Welcome to this tutorial on the basics of making gaskets with laser cut rubber! In this guide we will discuss the essential tools and materials needed for this task, as well as provide an overview of the process. Laser cut rubber gaskets are often used for industrial applications, as they are more efficient and cost-effective than traditional methods. We’ll also provide some tips on troubleshooting and common pitfalls to look out for. By the end of this guide, you’ll have a better understanding of the basics of laser cut rubber gaskets and be ready to start working on your own projects. So, let’s get started!
A Step-by-Step Guide
Choosing a rubber material
Making gaskets with laser cut rubber is a great way to ensure precise and intricate shapes and sizes. This can offer you the ability to create effective, flexible and water-resistant gaskets that suit your exact needs. To ensure success, there are a few basics steps to follow. Firstly, decide what material to use and how thick it needs to be.
- Research the specific demands and abrasion resistance of your particular product. Knowing the application will help you choose the right rubber material for your gaskets.
- Look for rubber materials that are certified and known to leading industry standards and guidelines.
- Ask your supplier if they can supply a sample of the gasket so you can test the product yourself.
- Take into consideration things like temperature and pressure range when selecting a rubber material.
- Consider getting a quotation from an experienced laser cutting service in order to ensure the highest quality of manufacturing.
Designing the gasket pattern
Designing the gasket pattern for laser cutting is not always straightforward. In order to get the best results for your project, you’ll need to be familiar with the design specifications for the type of rubber you are using, as well as the laser cutting system you’ll be using. To begin, you will need to decide on what size and shape the gasket will be.
The size needs to take into consideration how large the laser cutting machine will be able to process. Knowing this, you can then measure out the exact dimensions that would be most suitable.
Programming the laser cutting machine
When it comes to making gaskets with laser cut rubber, the first step is to program the laser cutting machine. Programming a laser cutter involves setting certain parameters such as the type of laser, the size and shape of the gasket, and the amount of cutting power required. The laser cutter must also be calibrated correctly to ensure accurate cuts and to avoid burning or melting the rubber.
Cutting the rubber
Making gaskets with laser cut rubber requires precise attention to detail and an efficient method of cutting the rubber to fit a specific purpose. The use of a laser cutter is the common choice for producing consistent and accurate cuts in rubber, and the process involves a few steps to ensure the gasket is properly prepared for use. The first step in cutting the rubber is to measure the surface area of where it will go and cut a piece of rubber that size.
Depending on the laser cutter being used, this process may need to be done manually or with a cutting template specific for the particular type of laser cutter. This template will help ensure the most accurate cut possible in the rubber.
Installing the finished gasket
Once the laser cut rubber gasket has been completed, the installation process is relatively straightforward. Depending on the size and shape of the gasket, you’ll need to take a few measures to make sure the installation is successful. First, make sure that the gasket is well-adapted for the space intended for it.
Measure the thickness and size to ensure that the gasket fits properly. If the gasket is too large, use a pair of scissors to adjust the size and shape. Make sure you don’t cut too much – the better the fit the better the seal.
Benefits of Laser Cut Rubber Gaskets
Tighter seals
When constructing any type of machinery, it is important to have properly fitting gaskets to ensure that the parts fit together with no leakage or problems. To create gaskets, one must cut out small pieces of rubber that have been customized to perfectly fit the machinery. This can be a tedious and time consuming process.
However, using a laser cutter simplifies and speeds up this process.
Superior longevity
Laser cutting is a great option for creating high-quality gaskets with rubber that offer superior longevity. Lasers are able to precisely cut intricate shapes and patterns with excellent accuracy, allowing for a variety of designs that traditional cutting methods can’t match. Furthermore, lasers emit high amounts of heat without causing any damage to the rubber material, unlike traditional cutting methods that can cause burnt or fraying edges.
Improved precision
When it comes to making gaskets, precision is key – this is why laser cut rubber gaskets are so popular. Laser cutters can deliver superior accuracy and repeatability compared to using other methods like die-cutting. With a laser cutter, you can cut gaskets to a uniform size and shape without worrying about warping, jagged edges, or other inconsistencies.
The high level of precision you can achieve with laser cut rubber gaskets lets you get a perfect fit, time and time again.
