Laser cutting has revolutionized the development and production of a wide variety of products. It is an incredibly precise process, but there are still ways to further refine the quality of your laser cutting. In this article, we will explore some effective tips for improving the overall quality and accuracy of your laser cutting projects.
Causes of Poor Laser Cutting Quality
Imperfect cutting settings
When it comes to laser cutting, quality is crucial for success. To maximize the quality of your outputs, it’s important to understand the causes and sources of poor laser cutting quality and address them with effective solutions. Issues such as incorrect cutting settings including incorrect power, speed, or pulse frequency, improper beam alignment and focus, rough edge quality, and varying or inconsistent material thickness can all cause poor laser cutting quality.
- Use the correct cutting power: Cutting power should be adjusted according to the material type, thickness and familiarity with material. Too much or too little power can negatively impact results.
- Use appropriate speed: For the best results, speed should not exceed the rate that allows for complete melting and vaporization of material. Slow and steady is the way to go.
- Ensure focus is accurate: Focus should remain constant from the start of the cutting to the end. Otherwise, the cut quality will be inconsistent.
- Feedstock should be correctly aligned and clamped: Disparity between the cutting head and the material can cause uneven edges.
- Select the proper optics: Depending on the type of cut and material, certain optics must be used in order to obtain the best results. Different optics work better for different applications.
Poor material selection
Quality Poor material selection is one of the biggest causes of poor laser cutting quality. Choosing the right material for your project is incredibly important to ensure that you get the best results possible. This means taking into consideration the type of laser you’re using, the thickness of the material (including how dispersible it is from the laser), and how the material shapes up under stress.
When selecting materials for your project, you’ll want to ensure the heat conductivity is compatible with the laser.
Dirty/contaminated components
quality One effective tip for improving laser cutting quality is making sure that all the components used in the cutting process are clean and free of contamination. Contaminated or dirty parts can cause a number of issues that lead to poor laser cutting quality. This is because particles on the surface of the part can interfere with the clean cut that the laser produces, and can even cause some parts of the laser cutting to be trapped within the part.
To clean the parts, it’s important to utilize the appropriate cleaning agent for the part materials. For example, parts composed of aluminum or copper can benefit from using a degreasing chemical.
Techniques for Optimizing Laser Cutting Quality
Adjusting beam focus
Quality One of the most important steps for optimizing the quality of laser cutting is adjusting the beam focus. Generally, the optimum focus for a laser cutting system will depend on the laser’s spot size and the thickness of the material being cut. By changing the focus of the laser, you can change both the speed and the quality of the cut.
When cutting thicker materials, the laser beam should be focused at a point that is slightly below the material surface in order to improve the cutting speed.
Optimizing parameters
When it comes to optimizing the quality of laser cutting, numerous parameters must be taken into account. Increasing the power of laser, improving the cutting speed, minimizing the kerf width, maintaining the focus position and minimizing the defocusing are some of the parameters that directly influence the cutting quality. It is important to adjust the laser power to the level that enables the optimization of the cutting speed and the kerf width.
This helps in improving the cutting quality without consuming too much of the laser power. With higher power levels, the speeds are faster, resulting in improved-quality cuts, but with higher levels of power also comes higher kerf width, which can result in poorer-quality cuts.
Utilizing accurate material sizes
Optimizing laser cutting quality is key to any efficient and successful project. One of the most effective ways to do this is by utilizing the right material sizes. Accurate material sizing is critical when it comes to laser cutting, as it ensures that the material is the right thickness and size for the laser to properly and effectively cut it, without wasting time and money due to cutting errors.
When selecting the right material size, be sure to take into consideration the type of laser cutter that will be used in the process, as well as the material’s properties. Thickness of the material should also be taken into consideration, as it will affect the cutting speed, accuracy, and depth of cut.
Introducing cutting aids
Quality Introducing cutting aids is an effective way of increasing the laser cutting quality. Aids can be added to the cutting process, such as gas assist nozzles, lenses, and mirrors, in order to optimize cutting. These aids help improve the outcome of the process by assisting with the cutting process and providing a smoother, more precise cut.
Gas assist nozzles help to enhance the cutting process by creating an environment where the sprayed gas speeds up the cutting process and helps the beam cut more efficiently.
Benefits of Improved Laser Cutting Quality
Enhanced accuracy
Quality Increasing the accuracy of laser cutting is one of the most effective ways to improve the quality of the finished product. The precision with which a laser can cut a material depends on the machine’s ability to control beam power and beam position. By improving the accuracy of the laser cutting process, you can gain significant benefits in terms of the quality and precision of your products.
