Optimizing the rate of laser cutting can help businesses to reach maximum efficiency levels whilst producing excellent quality output. With the right approach to laser cutting, businesses can save money, move projects forward in a shorter timeframe, and get the best possible returns on their investment. In this article, we will be looking at how to optimize your laser cutting rate for maximum efficiency. Through key strategies and tips, we will discuss the methods you can use to get your laser cutting projects completed quickly and to a high standard.
Preparing Your Laser Cutter
Choosing the Right System
When it comes to optimizing your laser cutting rate for maximum efficiency, one of the most important decisions you need to make is selecting the right system for your needs. The speed at which you are able to cut your material directly correlates with productivity, so it is essential to choose a system with the appropriate cutting speed for your project. Oftentimes, people select laser cutting machines that have a slow cutting speed and do not allow for the most efficient rate of cutting.
Maintaining the Cleanliness of the System
One of the most important factors involved in optimizing your laser cutting rate for maximum efficiency is maintaining the cleanliness of the system. A laser cutter is an intricate machine, so it needs to be treated with respect and regular cleaning. Dust, debris, and build-up on its components can cause an array of issues and lead to a decrease in efficiency (and in some cases damage to the unit).
One way to reduce the build-up of dust and other contaminants is to equip your laser cutting system with the necessary intake and exhaust filtering systems. This ensures that only clean air comes in contact with the laser’s internal components, allowing for higher cutting speeds and better performance.
Optimizing the Gas Pressure Settings
height Optimizing the gas pressure settings for your laser cutter is a great way to maximize its efficiency and improve the cutting speed. The most important factor to consider when setting the gas pressure on a laser cutter is the thickness and type of material being cut. The gas pressure needs to be set within the manufacturer’s recommended range to ensure a quality cut.
The higher the gas pressure, the more intense the laser beam is, allowing it to cut faster.
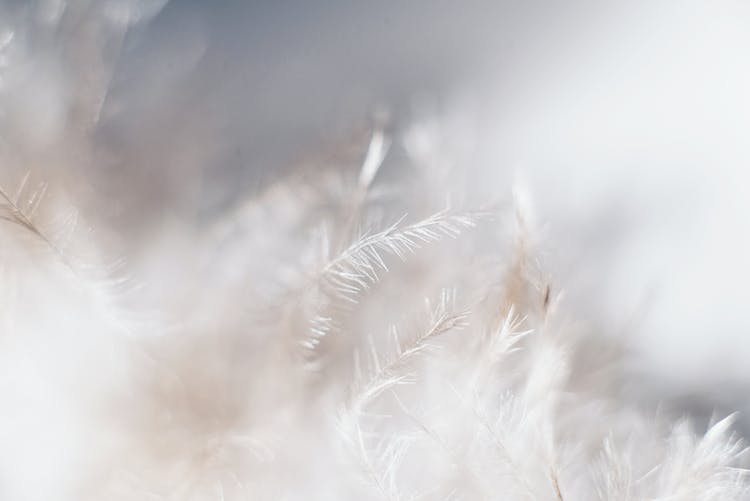
Calculating the Optimal Cutting Rate
Understanding Laser Cutting Process Variables
Understanding Laser Cutting Process Variables The key to maximizing efficiency when it comes to laser cutting is understanding the variables associated with the process. Speed, power, and clearance are the three primary variables to consider. Speed and power are the two most important factors when it comes to laser cutting rate for maximum efficiency.
Your speed should be adjusted based on the cutting material, thickness of the material, and your desired accuracy level. Power should also be adjusted as needed to ensure a successful cut. When looking at the actual cutting rate, this will also depend on the type of laser used.
Setting the Right Machinable Material Thickness and Toolpaths
passes Setting the Right Machinable Material Thickness and Toolpaths Setting the right machinable material thickness for your laser cutting job is essential for optimizing speed and efficiency. The thickness of your material will determine the cutting speed of the beam – thicker materials require more peak power and laser heat energy, which results in much slower cutting speeds than with thinner material.
Establishing the Optimal Laser Power Settings
Establishing the optimal laser power settings for a laser cutting job can be essential in order to achieve the best results and produce optimally efficient results. One of the keys to optimizing the laser cutting process is setting the correct power level. The power setting needs to be determined based on the type of job you are doing and the material you are cutting.
Different materials usually require different power levels and the size of the material can also impact the power setting. The ideal power level for cutting any material is that which provides the best combination of cutting speed and precision.