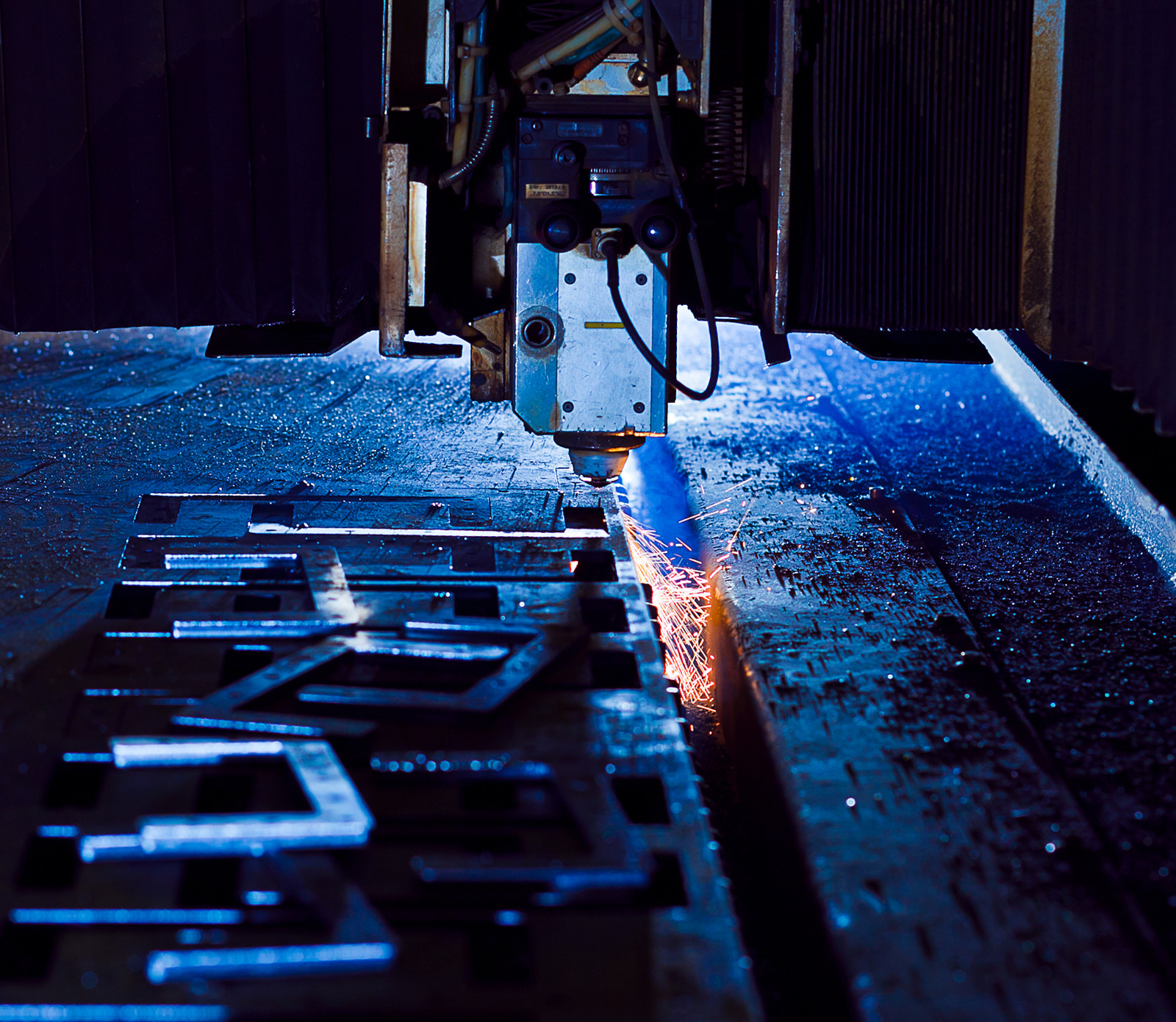
How do you cut a rubber gasket?
Making gaskets with a laser cutter is becoming increasingly popular as a manufacturing method. Laser cutting rubber is a fairly quick and accurate way to create any type of gasket. The process begins by selecting the proper rubber material that will match your application’s specifications.
After preparing the rubber material, the laser cutting system is loaded and the cut parameters are established according to the rubber material and the applied application. During gasket laser cutting, a precisely focused laser beam is used to cut and shape the rubber. The laser beam is finely controlled and able to cut intricate areas with ease.
What can you use to make a rubber gasket?
One of the most versatile techniques for fabricating rubber gaskets is laser cutting. Laser cutting is a rapid, precise method of cutting materials into a desired design. It uses a focused laser beam to cut through materials such as rubber, vinyl, and other flexible material.
Using a laser cutter, you can customize rubber gaskets to fit your needs. You can create complex shapes with just one laser cut, which means you don’t need complicated molds or manual labor. The process of creating the gasket is often much faster and more accurate than traditional methods.
To create a gasket, you must first have a design prepared that corresponds to the shape of your gasket.
Can you laser cut rubber gasket?
Yes, you can laser cut rubber gaskets! Laser cut rubber gaskets offer superior accuracy and flexibility in comparison to some of the counterpart technologies. The laser cutting process is the perfect solution for a reliable and extremely precise rubber gasket.
It is more efficient and cost-effective than mechanical cutting devices. First, you must identify the right type of rubber that is most suitable for laser cutting.
Conclusion
Summary of topic
This blog section provides a summary of the basics about making gaskets using a laser cutter. Laser cut rubber is an efficient way to create gaskets for a range of applications, from automotive to industrial and more. It is an economical approach to forming rubber gaskets and gasket assemblies because, unlike traditional methods, laser cut rubber gaskets can be cut in just a few minutes versus hours.
