Cutting materials for industrial and fabrication purposes is a widespread application across various industries. Traditional methods used for cutting materials are often associated with emission of hazardous particles and a hazardous working environment. On the other hand, technology has enabled the development of laser cutting which has proven to be a much more efficient, safe, and precise technique utilized in cutting. This article will discuss the advantages and disadvantages of laser cutting in comparison to conventional techniques.
Pros of Laser Cutting
Faster production times
One of the biggest advantages of using a laser cutter for production is that it allows for faster production times, as compared to other more traditional methods – such as die-cutting or routing. Laser cutters are able to quickly and accurately create intricate shapes, as well as cut and etch materials with a high degree of precision. This allows for faster production times as there is no need to manually measure or trim materials, or to reset the machine consistently.
However, it’s important to note that laser cutters can be quite expensive compared to other methods.
Lower energy costs
When discussing the pros and cons of laser cutting compared to traditional methods, a major benefit of laser cutting is its lower energy costs. This is because laser cutters use less energy as compared to traditional cutting methods, such as metal cutting saws that run on electricity or air. Additionally, laser cutters have a much higher accuracy than traditional methods.
This means that you’ll get significantly more accurate cuts with a laser cutter than with a metal cutting saw, resulting in less waste and higher efficiency. Another pro of laser cutting is the speed–most lasers can cut through materials rapidly and accurately, meaning less time wasted manually cutting materials with traditional methods.
More precise and accurate cuts
One of the primary advantages of laser cutting over traditional methods is its more precise and accurate cuts. Compared to manual cutting which is limited to the skill of the cutter, a laser cutter is able to make much more precise cuts with a much higher degree of accuracy. This level of accuracy is especially necessary for high-precision materials, such as metals, where even the smallest imperfections can affect the efficacy of the cut piece.
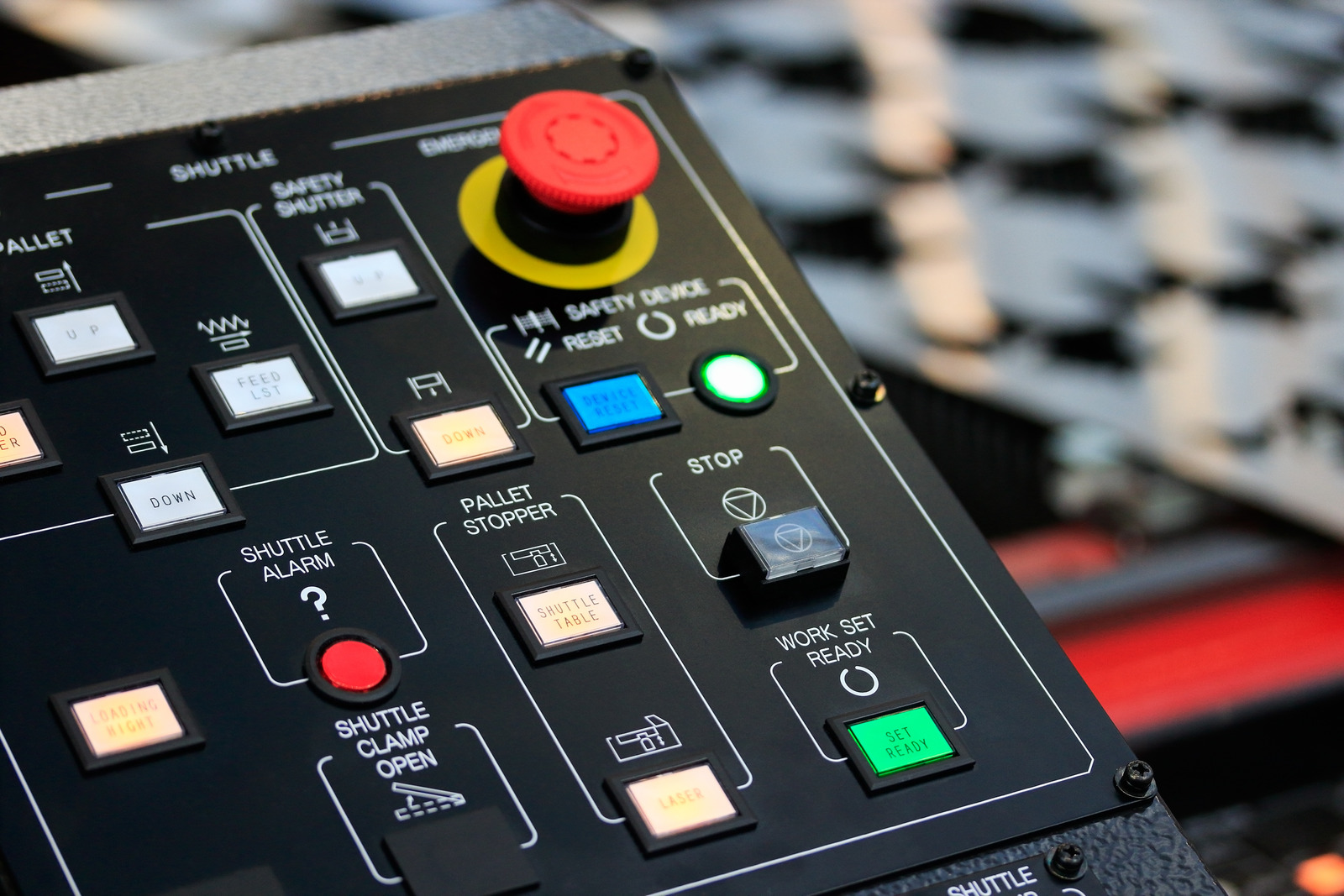
Cons of Laser Cutting
High initial investment costs
When comparing laser cutting to traditional methods, one of the biggest cons of laser cutting is the high initial investment costs. Laser cutters can be quite expensive due to the amount of technology needed for the machine. Not only do you need to buy the laser cutter itself, but you are also typically looking at purchasing safety gear and materials for making the actual cuts.