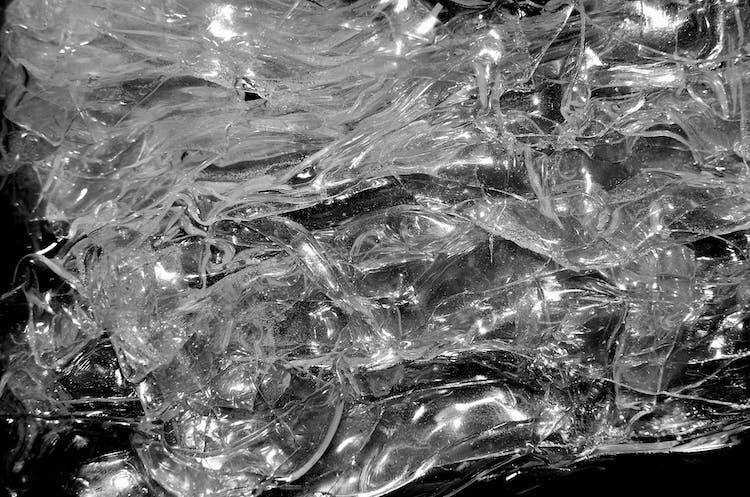
Adopting Best Practices to Increase Efficiency
Determine the Right Cutting Speed
time When it comes to optimizing the rate at which your laser cuts, determining the right speed is essential for maximum efficiency. Laser cutting speeds vary depending on the kind of laser you’re using, the type of raw material you’re cutting, and your end goal. Laser cutting speeds range anywhere from 0.00 inches per second (IPS) to up to 4.2 m/s (meters per second).
Maximize Throughput with Automated Settings
time Optimizing laser cutting rate for maximum efficiency means adopting the best practices to make sure that the laser cut is as fast and efficient as possible. By changing the settings to maximize throughput, laser cutting speeds can be increased up to 4.2 m/sec. The best way to optimize your laser engraving is to make sure that the correct tools are being used.
Fibre optical lasers are more efficient and faster when cutting raw material than gas lasers. Also, it is important to reduce cutting head lift time, as it can cause delays when the cutting head has to be moved from one area to another.
Reduce Cycle Times with Automation
times One of the most effective ways to increase the efficiency of laser cutting is to reduce the cutting cycle time. This is achieved by automating the process to determine the optimal cutting speed for each job. Automated cuts will adjust the speed of the laser to account for different materials and thickness.
In addition, this can also minimize scrap and downtime, increasing the productivity of the machine overall.
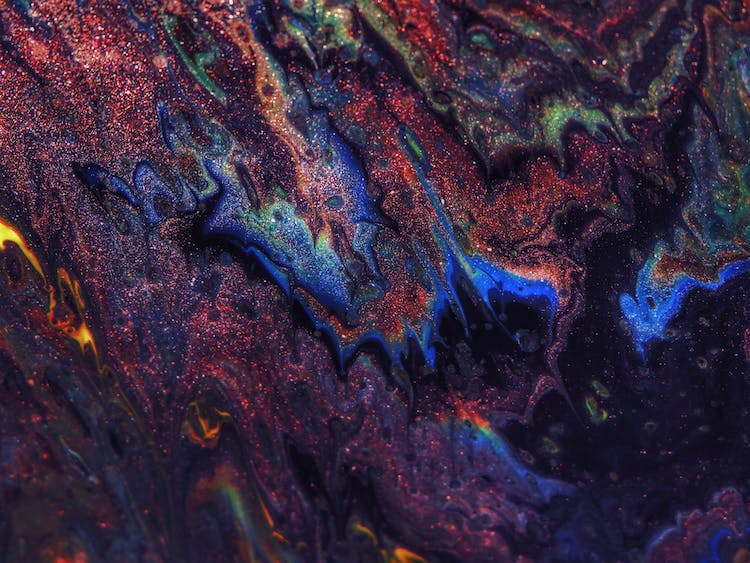
Conclusion
Summary of Proven Methods for Optimizing Laser Cutting Rate
time In conclusion, optimizing your laser cutting rate for maximum efficiency is an important and achievable goal. By following recommended tactics like switching to a more efficient laser type, such as fiber optical lasers, and reducing cutting head lift time, you will be able to speed up your laser cutting from your current rate of 2.4 m/sec to 4.2 m/sec or even increase efficiency by 30%. You can also take advantage of advanced computer hardware and software to speed up the process and increase precision.
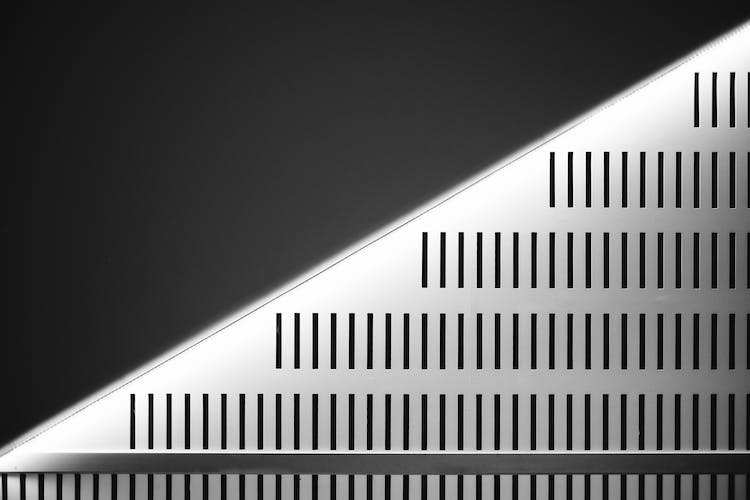