Final thoughts on the process
The process of making gaskets with laser cut rubber is a versatile and effective way to create the exact shape and size you need for specific projects or applications. It’s a relatively straightforward process, one which requires quite a bit of precision and attentiveness to ensure the results are of the highest quality. It is important to be sure to account for any possible imperfections that could occur when using a laser cutter for cutting rubber gaskets.
Suggestions for further exploration
Making gaskets with laser cut rubber is a reliable and efficient process for creating components of various shapes and sizes with precise detail. The first step in the process involves creating an accurate and detailed design with a CAD program. This design can then be converted into a file to be cut on a laser cutter with rubber and other material.
- Look into different approaches to designing and cutting rubber gaskets, such as water jet cutting, die cutting, and hand-cut methods.
- Consider additional materials to use for your gaskets, such as different types of foam, rubber, and plastic.
- To extend the life of the gaskets, consider using a protective coating or treatment when the gasket design is finalized.
- Explore different techniques for attaching gaskets to the surfaces they are intended for, such as adhesives, fasteners and clamps.
- Investigate other uses for laser-cut rubber gaskets, such as creating custom-shaped rubber stamps, packaging, and even toys and art.
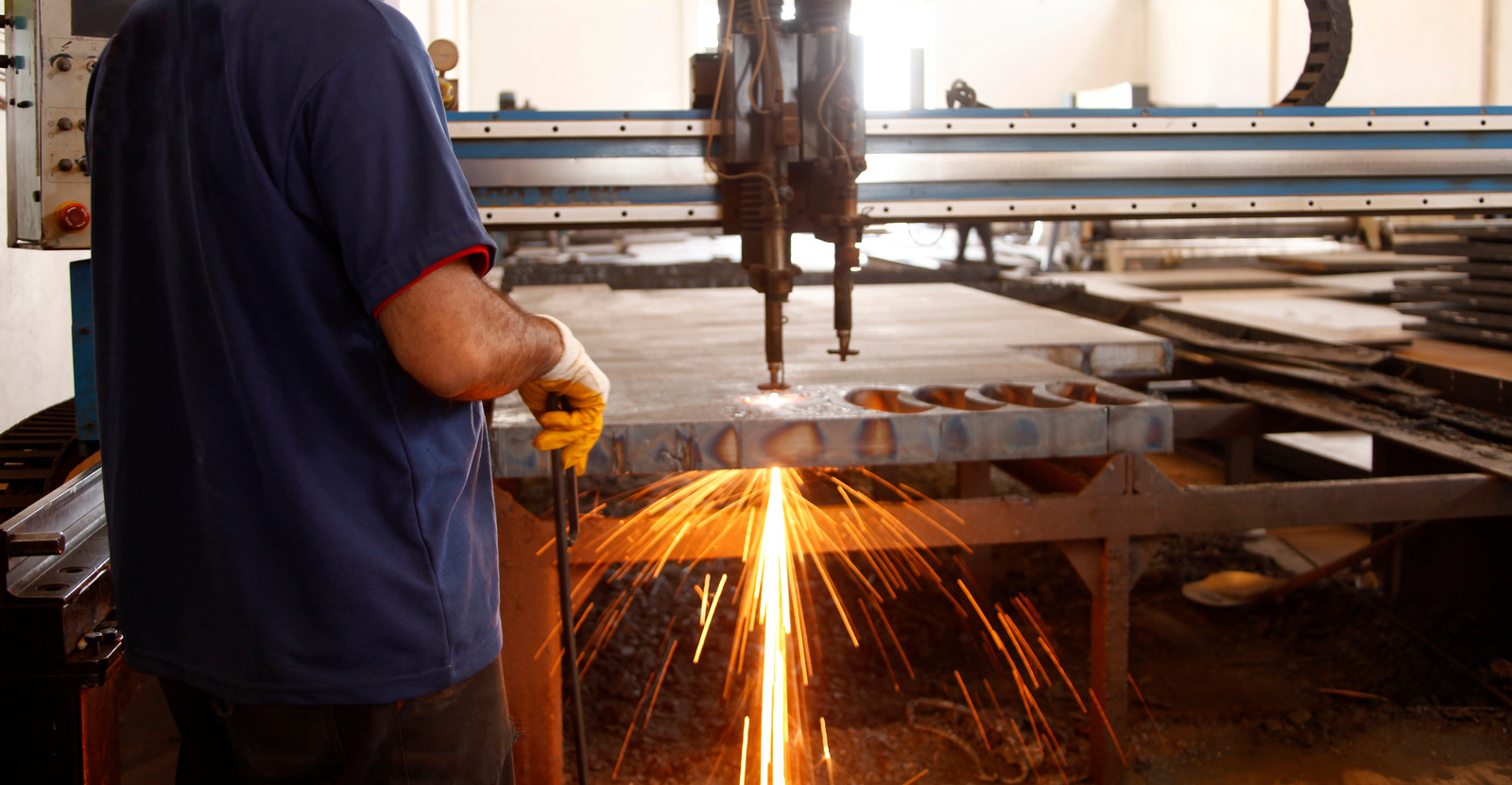