This can quickly add up and make it cost prohibitive for some businesses or individuals to invest in a laser cutting machine. When compared to traditional methods such as those that rely on hand tools like saws, the initial start-up costs are much lower.
Requires specific materials to cut
When comparing laser cutting to traditional methods, one of the main drawbacks of laser cutting is that it typically requires specific materials to cut accurately. Laser cutters typically cut thin and flat materials well, but thicker materials are more difficult to cut and require higher power densities to be successful. In order to ensure that a laser cutter can cut a certain material, manufacturers must provide recommendations.
Limited ability to cut thicker materials
When weighing the pros and cons of laser cutting versus traditional methods, one key disadvantage associated with laser cutters is the limited ability to cut thicker materials like steel and aluminum. While the laser beam used in a laser cutter can focus up to a very small area, the power of the beam will disperse over larger materials. This means that thicker materials cannot absorb sufficient amounts of energy to cut through more than very thin layers of material.
This disadvantage of laser cutting could limit the use of laser cutters for some applications, as other methods such as waterjet cutting would be better suited for projects that require thicker materials.
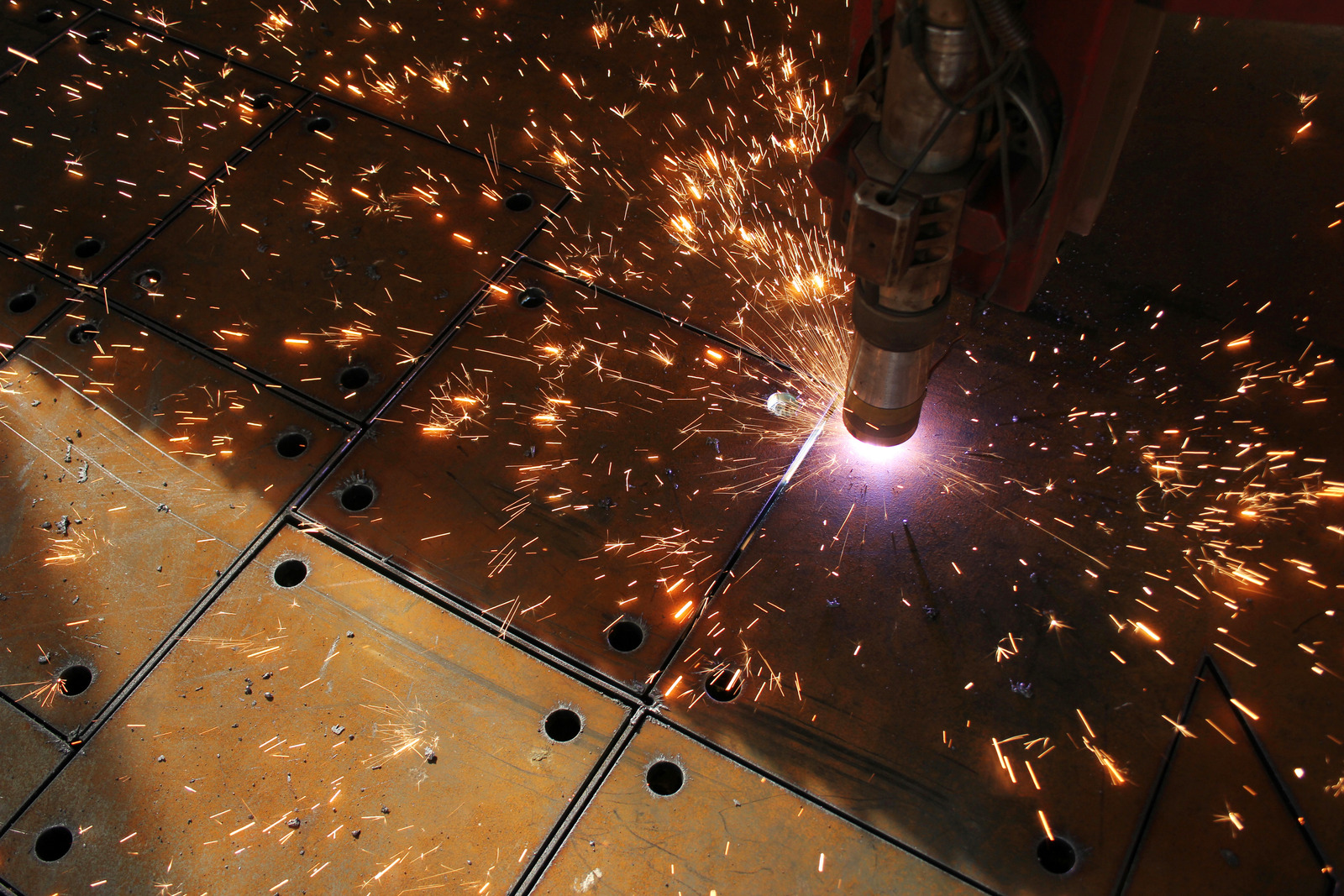
Traditional Machining Methods
Definition of traditional machining
Traditional machining is a form of manufacturing that uses cutting tools to shape and remove material from a workpiece. This process involves measuring and drilling holes, machining surfaces, cutting grooves and other details, and using lathes and other tools to accomplish the desired results. It is typically used for creating parts for industrial applications, such as automotive, aerospace, and medical equipment.
Advantages of traditional machining include its precision, accuracy, cost-effectiveness, and minimal environmental impact. On the other hand, the process can be labor-intensive and time-consuming.
Traditional machining advantages
Comparing laser cutting to traditional machining methods is important when considering what materials to use for a particular task. Traditional machining methods have been used for centuries, but laser cutting has emerged in recent decades as a more precise and efficient alternative.
- The benefit of using traditional machining method is that it allows for more precise and intricate cuts as compared to laser cutting.
- It is possible to mass-produce components exactly to the same specifications and features without any variations.
- Traditional machining processes can be used to produce components of any shape or size using different cutting tools.
- With the help of traditional machining, you can achieve a wide range of surface finishes, such as grinding and polishing.
- Traditional machining processes are economical and require less energy than laser cutting.
Traditional machining cons