Easier setup and higher profits
profits One of the key benefits of improving laser cutting quality is that it allows for easier setup and higher profits. With improved precision and consistency when slicing materials, the amount of time used setting up each cutting job can be significantly reduced. This, in turn, saves you time and boosts productivity.
Additionally, greater precision with laser cutting can also result in a higher quality finished product. With a better looking product, you can charge higher prices for it and make more money.
Improved end product quality
When it comes to increasing the quality of laser cutting, three key areas come into play: effective cutting, improved end product quality, and benefits of improved laser cutting quality. In this blog post, we will be looking at effective methods for improving the quality of laser cutting, as well as understanding the key benefits of improved laser cutting quality. Improving end product quality is often the primary goal when it comes to laser cutting.
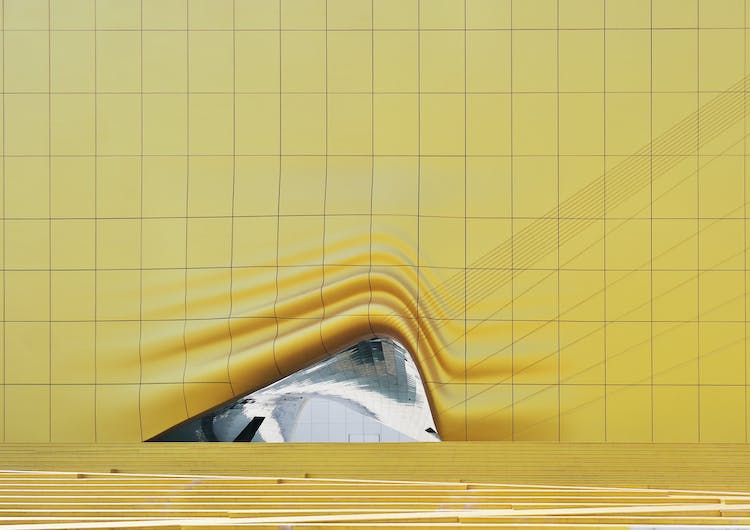
How do you prevent dross in laser cutting?
Quality One key to improving laser cutting quality and preventing dross is to ensure that all parts involved in the cutting process, including the nozzle, optics, and focussing lens, are in correct alignment and that the nozzle is the correct distance from the material being cut. Poor alignment or incorrect distance can cause the material to heat unevenly, resulting in a poor cut or the presence of dross, which can cause further issues. When setting up for laser cutting, it is also important to make sure the gas pressure and mixture ratios are correctly adjusted.
The gas pressure should be sufficient enough to evacuate all the melted material during cutting.
Conclusion
Summary of improving laser cutting quality
Quality In conclusion, there are many effective ways to improve laser cutting quality. Taking the time to understand and experiment with the various settings and parameters can really pay off in terms of increasing overall product quality and reducing waste.
Final thoughts
Quality The final takeaway from this article is that effective laser cutting requires an understanding of the technology, equipment, and processes that come together to make a successful cut. There is no one-size-fits-all solution, as different laser cutting projects will require different techniques and processes. However, by taking the time to research the best method for each particular job, following all safety protocols, and practicing proper maintenance, the quality of laser cutting can be significantly improved.
Doing so can help protect the longevity of the equipment, save money in the long run, and ensure an accurate, high-quality cut every time.
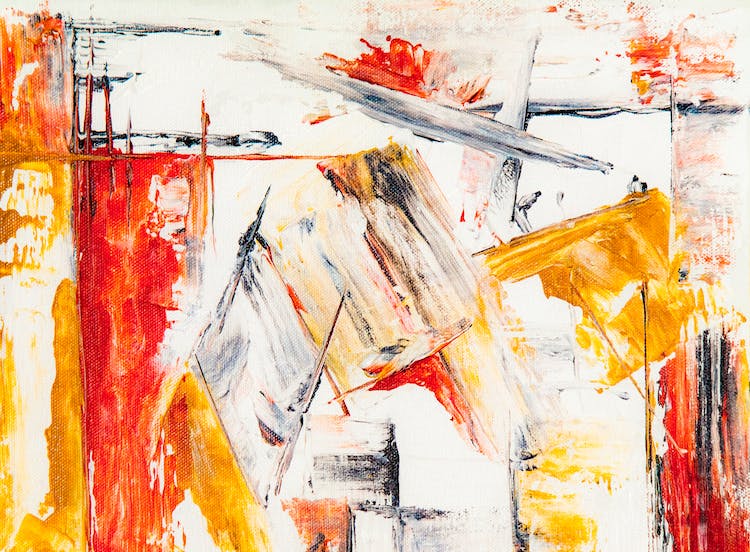