Laser cutting zinc for various craft projects can be a challenge for those who are new to the process. In this article we will look at some common issues that arise when laser cutting zinc and provide tips for troubleshooting them. We will cover topics such as temperature settings, burn marks, and machine setup. With the help of this information, you should be able to optimize your laser cutting capabilities when using zinc. Let’s begin!
Pre-Cutting Steps
Ensuring the machine is setup properly
in laser cutting When it comes to troubleshooting common issues when laser cutting zinc, one of the most important pre-cutting steps is ensuring your machine is setup correctly. It can be difficult to troubleshoot any laser cutter issues if the machine isn’t properly set up from the beginning, meaning any progress you make in cutting zinc could be hindered by a faulty or incorrect setup.
Choosing the correct settings for the job
When it comes to laser cutting zinc, the right settings can make the difference between a precise cut and an unsatisfactory job. To make sure you’re set up for success, it’s important to have the right settings for the job. The most common problems encountered when laser cutting zinc are too little focus power, slow cutting speed, and improper gas pressure.
Too little focus power can cause the laser beam to spread and not penetrate the metal enough to get a precise cut. Furthermore, setting the cutting speed too low can make the laser less responsive and can cause the edges to melt away and create a rough cut.
Adjusting ventilation
Adjusting ventilation is one of the most important steps in troubleshooting common issues when laser cutting zinc. Zinc is a metal that produces hazardous fumes when it is cut with a laser cutter. Without proper ventilation, fumes and deadly gases can linger in the air and become hazardous to both the operator of the laser cutter and any other people in the area.
It is important to ensure that the ventilation system in the workspace is functioning properly before beginning laser cutting.
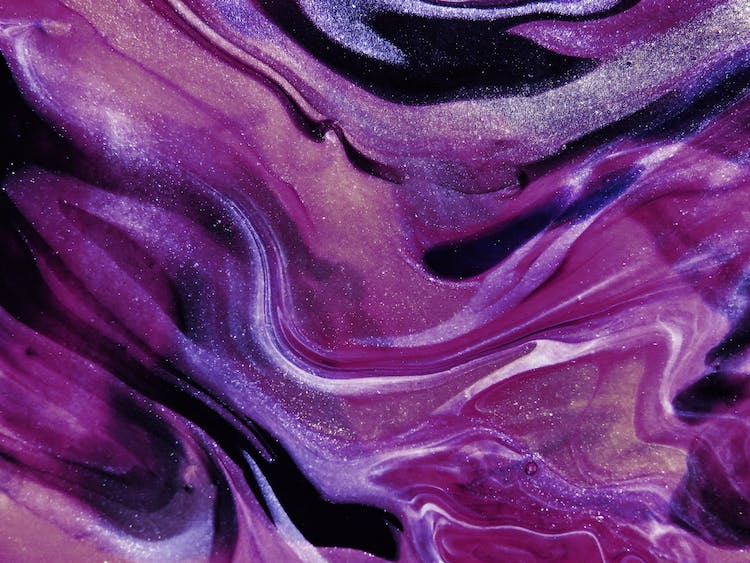
During the Cutting Process
Monitoring cut quality
with Monitoring cut quality when laser cutting zinc during the cutting process is key to ensure a successful outcome. The process can be especially tricky as zinc is a material that’s quite susceptible to melting and warping, complicating the machine’s ability to make precise and clean cuts. To help mitigate this, it is important to monitor the cut quality throughout the process to ensure it is up to the necessary standards.
Common issues that arise when laser cutting zinc include warping, melting, uneven cuts, and coating damage. Warping occurs when the material starts to bend, due to uneven heating across the zinc surface.
Testing for gas type that works best
When laser cutting zinc, there are some common issues that can arise during the cutting process. If you are running into issues, it’s important to correctly troubleshoot and identify the source of the problem in order to minimize production downtime and maximize efficiency. One of the common problems when laser cutting zinc is testing for the right gas type.
When cutting metals with a laser cutter, the metal is heated during cutting and vaporized to create a cut. In order to increase the accuracy and efficiency of cutting, a stream of pressurized gas is sent along the cutting path during the cutting process.