When it comes to technology-driven processes for producing parts and components for a range of industrial uses, laser cutting is taking the world by storm. This process is incredibly efficient and versatile, but it doesn’t necessarily replace traditional machining methods. Let’s take a deeper look at the pros and cons of traditional machining methods in comparison to the power of a laser cutter.
Traditional machining has a number of cons that make it less attractive than laser cutting.

Comparing Laser Cutting and Machining
Price
When it comes to price, it’s important to consider pros and cons of laser cutting compared to more traditional methods. When it comes to cost, laser cutters can be quite expensive up front, and require significant maintenance, especially compared to more conventional machining. This can quickly add up in terms of cost.
Precision
When it comes to precision, laser cutting has the clear advantage over traditional methods. Laser cutters use a small, focused laser beam to precisely cut through materials with a very high degree of accuracy. This means that the finish cuts are extremely precise and consistent, as the laser beam will always produce cuts of exactly the same shape and size.
In addition, laser cutters can produce much more intricate and complex designs than traditional methods, as the laser beam can reach into tight corners and precisely cut very intricate shapes.
Speed
When it comes to speed, laser cutting has a clear advantage over traditional methods. Laser cutters are much faster than traditional methods such as saws, milling machines, or routers. With laser cutters, you can cut multiple shapes and sizes in a much shorter amount of time.
Laser cutters can work faster and more accurately than traditional methods and can even be programmed to make complex cuts with no heating, distortion, or manual labor. One downside to choosing laser cutting over traditional methods is that it requires more time to set up and changeover jobs.
Versatility
When it comes to the versatility of laser cutting, there are both pros and cons to consider. On one hand, the laser cutter can be used to accurately and quickly cut intricate shapes, as well as be used for engraving and marking metal or other materials. Additionally, with a laser cutter it is much easier to scale out a design for multiple items quickly and with much greater precision than in traditional machining.
On the other hand, the laser cutter does have some drawbacks. Items cut with laser cutters often require post-production processing or finishing to remove the heat and flame residue the laser cutter creates.
Conclusion
Review of advantages and disadvantages of laser cutting compared to traditional machining methods
vs traditional machining Pros of Laser Cutting One of the biggest advantages of laser cutting when compared to traditional machining methods is its level of accuracy. Laser beam cutting is significantly more precise than most traditional machining techniques- allowing for much tighter tolerances. The laser beam maintains a consistent intensity level, ensuring a consistent cut with no variation.
