues
When you are setting up your laser cutting process for HDPE, identifying the source and source of issues can be a difficult task. The first step is to create your laser cutter setup. This means having the correct power output, lens focal length, gas mixture, and cutting speed.
Once your laser cutter setup is configured correctly, you can start your laser cutting process for HDPE. When it comes to troubleshooting laser cutting issues, the best approach is to investigate each component of the laser cutting process.
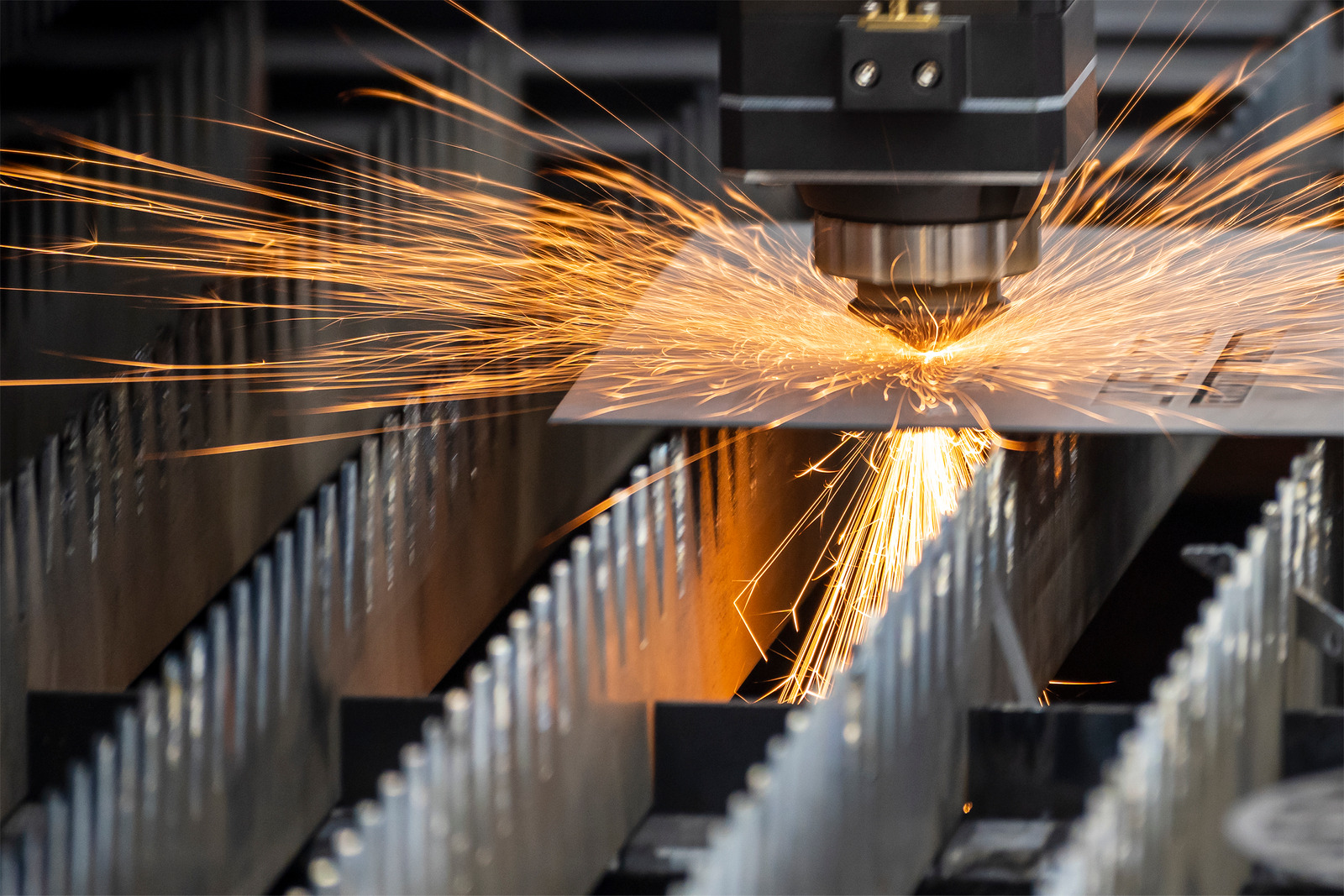
Can you cut HDPE with a laser?
Absolutely! High-density polyethylene (HDPE) is a heavy-duty plastic that is resistant to a variety of chemical compounds and is easily cut with a laser cutter. If you’re looking to start your own laser cutting process for HDPE, it’s important to understand the optimal settings for your laser cutter to ensure you get the best results for each cut.
At the core of any laser cutting process is the laser cutter itself.
Conclusion
Summary and review of the laser cutting process for HDPE
Creating your own laser cutting process for HDPE can be a daunting task, so it’s important to understand the resources you’ll need and the steps you should take to ensure optimal performance. In this blog post, we reviewed the basics of laser cutting and discussed the best practices for setting up a laser cutting process for HDPE. To start your process, you’ll need the right type of laser cutter as it will be the primary tool that drives the process.
Tips and ideas for future experiments and improvements in the process
Optimally setting up your laser cutting process for HDPE is a necessary step to ensure a successful and cost-efficient production process. To do this, it is important to configure the laser parameters correctly and match the process settings according to material thickness, required precision, and speed.
- Use a slow and steady cutting speed to reduce the heat generated and therefore the friction and wear of the tool. Ensure the nozzle is fitted correctly to prevent any uneven cutting and jointing of the material. Increase the flow of oxygen to assist the cutting of the HDPE material, allowing the product to cool down during cutting. Ensure the working area is adequately lit and that the operators can safely monitor the entire area while working. Add extra steps during the process such as cool-down time and regular clean-up of the machine, this helps to ensure long term efficiency.