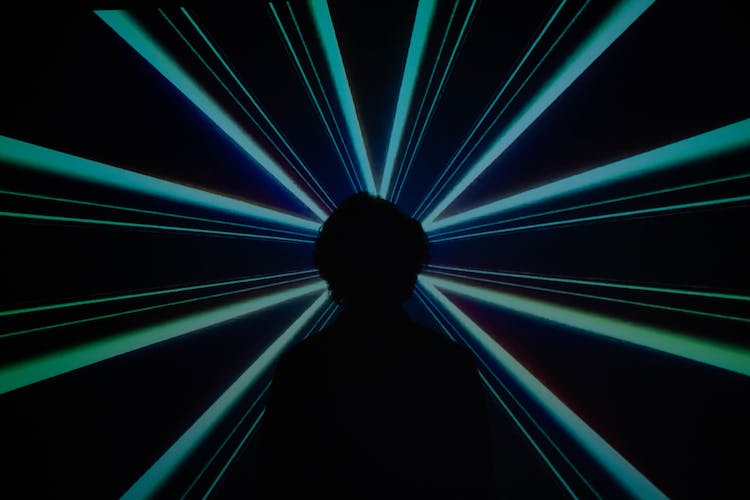
Troubleshooting
Inspection of parts
Inspection of parts is one of the most important steps when troubleshooting common issues when laser cutting zinc. While laser cutting zinc, the parts that are produced should be inspected carefully to determine if there are any defects present. This is especially true when laser cutting thin parts, as any imperfections can cause the part to become damaged or break.
Inspection of parts should include checking for any dents, burrs, bends, or other defects that could limit the part’s performance.
Strategies for addressing issues
When laser cutting zinc, there are many potential issues that can occur. Some of the most common issues include laser misalignment, poor quality of cut, too high of a cutting speed, poor surface finish, and damage to the material. In order to ensure successful results when laser cutting zinc, it is important to understand the best strategies for addressing these common issues.
Conclusion
Summary
Summary: When laser cutting zinc, it is important to be aware of the common issues that can occur and how to troubleshoot them. Specifically, the most common issues when laser cutting zinc include charring, dross, and sharp angles. To prevent these from occurring and ruining the finish of the zinc, be sure to adjust the focus of the laser cutter, use the correct cutting speeds, and include extra support.
Additionally, it is important to practice a trial run first to ensure that the finished product is free of any common issues. Overall, with the right knowledge and experience, laser cutting zinc can be successfully completed with beautiful and accurate results.
Resources for further information
Conclusion This article has discussed the common issues that can occur when laser cutting zinc, as well as some tips and tricks to help you troubleshoot these issues. While issues due to the laser cutter itself can often be addressed using the manufacturer’s instructions and resources, it is important to also understand the physical and chemical properties of the material being cut to help optimize the cutting process.
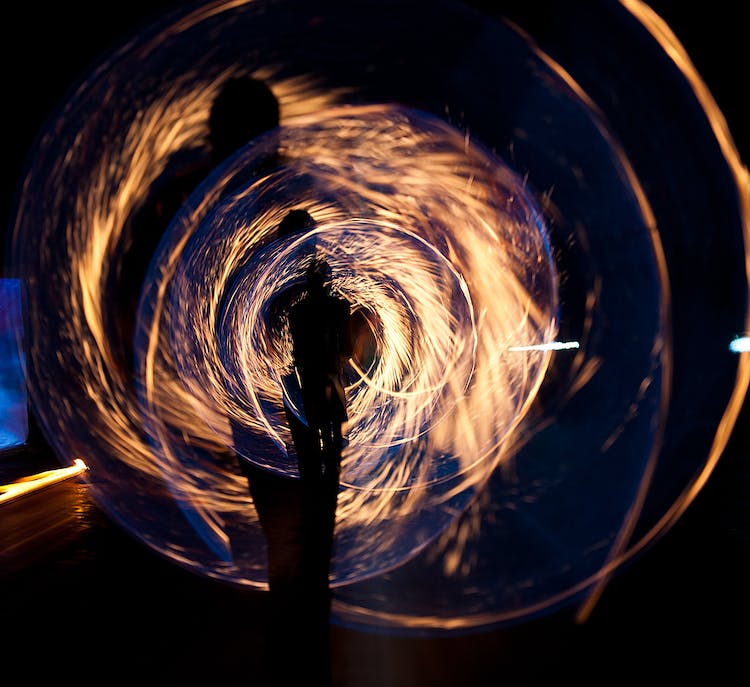