Another benefit of laser cutting is its increased efficiency. Lasers can provide significantly higher cutting speeds than traditional methods, as well as increase the accuracy of the cut. Depending on the application, laser cutting can also have a much higher material yield than traditional machining.
Finally, laser cutters provide a much safer working environment than traditional machining.
Impact of technology on modern production methods
Technology has made a huge impact on modern production methods. One of the most important examples of this is the use of laser cutters in manufacturing and prototyping. Laser cutters are used to create precise cuts in a variety of materials, from plastic to steel.
They are often used to create intricate designs or to trim down different parts. When compared to traditional methods, laser cutting technology offers clear advantages. It is incredibly precise, able to produce complex designs with a fraction of the time taken by traditional methods.
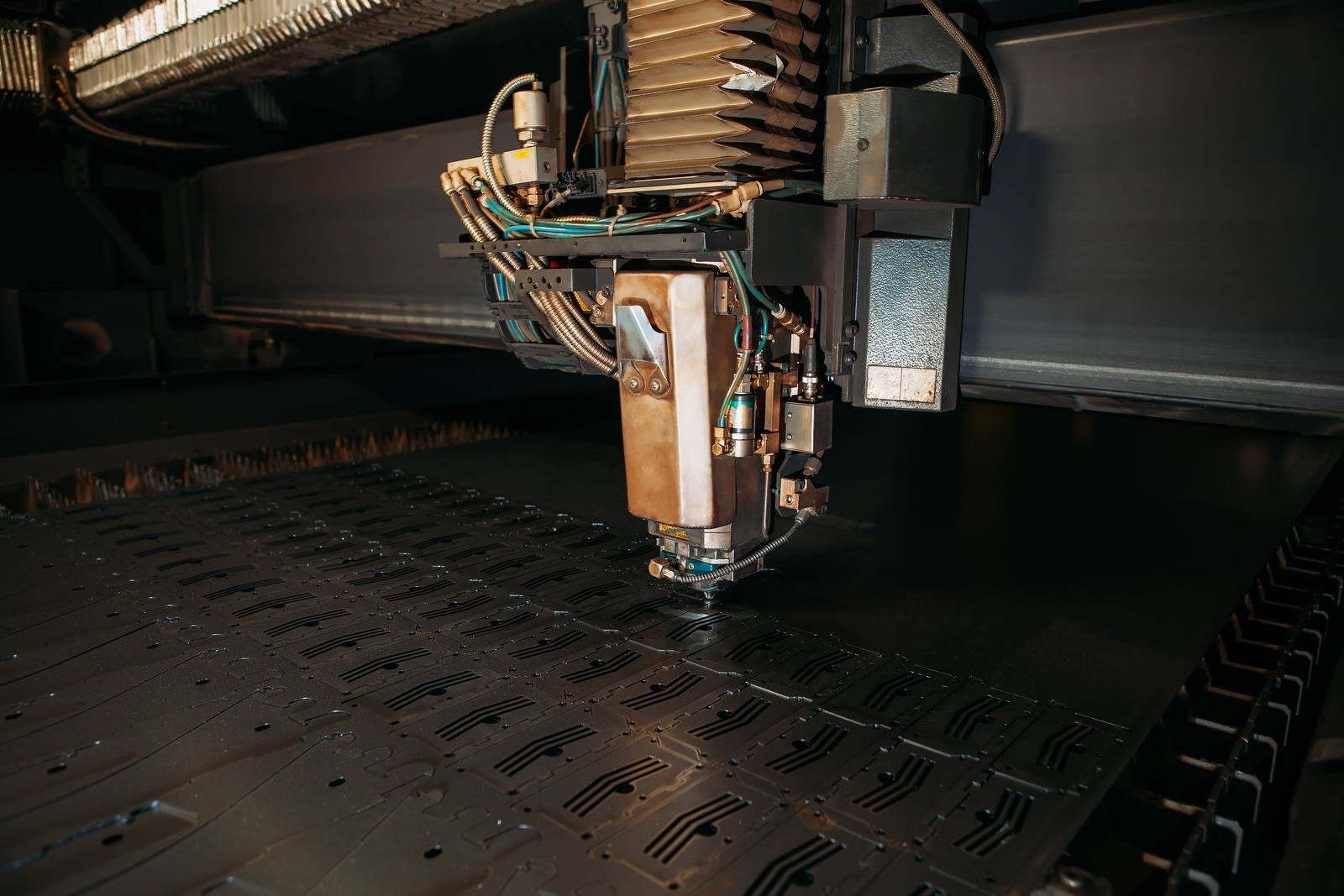