When it comes to laser cutting quality control, one of the most important aspects is reducing the possibility of errors. Quality control for laser cutting should always be done carefully and routinely to guarantee the best possible outcome for a product. This article will explain how to minimize errors when laser cutting through quality control methods and practices.
Reasons why laser cutting quality control is important
Unforeseen risks
When it comes to laser cutting, ensuring quality is an incredibly important task and something that cannot be overlooked. Unforeseen risks can become a serious issue if the proper quality assurance measures are not taken. As laser cutters get more and more complex, they create more and more intricate designs, thus making the potential for error all the more costly.
Preventing damage to materials
One of the most important aspects of laser cutting quality control is preventing damage to the material being cut. High quality cuttings are not just based on aesthetics, but also include factors like accuracy and ensuring that no damage is done to the material during the process.
Identifying Quality Control Problems
Mistakes in set-up
When it comes to laser cutting, set-up can be one of the most crucial components of ensuring good cut quality and quality assurance. Mistakes in the set-up process can cause a host of issues that result in poor cut quality, errors and rework down the line. Mistakes during the set-up of the laser cutting machine can arise from a number of sources.
Machine installation
Quality control starts with machine installation. The first step is to ensure that the laser cutting machine is properly installed and calibrated for optimal cut quality. To do this, it’s important to install the machine in an environment free from dust, vibration, and direct sunlight.
Doing this helps to reduce the chance of any potential issues occurring with the cutting process. It’s also important to ensure that the laser cutting machine is correctly connected to the power source and has the right settings applied. This includes setting the right power, gas, and air pressure to ensure the optimal cutting results.
Material selection
When it comes to minimizing error with laser cutting quality control, one of the most important factors to consider is your material selection. The kind of material you choose to use will have a direct impact on the overall cut quality. Different materials have different properties that can affect the cutting process, such as reflectivity and the levels of heat that the material is able to generate.
For example, some materials require a higher power setting to ensure a clean cut, while others require lower power settings to avoid damage. If you use materials with high reflectivity, the laser is likely to cause damage, too.
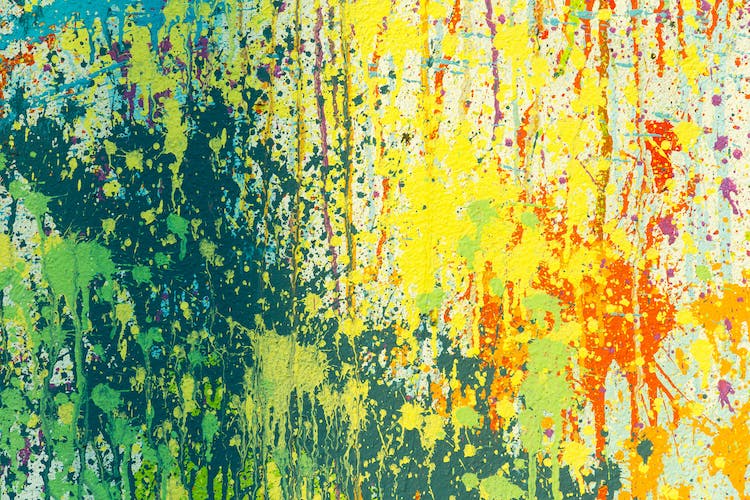
Strategies to Minimize Errors in Laser Cutting Quality Control
Consider the features of the laser cutting machine
One of the most important aspects to consider when seeking to minimize errors in laser cutting quality control is the features of the laser cutting machine itself. Whether you are using a gas, solid-state, or pulsed-laser, each type has its own quirks that must be taken into account to ensure cut quality and consistency. Gas lasers, for example, have been around since the 1960s and are particularly adept at cutting thicker materials.
However, they are generally more expensive and require more maintenance than other laser cutting machine types.
Establish preventative measures
When it comes to minimizing errors with laser cutting quality control, setting up preventive measures is a great way to reduce the number of mistakes that can occur. Having a robust quality assurance process in place specifically tailored to the specific laser cutting applications can help to decrease the potential for errors. It may be helpful to start by analyzing the current production process and documenting the causes of cut quality errors.
Next, review the process and develop potential strategies or modifications to reduce or prevent the problems that are causing quality errors. Consider if procedures should be updated or equipment needs to be replaced or modified.
Review maintenance and operational processes
When it comes to laser cutting, achieving a perfect cut every time requires a methodical approach to both maintenance and operational processes. Taking the time to review and regularly assess these processes can help to minimize errors in laser cutting quality control. When it comes to maintenance, regular assessments of your laser cutting machine can help to ensure the machine is in optimal running condition.
Things like checking for signs of wear and tear in parts, inspecting for any fluid or air leaks, and regular servicing of lenses, mirrors and other related components should all be taken into account to keep a laser cutting machine running in tip top shape.
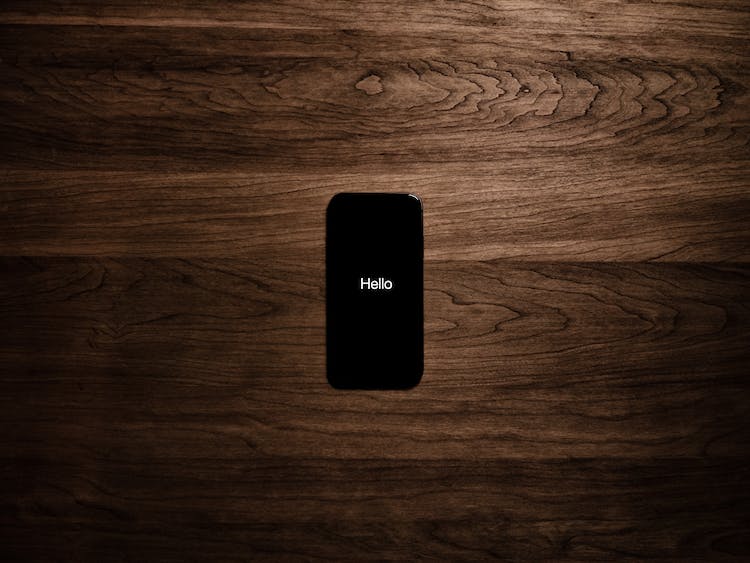
Conclusion
Summary of laser cutting quality control information
In conclusion, laser cutting quality control is an important part of any laser cutting process. Quality control ensures that the cut is as precise and accurate as possible. There are a variety of methods for measuring and evaluating the quality of laser-cut products, including laser power, feed rate, and cutting speed, as well as regular monitoring of the material being cut.
Additionally, there are a number of checks that can be performed prior to production to minimize error, such as calibrating the laser and double-checking measurements against a CAD design. By using these tips, manufacturers can ensure the highest quality of laser-cut products, minimize error, and save time and money.
Tips for a successful quality control process
The implementation of quality control for laser cutting processes is an important step for ensuring error minimization and the satisfaction of clients. With the right tools, processes and oversight, laser cutting quality control can help to improve product quality significantly and ensure that the desired outcome is achieved.
- Educate your operators and production staff on all machine operators, settings, and adjustment procedures.
- Develop standard operating procedures for each product to minimize errors, such as confirming material characteristics, verifying cutting paths, validating nested parts for cutting, and documenting job results.
- Perform periodic laser cutting system maintenance to reduce laser cutting errors due to contaminated optics and misalignments.
- Establish a consistent inspection program, using the proper measurement technology, to ensure that each product meets the quality requirements.
- Implement a system to correct errors as they occur and provide feedback to operators on correcting any errors they make.
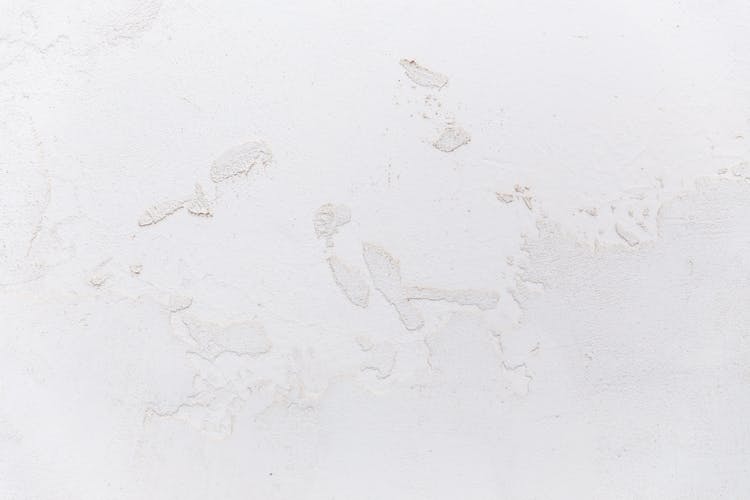